1、引言
鈦合金具有比強度高、重量輕、耐腐蝕、導(dǎo)熱率小、彈性模量小、非磁性及線膨脹系數(shù)小等特性,是再生冷卻結(jié)構(gòu)推力室噴管的理想材料[1]。相同量級發(fā)動機若采用鈦合金噴管可以減輕重量,大幅提高發(fā)動機的推質(zhì)比,使液體火箭發(fā)動機的綜合水平得以提升,有效提高運載火箭發(fā)動機的運載能力[2]。
現(xiàn)役液體火箭發(fā)動機推力室擴張段內(nèi)外壁多采用不銹鋼材料,不銹鋼雖具有良好的塑性和切削性能,但相較于低密度且高強度的鈦合金,在液體火箭發(fā)動機擴張段上的應(yīng)用劣勢較為明顯,推質(zhì)比大打折扣,對發(fā)動機性能提升有較大的制約。
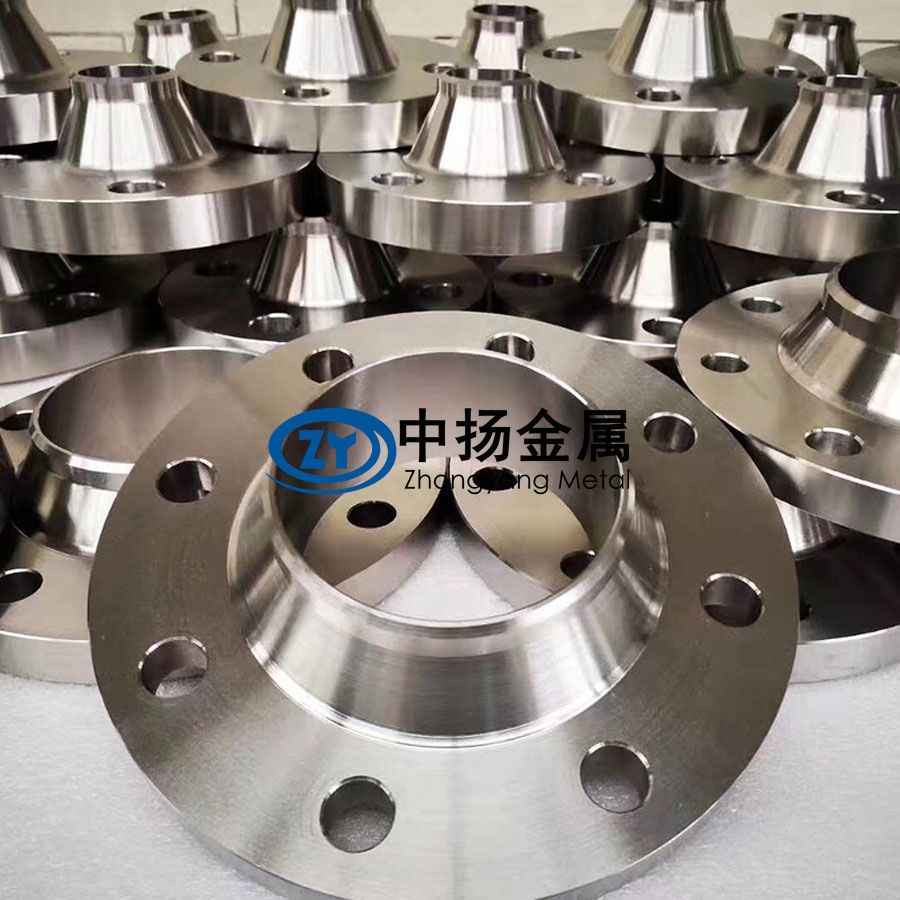
隨著我國制造生產(chǎn)水平和工藝技術(shù)的穩(wěn)步提升,已經(jīng)在某大型液體火箭發(fā)動機推力室擴張段上應(yīng)用了鈦合金材料。雖然鈦合金材料具有獨特的優(yōu)勢,但其加工工藝難度大,不僅在鈑金熱成型工藝中較不銹鋼的成型精度差,而且切削加工性較低,主要體現(xiàn)在:鈦合金導(dǎo)熱性能差,切削過程產(chǎn)生的切削熱聚集在工件與刀具的接觸區(qū)域,刀具磨損快,非特制切削液不能發(fā)揮良好的冷卻效果;鈦合金在溫度600℃以上時硬度顯著上升,加速刀具磨損;鈦合金塑性低,彈性變形大,加工過程中已加工表面與刀具后刀面的接觸面積增大,降低切削性能[3]。
液體火箭發(fā)動機推力室擴張段內(nèi)外壁均屬鈦合金大型薄壁結(jié)構(gòu)件,針對其難加工特性,通過專用刀具開發(fā)、程序優(yōu)化和參數(shù)優(yōu)化等技術(shù)手段,經(jīng)大量的切削試驗驗證研制出適用于鈦合金大型薄壁件的工藝技術(shù)方案,使加工效率獲得顯著提升。
2、零件加工技術(shù)難點
2.1零件結(jié)構(gòu)特點
某型液體火箭發(fā)動機推力室擴張段內(nèi)壁(簡稱內(nèi)壁)小端直徑約1000mm,大端直徑約1800mm,大小端端面距離約1300mm,壁厚4mm,徑厚比250~450,且內(nèi)壁銑槽后槽底剩余壁厚最小為0.6mm,徑厚比高達3000,屬于典型的大型薄壁件。內(nèi)壁由鈦合金鈑金件拼焊脹型而成,脹型過程中,內(nèi)壁壁厚經(jīng)歷剪切—拉伸復(fù)合運動,是多因素綜合作用下的彈塑性變形過程,由于母線為非線性曲線,內(nèi)壁不同部位的壁厚變化量不同。
