1 、前言
鈮鉿合金是一種低強(qiáng)度高塑性并且有良好焊接性能的合金,1965 年,美國(guó)研制成功 Nb-10Hf-1Ti 合金,并于 1969年用于阿波羅載人登月艙液體火箭發(fā)動(dòng)機(jī)輻射冷卻噴管延伸
段,1975 年,中國(guó)也研制成功 Nb-10HfTi1Zr0.7 鈮合金。試驗(yàn)證明,我國(guó)研制的鈮鉿合金的主要性能指標(biāo)已經(jīng)達(dá)到國(guó)外同類(lèi)合金的水平。目前能生產(chǎn)直徑 220mm,高 900mm 的鑄錠 ;同時(shí)也能生產(chǎn)直徑 110mm,長(zhǎng) 1200mm~1500mm 的擠壓棒以及各種規(guī)格的板材。
由于鈮鉿合金材料具有特有的高熔點(diǎn),低強(qiáng)度、高塑性并且有良好焊接性能的特點(diǎn),其廣泛應(yīng)用于電子、冶金、鋼鐵、石油、化工、汽車(chē)、通訊、建筑、交通、核能、航空應(yīng)用
及航天航空等領(lǐng)域[1]。
另外,鈮鉿合金是航天工程和技術(shù)中應(yīng)用量最多的一種鈮合金,對(duì)金屬鈮來(lái)說(shuō),它在難熔金屬中具有的出色綜合性能,如熔點(diǎn)高達(dá) 2448℃,比重為 8.57 克 / 立方厘米,在1093℃ ~1427℃范圍比強(qiáng)度最高,溫度低至 -200℃仍有良好的塑性和良好的加工性能,而鈮鉿合金是以鈮為基加入一定量鉿和其他元素形成的鈮合金 , 在二元相圖上,鈮和β-Hf 形成置換固溶體,鉿是一種活性元素,與鈮中的氧和碳化合生成 HfO2 和 HfC 化合物,起彌散強(qiáng)化作用,同時(shí)降低間隙元素的有害影響,改善鈮合金焊接性能和涂層性能 ,從而使它成為在宇航方面優(yōu)先選用的熱防護(hù)材料和結(jié)構(gòu)材料。但是,它的高溫抗氧化性能不好,在 450℃以上必須氧化保護(hù)涂層。具體應(yīng)用場(chǎng)所 :
