引言
鈦合金具有低密度、高比強度、高溫力學性能、抗沖擊振動以及耐腐蝕等特點,已經廣泛應用于航空航天領域,尤其是在飛行器上表現(xiàn)出無可比擬的減重優(yōu)勢[1]。
自 20 世紀 80 年代開始,我國將鈦合金材料用于制造緊固件,并且隨著我國制造技術水平的提升,鈦合金緊固件(鈦合金螺絲)大量應用于航天航空工業(yè)[2]。據相關資料顯示,每架國產 C919 大飛機約需鈦合金緊固件 20 萬件,按計劃年產 150 架計算,每年需要 3 000 萬件鈦合金緊固件[2]。
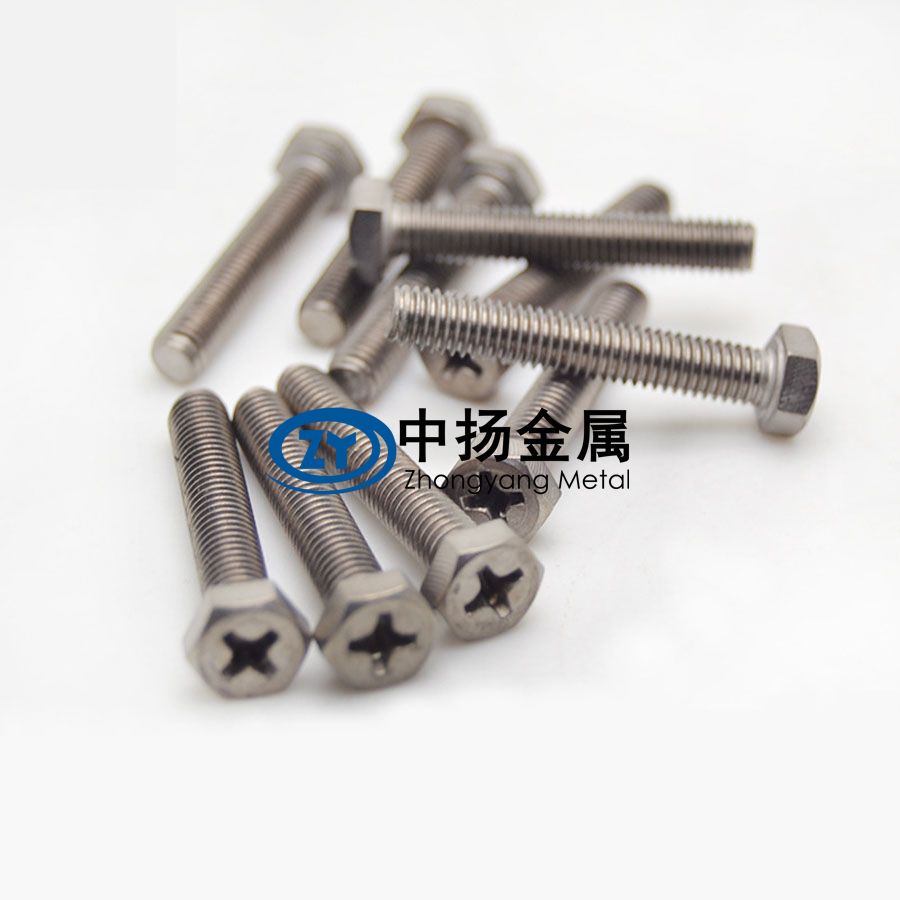
由于鈦合金緊固件表面存在著致密氧化膜,膜層的保護作用使其表現(xiàn)出優(yōu)異的耐腐蝕性能,但是當鈦合金緊固件處于潮濕的海洋環(huán)境時,當接觸到鋁合金、結構鋼等異種金屬構件時,由于不同金屬之間存在著電位差,導致鋁合金、結構鋼等構件較易出現(xiàn)電偶腐蝕現(xiàn)象。
為了減少電偶腐蝕現(xiàn)象,國內外學者研究開發(fā)了多種鈦合金表面處理和改性技術,如離子注入、陽極氧化、物理氣相沉積、金屬鋁涂層等,以及采用濕的底漆或彈性密封膠進行裝配等方法[4]。但是這些表面處理技術存在諸多問題,比如生產周期長、處理效率低、加工成本高、工藝復雜、效果不理想等諸多問題,不利于鈦合金緊固件在航空領域的批量化工程化應用。微弧氧化技術(M A O )是近些年發(fā)展起來的一項新的防護技術,它是通過熱化學、等離子體化學、電化學的共同作用下,在 Ti、A l、M g 等材料表面原位生長形成一層陶瓷氧化膜[3]。該層陶瓷氧化膜具有優(yōu)異的電絕緣性、耐蝕性、耐磨性以及較高的硬度。