鈦合金材料彈性模量小、常溫下塑性差、各向異性系數(shù)大、成型后回彈大且冷成型極易開裂,導(dǎo)致內(nèi)壁的鈑金成型難度極大,需采用熱成型模式,而熱成型對零件的形狀、表面質(zhì)量和尺寸精度影響很大,在大尺寸薄壁曲母線鈦合金內(nèi)壁中表現(xiàn)更為明顯。在整個熱成型過程中,成型溫度區(qū)間、間隙選擇、進給率和主軸轉(zhuǎn)速等因素對產(chǎn)品精度控制有很大影響,造成其表面輪廓度差,與設(shè)計理論型面偏差較大,所設(shè)計的工裝無法與其平穩(wěn)緊密貼合,尤其在大端軸向400mm范圍內(nèi)存在大面積未貼合現(xiàn)象。
工件需加工近300條縱向均布直槽,倘若刀具壽命不穩(wěn)定,頻繁換刀將占用大量生產(chǎn)時間。
在加工過程中,拼焊、脹型時形成的應(yīng)力會緩慢釋放,工件局部產(chǎn)生變形,容易造成產(chǎn)品幾何尺寸超差;另一方面,工件表面均布近300條槽,壁厚由4mm減薄到0.6mm,金屬去除量大,這一過程會同時出現(xiàn)應(yīng)力的產(chǎn)生與釋放,同樣會促使產(chǎn)品變形,造成工件與工裝局部不貼合。圖1為產(chǎn)品結(jié)構(gòu)示意圖。
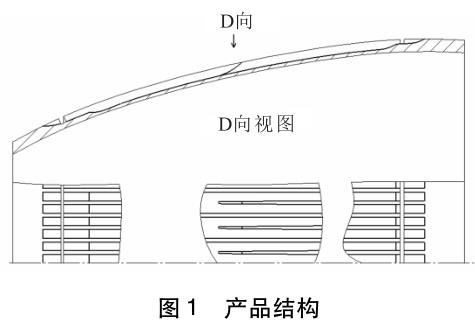
2.2加工技術(shù)難點
鈦合金材料固有的特性決定了其切削性能差,鈦合金大型薄壁件不僅具備鈦合金材料難切削的特點,而且銑槽毛坯鈑金件的剛性差,更加劇了銑槽加工難度。與其他碳鋼相比,鈦合金與刀具材料件的摩擦系數(shù)更大,而切屑變形系數(shù)遠小于其他材料,切屑與前刀面的摩擦速度大,接觸界面溫度高,刀具更易磨損[4]。鈦合金在高溫下化學(xué)活性高,能與空氣中的氫、氧、氮發(fā)生化學(xué)作用形成脆性層,降低材料塑性,并使切屑與前刀面的接觸長度減小,加劇刀具磨損。
由于鈦合金大型薄壁件成型難度大且型面精度差,內(nèi)壁與工裝胎具不貼合,刀具切削加工過程中抗振性差,刀具磨損嚴重,難以保證槽深和筋寬等技術(shù)指標,產(chǎn)品報廢率高。
該型號內(nèi)壁結(jié)構(gòu)尺寸遠大于現(xiàn)有銑槽件,由于現(xiàn)有銑槽設(shè)備的裝夾空間、承重能力和采樣軟件處理能力不足,對于大型薄壁件的裝夾存在困難。