(1)液體火箭發(fā)動(dòng)機(jī)輻射冷卻噴管延伸段,此種結(jié)構(gòu)簡(jiǎn)單、可靠、適用于承受長(zhǎng)時(shí)間工作和多次起動(dòng),所以多用于頂級(jí)發(fā)動(dòng)機(jī)和宇宙飛行器發(fā)動(dòng)機(jī)。如 ;大力神Ⅲ C 的過(guò)渡級(jí)發(fā)動(dòng)機(jī)噴管延伸段采用輻射冷卻 ;阿波羅載人登月飛船服務(wù)艙發(fā)動(dòng)機(jī)輻射冷卻噴管延伸段 ;阿波羅登月艙下降發(fā)動(dòng)機(jī)輻射冷卻噴管延伸段等等 ;
(2)雙元液體推進(jìn)劑姿控發(fā)動(dòng)機(jī) ;R-4D 反作用控制發(fā)動(dòng)機(jī)是用鈮鉿合金棒材機(jī)加工制成燃燒室 ;阿金納火箭其推力室的燃燒室也是用鈮鉿合金機(jī)加工制成 ;
(3)可伸出噴管民兵Ⅲ第三級(jí)可伸出噴管延伸段方案采用鈮鉿合金制成,長(zhǎng)度約 406 毫米,用 4 個(gè)氣動(dòng)作動(dòng)器在點(diǎn)火幾秒后展開(kāi),噴管面積從 24 加大到 43,提高了推力效率,為提高導(dǎo)彈射程或有效載荷提供了可能。
但是,確保產(chǎn)品正常順利工作和使用的首要條件是產(chǎn)品必須無(wú)任何質(zhì)量問(wèn)題,特別是上面所說(shuō)的應(yīng)用于航天方面的火箭發(fā)動(dòng)機(jī)更是不能有一絲一毫的問(wèn)題,如果當(dāng)產(chǎn)品存在潛在的各種缺陷如裂紋等,不僅無(wú)法保證產(chǎn)品的正常使用,對(duì)航天類(lèi)產(chǎn)品而言,還將由于此問(wèn)題將造成設(shè)備或裝備的致命的損傷,從而導(dǎo)致無(wú)法正常工作,其后果是非常嚴(yán)重的。因此非常有必要明確缺陷的產(chǎn)生原因并提出相應(yīng)的檢測(cè)方法。
在這里,我們僅針對(duì)棒材在機(jī)加工后出現(xiàn)的肉眼可見(jiàn)裂紋缺陷產(chǎn)生原因進(jìn)行分析,并提出相應(yīng)的預(yù)防和解決辦法。