國內針對鈦合金材料的微弧氧化技術以及耐磨性改性技術開展了很多研究[4-5],但對鈦合金緊固件典型結構的微弧氧化技術以及耐腐蝕行為還未開展深入研究。本文通過在 TC4 鈦合金緊固件上采用四種不同的工藝參數制備微弧氧化膜層,研究了最適合緊固件結構的工藝模式,同時考察其微弧氧化膜層的抗電偶腐蝕性能,并分析討論了其抗電偶腐蝕行為。
1、 試驗
1.1 試驗材料及設備
TC 4 鈦合金緊固件(M 5 雙線螺栓)制備微弧氧化膜層,TC 4 鈦合金的化學成分(以質量分數計)為:A l(5.5~6.8)% ,V (3.5~4.5)% ,F(xiàn)e ≤ 0.3 % ,Si ≤ 0.15 % ,O ≤ 0.2 % ,C ≤ 0.1 % ,N ≤ 0.05 % ,H ≤ 0.015 % ,其他 ≤ 0.4 % ,Ti 余量。
試 驗 所 使 用 的 偶 對 試 樣 為 2 0 2 4 鋁 合 金 試 片(70 m m ×150 m m ×10 m m ),其化學成分(以質量分數計)為:Cu 4.50 % ,M g 1.30 % ,M n0.50 % ,F(xiàn)e < 0.50 % ,Si < 0.50 % ,Cr < 0.10 % ,A l 余量。先預噴漆處理(預噴涂底涂)。試驗設備采用雙極性疊加脈沖 M A O 裝置。
1.2 工藝研究試驗件制備