鈦合金銑槽時存在刀具磨損嚴重和報廢頻繁等問題,加工一件產(chǎn)品因崩刃、斷齒等原因會報廢高速鋼銑刀約100片,高速鋼刀具加工鈦合金的適用性低。雖然硬質(zhì)合金刀具比高速鋼刀具更適合銑削鈦合金,但由于冷卻不足,單件內(nèi)壁需消耗硬質(zhì)合金銑刀約30多片,耗費刀具價值約10萬元。為充分冷卻需使用大流量乳化液澆注(流量>5L/min),造成冷卻液大量耗費且污染環(huán)境。
由于頻繁換刀及返修刀具損壞造成尺寸超差,銑槽效率低,加工1件鈦合金產(chǎn)品用時約480h,而同樣結(jié)構(gòu)尺寸的不銹鋼產(chǎn)品僅需160h。
以上技術(shù)難點導(dǎo)致鈦合金薄壁件噴管銑槽加工存在質(zhì)量差、物耗能耗高、清潔程度低、加工效率低以及生產(chǎn)周期長等問題,改進鈦合金薄壁件銑槽工藝技術(shù)改革方案勢在必行。
3、解決方案
為解決鈦合金薄壁件內(nèi)壁的銑槽加工難點,本文通過專用刀具、切削參數(shù)和加工方法三個方面對其進行工藝研究。
3.1刀具方案
分別采用現(xiàn)有的超硬高速鋼鋸片銑刀、涂層高速鋼鋸片銑刀和涂層硬質(zhì)合金鋸片銑刀進行加工實驗,每種鋸片銑刀采用相同的切削參數(shù),對鈦合金試板進行銑削加工,實際切削長度如表1所示。
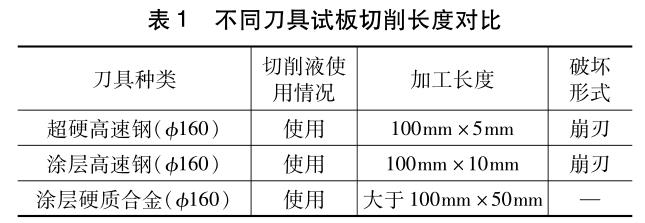
通過鈦合金試板銑削實驗對比,在試板貼和良好的情況下,涂層硬質(zhì)合金片銑刀的耐用性和耐磨性均遠好于高速鋼片銑刀。
通過對試板的加工,初步掌握了鈦合金片銑刀的切削轉(zhuǎn)速、切削深度及進給量的選用范圍。
考慮到實際產(chǎn)品的加工長度和貼合情況遠比試板的裝夾情況差,且大端存在軸向400mm范圍內(nèi)與胎具不貼合的情況,使用三組刀具在最佳轉(zhuǎn)速和切削深度的情況下對產(chǎn)品進行試加工,加工情況如表2所示。
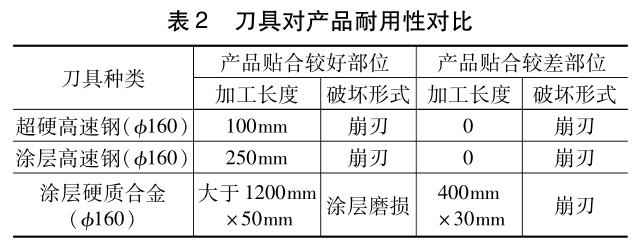
通過實驗對比得知,在產(chǎn)品貼合較差的部位,由于切削過程中產(chǎn)生的振動很大,容易對刀具造成結(jié)構(gòu)性破壞,導(dǎo)致刀具的使用壽命大幅下降。
涂層硬質(zhì)合金片銑刀的失效形式也由涂層磨損變成了崩刃,如圖2所示。
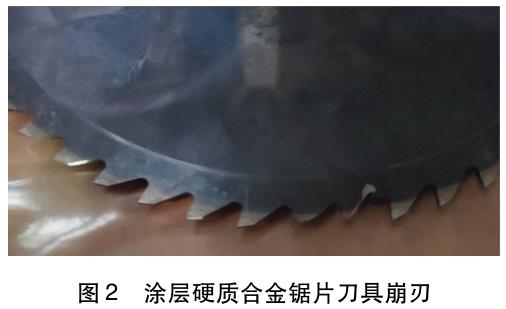
具崩刃不僅極易造成產(chǎn)品扎刀,而且大幅降低了整體式硬質(zhì)合金片銑刀的耐用性。在降低產(chǎn)品質(zhì)量的同時,提高了加工成本,因此需要針對產(chǎn)品特點對加工參數(shù)和加工方法進行優(yōu)化。