2、 實(shí)驗(yàn)
2.1 實(shí)驗(yàn)用材料來(lái)源及缺陷分類(lèi)
2.1.1 材料生產(chǎn)過(guò)程及來(lái)源
將鈮、鉿、鈦三種合金按一定比例配料,用氬弧焊方法制成電極,在真空自耗電弧爐上經(jīng)兩次熔煉制取鑄錠,然后將鑄錠包鋼套在擠壓機(jī)上開(kāi)坯,再鍛成棒材,經(jīng)機(jī)加至規(guī)定尺寸。
此次收集的棒材為在機(jī)加工生產(chǎn)工序中發(fā)現(xiàn)存在裂紋缺陷的廢品。
2.1.2 缺陷分類(lèi)
依據(jù)發(fā)現(xiàn)裂紋缺陷的部位,分為棒材外表面及側(cè)面存在長(zhǎng)度及深度不等的裂紋、內(nèi)部裂紋及表面較淺的小缺陷三類(lèi)缺陷作為分析對(duì)象。具體為 :圖 1-5 為外表面及側(cè)面存在長(zhǎng)
度及深度不等的裂紋、圖 6-7 內(nèi)部裂紋及圖 8 為表面較淺的裂紋小缺陷。
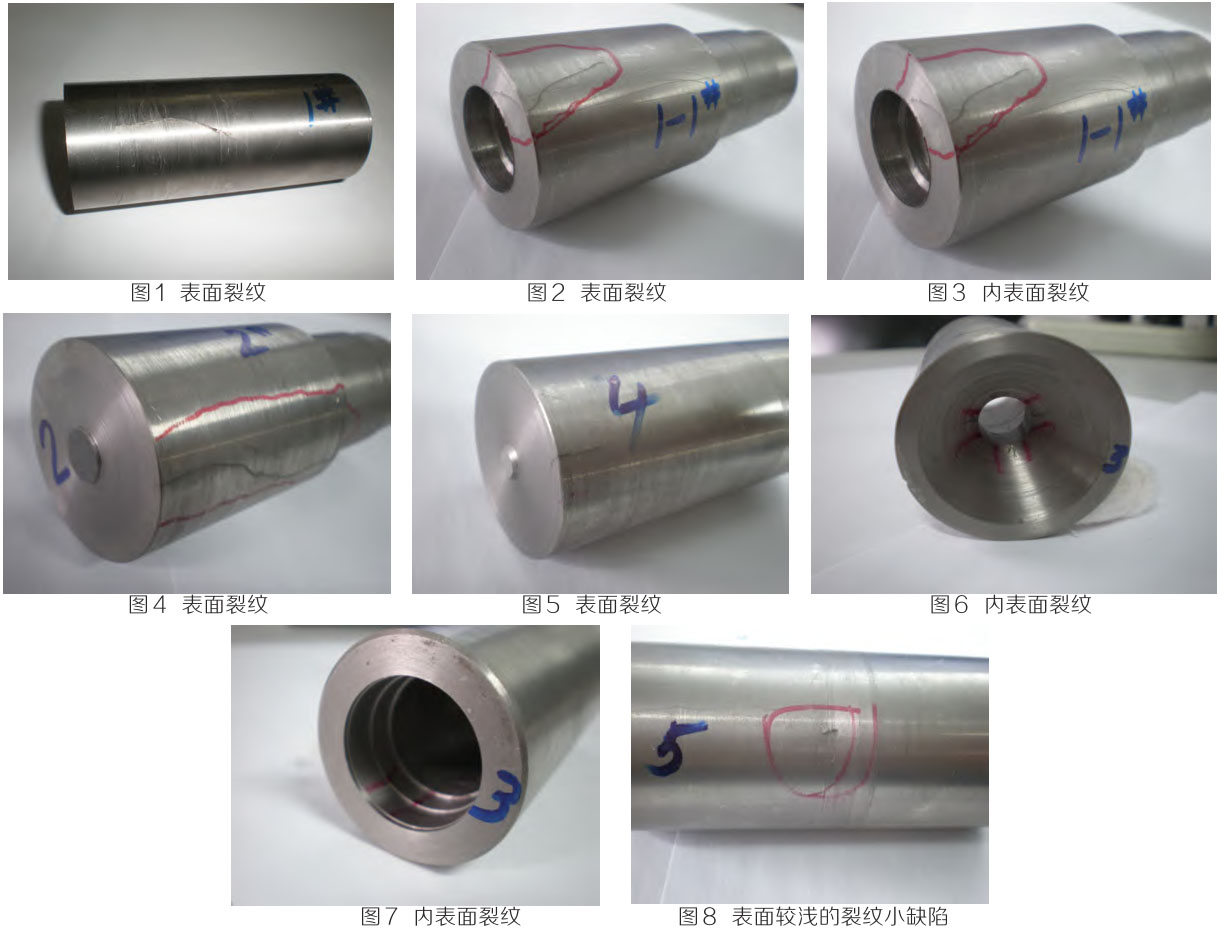
2.2 實(shí)驗(yàn)用檢測(cè)設(shè)備原理及型號(hào)
2.2.1 超聲波探傷儀
(1)超聲波檢測(cè)原理。超聲波檢測(cè)是應(yīng)用最廣泛的無(wú)損檢測(cè)方法之一,超聲波檢測(cè)方法利用進(jìn)入被檢測(cè)材料的超聲波對(duì)材料表面與內(nèi)部缺陷進(jìn)行檢測(cè)。利用超聲波對(duì)材料的宏觀缺陷進(jìn)行探測(cè),依據(jù)的是超聲波在材料中傳播時(shí)的一些特性,如 :聲波在通過(guò)材料時(shí)能量會(huì)有損失,在遇到兩種介質(zhì)的分界面時(shí),會(huì)發(fā)生反射等等,常用頻率為 0.5—25MHz。