采用鈦合金磷酸鹽基礎配方電解液,電參數采用恒流模式與分段模式(先恒流再恒壓)。頻率為 600 H z、占空比 10 % 、氧化時間 15 m in,分段式設立三組參數,分別為 2 段式,3 段式,4 段式。表 1 為制備膜層的電壓參數。
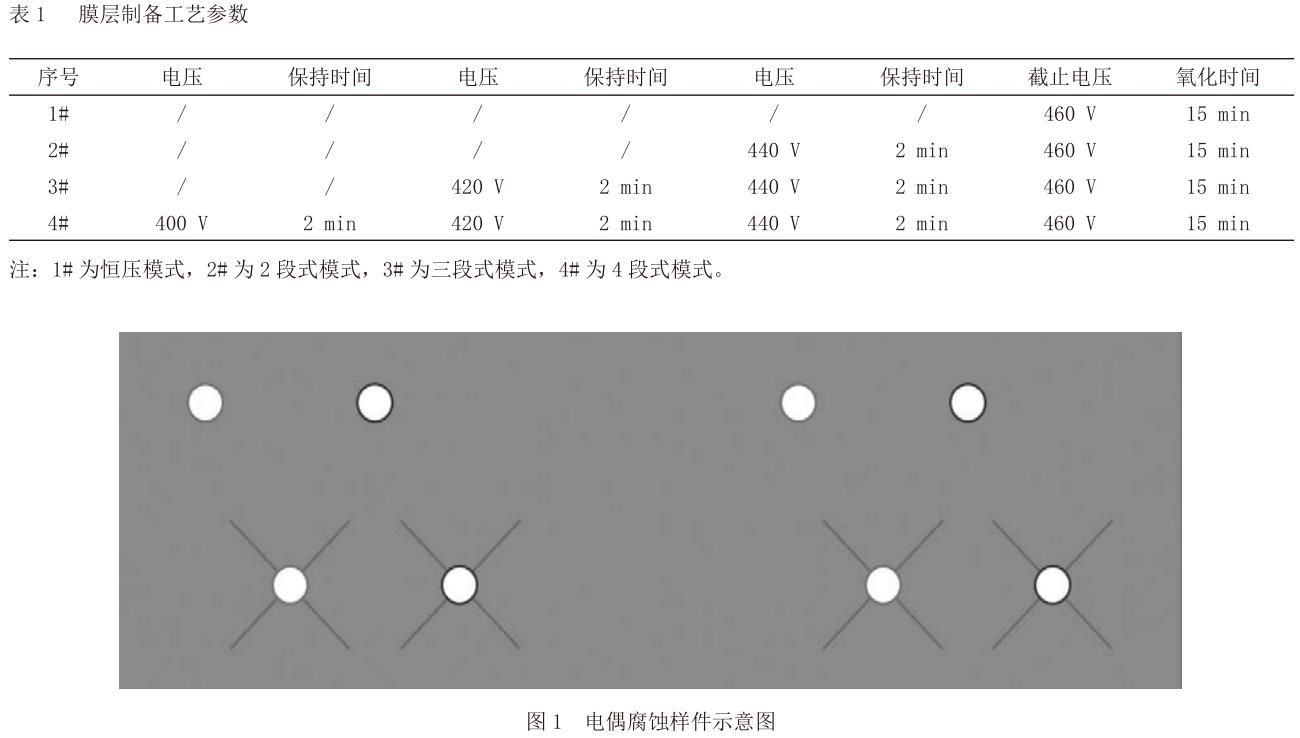
1.3 耐蝕性研究試驗樣件制備
航空緊固件區(qū)域是承受高載荷和潮濕環(huán)境最集中的區(qū)域,與其連接的鋁合金蒙皮材料極易發(fā)生電偶腐蝕,因此模擬航空緊固件的工作模式設計了電偶腐蝕試驗件(如圖 1)。采用噴漆預處理后的 2024 鋁合金試板,按圖 1 的加工方式打孔及劃格。
圖 1 中,孔為 M 5 螺釘配套通孔,劃出“×”狀刻紋,線寬 0.5 m m 、長 1.27 m m 長。緊固件分別為尺寸 M 5 的鈦合金(裸)、鈦合金(M A O )、尼龍緊固件。
1.4 性能測試
采用三維體式顯微鏡、X 射線晶體衍射儀、電化學工作站分別對微弧氧化膜層進行分析。
依據 G B/T 10125-2012 開展持續(xù)鹽霧試驗,500 h、1000 h 以及 3 000 h 后,脫漆處理后,觀察鋁合金表面腐蝕情況。
2、 結果與討論
2.1 微弧氧化工藝研究
以三種不同的工藝參數,制備的膜層,依次編號1#、2#、3#、4#,從膜層微觀形貌、厚度、顯微硬度三個方面,分析恒流模式與分段式工作模式對膜層性能的影響。
圖 2 為工藝參數下 TC4 鈦合金緊固件微弧氧化層的膜層厚度情況,結果顯示,隨著分段保持次數的增多,膜層厚度表現(xiàn)為先降低,再持平。