3.2加工方法與參數(shù)優(yōu)化
3.2.1加工技術(shù)
火箭發(fā)動機擴張段內(nèi)壁再生冷卻通道銑削加工技術(shù)依托數(shù)字化激光仿形直槽銑槽機加工[5],具有如下特點:①以銑槽處外表面作為母線基準,采用激光微位移傳感器對每條槽對應(yīng)的外表面進行掃描采樣,消除了采樣位置與銑槽位置不一致帶來的槽深誤差;②對于要求剩余等壁厚的銑槽件,不僅外表面母線采用精確的激光采樣技術(shù),而且以工件的實際原始壁厚為依據(jù)建立工件壁厚數(shù)據(jù)庫,通過軟件獲取槽底軌跡,精確控制槽底剩余壁厚;③該技術(shù)不僅能加工等槽深和等剩余壁厚的槽,而且能在同一條槽上完成指定槽深加工,將原來多道工序合并為一道工序,提高加工質(zhì)量的同時提升了加工效率。
噴管數(shù)字化加工工藝流程見圖3。
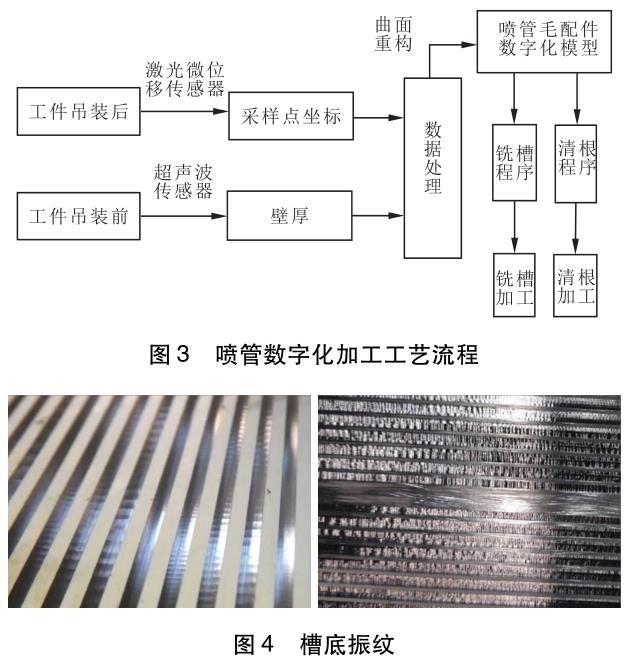
3.2.2加工方法
試加工時,在貼胎較差部位出現(xiàn)刀具壽命大幅降低的情況,同時刀具磨損導(dǎo)致銑槽槽底因振動產(chǎn)生振紋(見圖4)。由于產(chǎn)品不貼胎,導(dǎo)致鈦合金薄壁固定性差,鈦合金材料的切削回彈現(xiàn)象被成倍放大,在按相同切削深度的數(shù)控程序加工情況下,產(chǎn)品貼胎較差部位比貼合良好部位最終槽深要淺0.3~0.5mm,嚴重超出設(shè)計范圍。
解決上述問題,針對激光采樣仿形得到的型面結(jié)合產(chǎn)品的實際貼合狀態(tài),采用分區(qū)域處理。通過調(diào)整進給速度和槽深回彈補償分區(qū)域?qū)Ω鞣N貼合狀態(tài)進行獨立設(shè)計加工參數(shù),保證銑槽光潔度和槽深尺寸滿足設(shè)計要求。
鈦合金的彈性模量僅有鋼的一半且屈強比大,在切削加工時鈦合金零件容易產(chǎn)生較大變形。擴張段II段內(nèi)壁大端超過250mm范圍內(nèi)不貼胎,銑槽時出現(xiàn)讓刀現(xiàn)象,每條槽的槽深不一致(見表3),大端不貼胎處的槽深較貼胎處淺0.2~0.3mm,主輔兩個銑頭加工區(qū)域的槽深誤差和貼胎情況不一致。針對上述情況,采取下列措施來解決槽深超差問題。

(1)主輔側(cè)分別單頭加工。
(2)軸向分段銑槽,分別控制槽深。
檢測每條槽的槽深,標注槽深超差區(qū)域。