通常以來(lái)自材料內(nèi)部各種不連續(xù)的反射信號(hào)的存在及其幅度、入射信號(hào)與接收信號(hào)之間的聲傳播時(shí)間、聲波通過(guò)材料以后能量的衰減的進(jìn)行發(fā)現(xiàn)缺陷并對(duì)缺陷進(jìn)行評(píng)估的基本信息。超聲波檢測(cè)的適用范圍非常廣,可用于各種金屬材料和非金屬材料,從檢測(cè)形狀上來(lái)說(shuō),可以是板材、棒材、管材、鍛件等 ;從缺陷的特點(diǎn)來(lái)說(shuō),既可以是表面缺陷,也可以是內(nèi)部缺陷[2]。
(2)超聲波檢測(cè)設(shè)備型號(hào)。檢測(cè)時(shí)選用武漢中科創(chuàng)新技術(shù)股份有限公司生產(chǎn)的漢威 HS610e 型 A 掃描超聲波探傷儀器,該儀器具有檢測(cè)靈敏度高、可對(duì)缺陷精確定位、操作方便和選用范圍廣的特點(diǎn)。

(3)超聲波檢測(cè)設(shè)備選配探頭。檢測(cè)時(shí)選用廣東汕頭超聲電子股份有限公司生產(chǎn)的 5Z10SJ50XJT 水浸線聚焦探頭( 圖 9) 以及 2.5Z20N直探頭 ( 圖 10)。為保證檢測(cè)過(guò)程中,水浸聚焦探頭始終以固定角度入射到工件上,對(duì)探頭采用馬鞍架固定,并且馬鞍架與工件接觸部位,馬鞍架采用線切割的方法,加工成與工件曲率相同的外形,保證了檢測(cè)的穩(wěn)定性與準(zhǔn)確性,再輔以直探頭,對(duì)直徑方向上的內(nèi)部缺陷進(jìn)行檢測(cè)。
(4)超聲波檢測(cè)對(duì)比試塊選擇。采用與工件相同材質(zhì)的,相同規(guī)格的縱向人工刻槽缺陷以及帶曲率的平底孔試塊??v向人工刻槽缺陷參數(shù)為 3mm×0.1mm×0.05mm(長(zhǎng)× 寬 × 深);平底孔試塊人工缺陷埋深一般用壁厚的 3/4 作為基礎(chǔ)。
(5)超聲波檢測(cè)靈敏度選擇。通過(guò)前期對(duì)檢測(cè)設(shè)備及探頭角度的調(diào)試和確定,最終檢測(cè)時(shí)所用的基礎(chǔ)靈敏度為61.4dB。為了便于發(fā)現(xiàn)缺陷,一般在檢測(cè)時(shí),在基礎(chǔ)靈敏度的數(shù)值上增加 6dB 作為檢測(cè)靈敏度,當(dāng)發(fā)現(xiàn)缺陷時(shí),恢復(fù)至基礎(chǔ)靈敏度作為當(dāng)量的判定,得出該缺陷的當(dāng)量值大小。