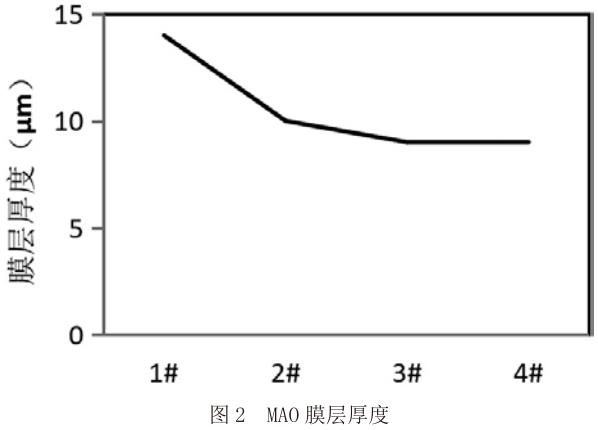
圖 3 為鈦合金緊固件微弧氧化膜層在掃描電鏡下的微觀表面形貌圖。圖中可以清晰地看見膜層表面均存在非常細微的裂紋,這是熱應力和高壓下發(fā)生氧化還原反應所造成的[4]。而且膜層表面均充滿了大量的微孔,這與微弧氧化膜形成的原理緊密相關,反應過程中的火花放電階段會在鋁合金表面形成大量的放電通道,熔融態(tài)的鈦氧化物以類似火山噴發(fā)的方式從這些通道中大量噴濺而出,最終噴濺于表面的氧化鋁經過等離子體高溫、高壓瞬間燒結作用形成晶態(tài)氧化物陶瓷膜[5]。在恒流工作模式下膜層微觀表面有明顯的氧化物堆積,在先恒流再分段式恒壓的工作模式下氧化物堆積減少,在分 4 段式氧化物堆積現(xiàn)象最不明顯,這主要是由于電壓在(400~460)V ,每隔 20 V 時保持停留,2 m in 的恒壓模式對樣件的電場力更均勻、穩(wěn)定,致使形成的膜層更致密、膜層表面的平整度、均勻性得到了顯著提升。
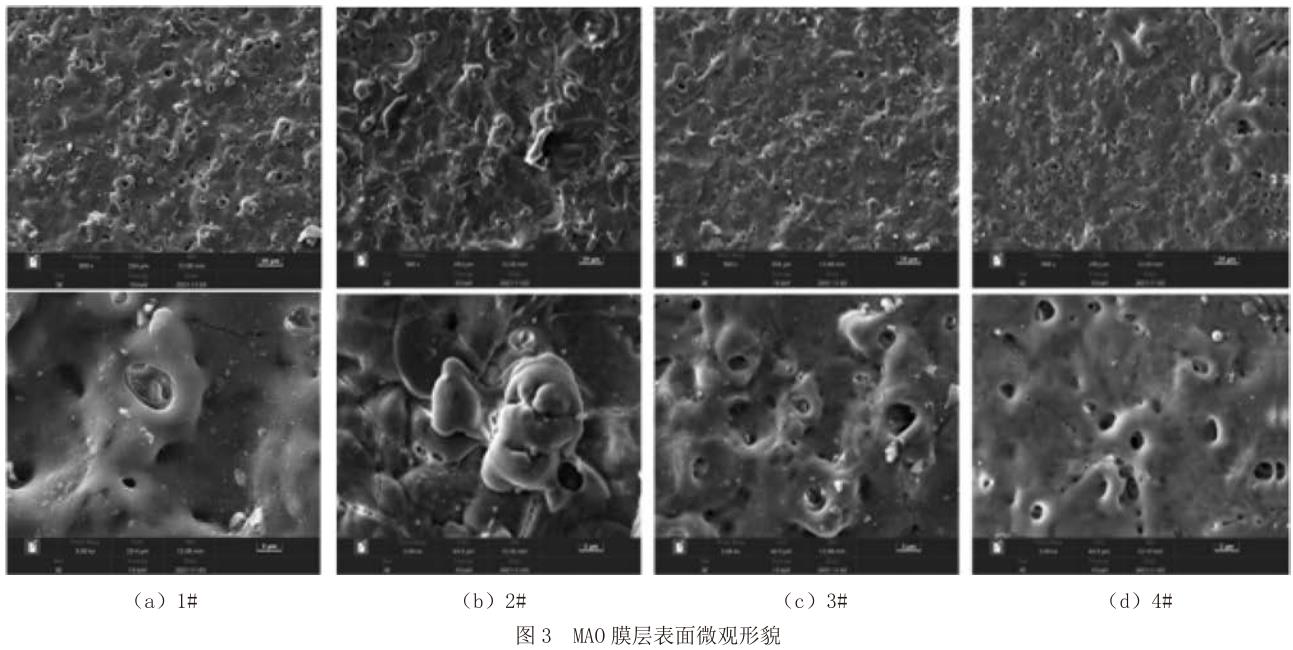
圖 4 為 TC4 鈦合金緊固件表面微弧氧化層的顯微硬度。結果表明,分段式形成的膜層硬度更高,這是因為微弧氧化膜層表面的微孔減小,形成的膜層更致密所致。
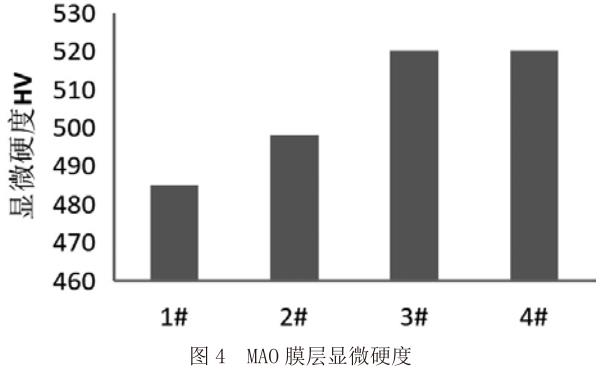
通過本次試驗,對比發(fā)現(xiàn)分 4 段式工作模式形成的微弧氧化膜層性能最優(yōu),因此,鈦合金緊固件微弧氧化層耐蝕性研究采用 4 段式工藝開展。