經(jīng)過分析、辨別、比對,不貼胎區(qū)域的槽深與貼胎區(qū)域槽深差別較大,將是否貼胎作為分段加工的界限。每條槽在整個槽長范圍內(nèi)整體采樣,在進行加工程序處理時設(shè)置不同的槽長,軸向分兩段加工。距大端250mm作為分段界限,先加工貼胎情況較好區(qū)域,距大端250mm開始至小端銑槽結(jié)束,此區(qū)域貼胎較好,采用原來的加工參數(shù),連續(xù)加工數(shù)十條,具體條數(shù)根據(jù)周向圓跳動決定。大端開始至距大端250mm處作為第二段銑槽區(qū)域,為了保證兩端能夠很好地對接,銑槽位置超出250mm。
(3)兩端分別采用不同的加工參數(shù)。
靠小端區(qū)域貼胎情況好,無讓刀現(xiàn)象,大端區(qū)域不貼胎且剛性差,銑槽時存在讓刀現(xiàn)象,在銑槽深度設(shè)置時注意監(jiān)控槽深。
主軸轉(zhuǎn)速為96r/min,進給量為44~66mm/min。
(4)采用高速鋼銑刀加工貼胎好的區(qū)域,剩下的不貼胎區(qū)域留給硬質(zhì)合金銑刀加工。雖然采用分段加工,但是大端不貼胎區(qū)域依然斷刀頻繁,銑槽較難。為了加快研制進度,采用高速鋼銑刀暫時加工貼胎良好的區(qū)域,貼胎不好的大端采用硬質(zhì)合金銑刀銑槽。
鈦合金薄壁件與胎具的貼合間隙為0.1~3mm,通過分區(qū)域加工技術(shù),不僅保證了在該貼合狀態(tài)下的最快加工速度、加工效率和刀具耐用度,大幅降低了加工成本,而且可以通過對該區(qū)域的銑槽深度進行參數(shù)補償,保證產(chǎn)品整體槽深的一致性。
3.2.3參數(shù)優(yōu)化
鈦合金對變形速度敏感,應(yīng)在低速條件下進行加工。鈦合金彈性模量低、回彈大、易變形以及彈性模量低,已加工表面容易產(chǎn)生較大回彈,而且薄壁零件的回彈更為嚴重,會引起零件在機加工過程中刀具偏離,難以保證產(chǎn)品精度。
需要進行鈦合金銑槽加工參數(shù)的研究(主軸轉(zhuǎn)速、吃刀深度和切削速度等),解決鈦合金回彈帶來的加工精度下降。
經(jīng)試驗驗證,硬質(zhì)合金銑刀最佳切削參數(shù)為進給量0.015mm/z,刀具直徑φ154mm~φ160mm,齒數(shù)Z=32,主軸轉(zhuǎn)速S=180r/min,進給速度選擇F=90mm/min。每齒進給量=F/(S×Z)=90/(180×32)=0.0156mm。
不貼胎處選擇主軸轉(zhuǎn)速S=90r/min,進給速度選擇F=44~66mm/min最佳。
優(yōu)化前后的加工工件對比如圖5所示。
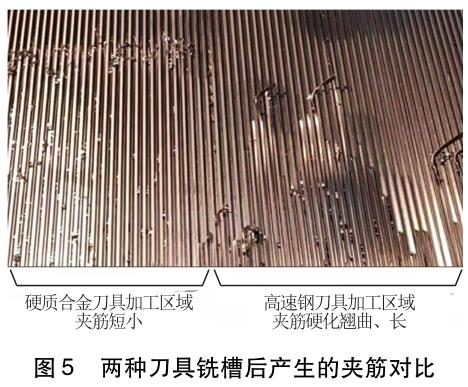