2.2 耐蝕性研究
通過電化學工作站測試動電位極化曲線,發(fā)現(xiàn)在3.5 % N aCl溶液中,采用微弧氧化處理后陰極電流密度的顯著降低(如圖 5 所示)。
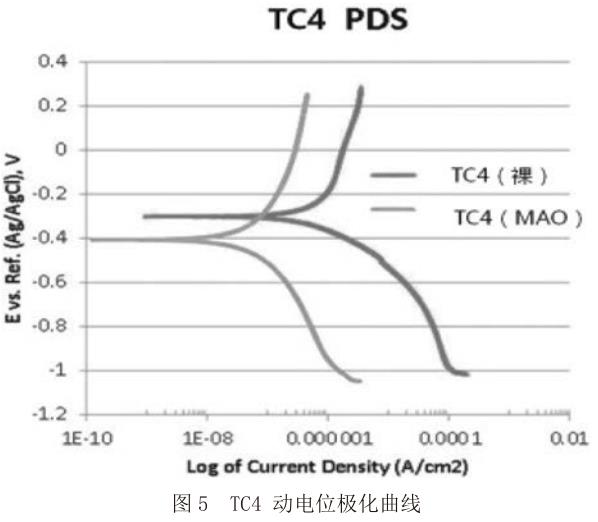
依據 G B/T 10125-2012 標準對試驗件開展耐連續(xù)鹽霧電偶腐蝕試驗,500 h 后去除 2024 面板上的油漆,試驗結果見表 2。試驗表明與鈦合金(裸)緊固件相連接的鋁板上發(fā)生了較嚴重的腐蝕,尤其是刻紋位置,此外,白色腐蝕產物也明顯較多。而與微弧氧化后鈦合金緊固件連接的鋁板在整個測試過程中外觀基本保持不變,只有輕微的變色跡象,去除漆層后發(fā)現(xiàn)鋁基材未發(fā)生明顯腐蝕,與缺乏陰極驅動力的尼龍緊固件情況一樣。這表明采用微弧氧化工藝以后,有效地避免了鈦合金緊固件與鋁合金接觸的電偶腐蝕。
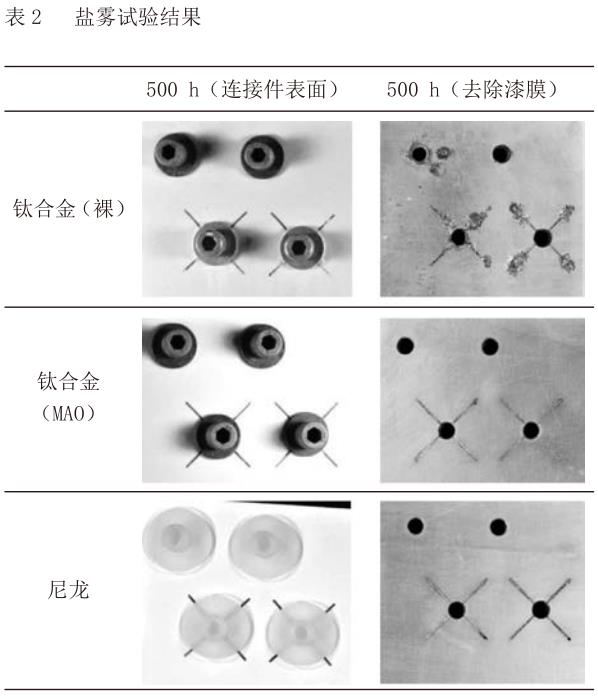
持續(xù)鹽霧腐蝕測試中選擇暴露 500 h 的樣品,用 PPGEl D orado 涂層去除劑進行脫漆,對緊固件與鋁板連接孔截面分析進行微觀形貌分析,分析結果如圖 6 所示。
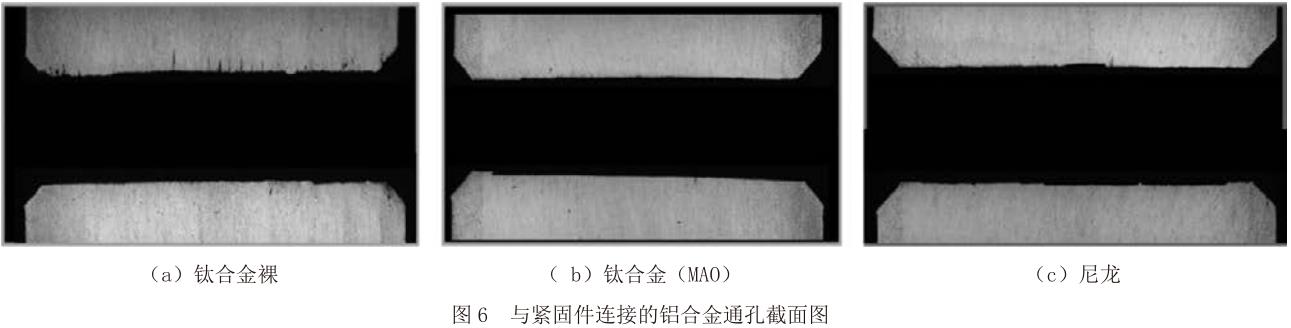
試驗通過觀察截面微觀圖,表明鈦合金(裸)緊固件周圍存在明顯腐蝕,尼龍緊固件在斷面分析中沒有出現(xiàn)腐蝕裂紋,證實了孔內對金屬緊固件的腐蝕攻擊確實是電偶腐蝕驅動的。與裸露的鈦合金緊固件相比,微弧氧化處理的鈦合金緊固件孔內腐蝕明顯降低,與尼龍緊固件相當,表明通過微弧氧化處理可以明顯降低電偶腐蝕。
3、 結論
1)鈦合金微弧氧化膜層表面存在大量微孔,采用4 段式恒定電壓工作模式制備的膜層微孔表面平整度和均勻性提高,且膜層硬度提高、厚度降低更易于裝配和使用。
2)鈦合金螺絲(鈦合金緊固件)采用微弧氧化處理后顯著降低了與鋁合金接觸的電偶腐蝕。
參考文獻 :
[1] 柳鴻飛 , 高玉魁 . 某型飛機螺栓連接結構釘載分配特性研究 [J].航空制造技術 , 2020 (Z2):64-71+101.
[2] 劉彥清 . 民用飛機緊固件選用概述 [J]. 科技視界 , 2020 (4):182-183.
[3] 張毅斌.船用鈦合金表面改性技術研究進展 [J]. 材料開發(fā)與應用 , 2009, 24(5):70-74.
[4] 穆明 , 梁軍 , 肖乾 , 等 . 鈦合金微弧氧化一步制備含石墨的減摩涂層 [J]. 材料科學與工藝 , 2013, 21(1):18-23.
[5] Hongping Duan,Chuanwei Yan, Fuhui Wang. Growth process of plasma electrolytic oxidation films formed on magnesiμm alloy AZ91D in silicate solution [J]. ElectrochimicaActa, 2007, 52(15).
[6] 李均明 . 鋁合金微弧氧化陶瓷層的形成機制及其磨損性能 [D]. 西安理工大學 , 2008.
無相關信息