結(jié)語
本文解決了某型液體火箭發(fā)動機推力室擴張段內(nèi)壁的鈦合金銑槽難題。該技術(shù)不僅大幅縮短了加工周期,節(jié)省了加工成本,極大提升了液體火箭發(fā)動機的整體性能,具有良好的經(jīng)濟效益和社會效益。
通過對專用刀具開發(fā)、切削參數(shù)優(yōu)化和加工方法提升三個方面的研究,得出以下結(jié)論。
(1)鈦合金材料大型薄壁件銑槽刀具優(yōu)先采用硬質(zhì)合金材料的鋸片銑刀,無論是刀具耐用度、加工效率、銑槽質(zhì)量還是加工用的高速鋼鋸片刀具都比硬質(zhì)合金鋸片刀具更差。
(2)大型薄壁件剛性差,銑槽夾具的設(shè)計很關(guān)鍵,適當?shù)奶ゾ哐b夾可以解決整體加工系統(tǒng)剛性差的問題。
(3)鈦合金材料大型薄壁件的貼胎程度對銑槽槽深有明顯影響,可以采用分片加工的工藝方法解決不貼胎造成的讓刀問題。
(4)鈦合金材料大型薄壁件的貼胎程度對刀具耐用度以及產(chǎn)品表面質(zhì)量有較大影響,后續(xù)要著力解決鈦合金材料大型薄壁件的成型問題,確保與胎具貼合。
(5)采用數(shù)字化仿形銑槽技術(shù)可以解決大型薄壁件輪廓度差的問題。
參考文獻
[1]呂嗣孝,周洪,崔建坤.鈦合金材料切削加工參數(shù)優(yōu)化和實驗研究[J].機械工程師,2022(1):154-156.
[2]譚永華.中國重型運載火箭動力系統(tǒng)研究[J].火箭推進,2011,37(1):1-6.
[3]朱衛(wèi)華,王宗園,任軍學(xué),等.TC4鈦合金薄壁件銑削殘余應(yīng)力變形研究[J].組合機床與自動化加工技術(shù),2020(12):70-72,79.
[4]閆凱強,黃曉斌,張仕杰,等.面銑刀銑削鈦合金時切削參數(shù)對切削力影響規(guī)律的仿真[J].工具技術(shù),2022,56(4):80-83.
[5]盧杰持,胡力耘,楊金奎,等.火箭大噴管數(shù)控仿形銑槽控制系統(tǒng)[J].大連理工大學(xué)學(xué)報,1998,38(3):296-299.
第一作者/通信作者:劉林,碩士,高級工程師,西安航天發(fā)動機有限公司,710100西安市
FirstAuthor/CorrespondingAuthor:LiuLin,Master,SeniorEngineer,Xi′anSpaceEngineCompanyLimited,Xi′an710100,China
無相關(guān)信息