2.2.2 X 射線探傷機(jī)
(1)X射線檢測(cè)原理。X射線檢測(cè)技術(shù)是一種重要的無(wú)損檢測(cè)技術(shù),它依據(jù)的是被檢工件由于成分、密度、厚度等的不同,對(duì)射線產(chǎn)生不同的吸收或散射的特性和對(duì)被檢工件的質(zhì)量、尺寸、特性等作出判定[3]。當(dāng)強(qiáng)度均勻的射線束透照射物體時(shí),如果物體局部區(qū)域存在缺陷或結(jié)構(gòu)存在異常,它將改變物體對(duì)射線的衰減,使得不同部位透射射線強(qiáng)度不同,這樣,采用一定的檢測(cè)器(例如,射線照相中采用膠片)檢測(cè)透射射線強(qiáng)度,就可以判斷物體內(nèi)部的缺陷和物質(zhì)分布等。
(2)X射線檢測(cè)設(shè)備型號(hào)及參數(shù)。檢測(cè)時(shí)選用德國(guó)進(jìn)口的飛利浦450X射線探傷機(jī),該機(jī)具有靈敏度高,穿透力強(qiáng)的特點(diǎn);根據(jù)工件材質(zhì)和厚度,通常電壓選用100KV~360KV,電流選用 10mA,透照時(shí)間選用2min; 膠片選用愛(ài)克發(fā)工業(yè)膠片。
3、 實(shí)驗(yàn)結(jié)果
3.1 超聲波檢測(cè)結(jié)果
對(duì)上述三種類(lèi)型的裂紋缺陷進(jìn)行水浸橫波超聲波檢測(cè),其結(jié)果見(jiàn)圖 11-17。
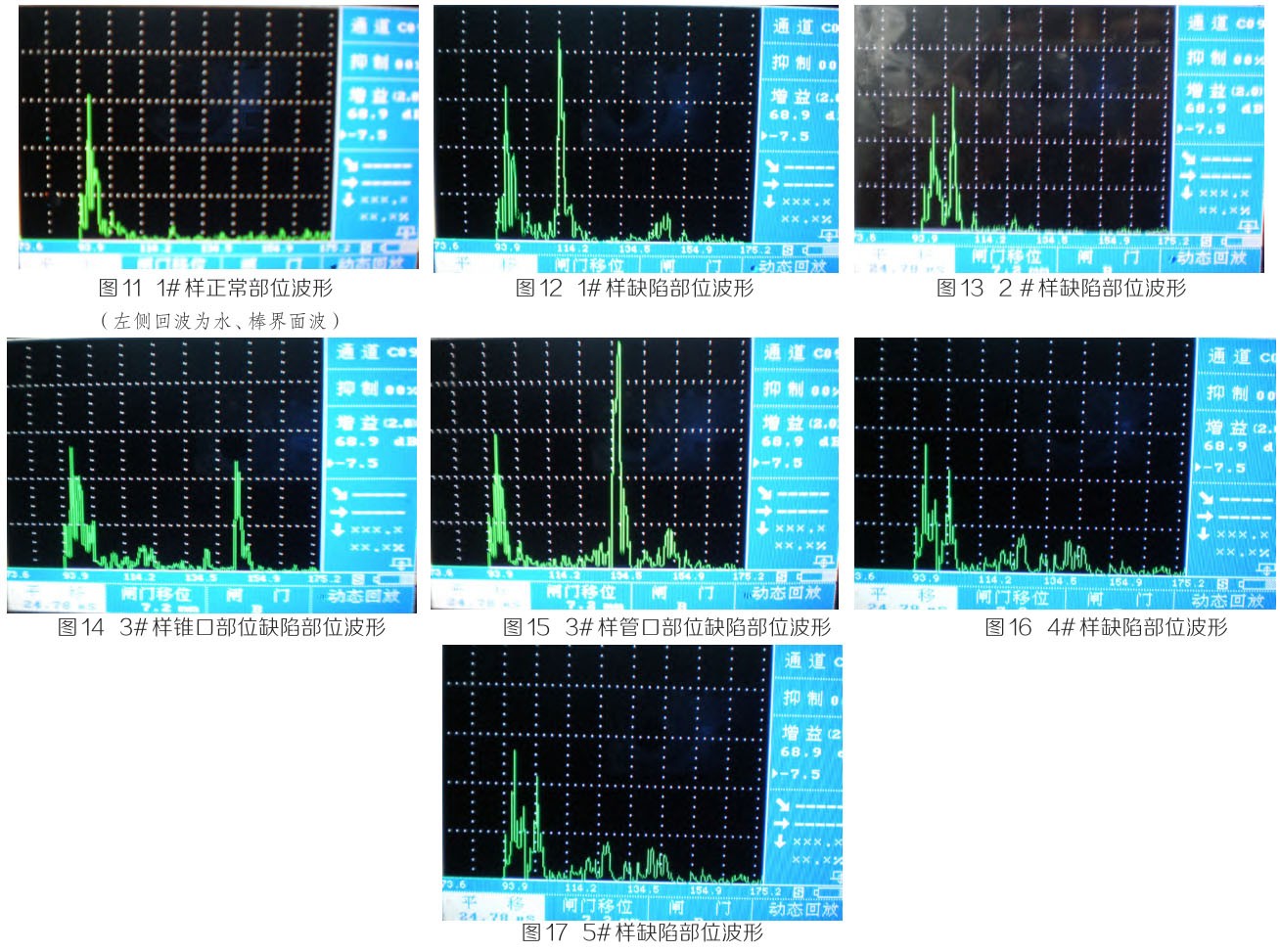
從圖中的檢測(cè)試驗(yàn)情況可以看出,上述三類(lèi)缺陷,通過(guò)超聲波檢測(cè)是可以發(fā)現(xiàn)的。若再進(jìn)一步確定方法,設(shè)計(jì)實(shí)驗(yàn)、確定人工參數(shù)試樣后,該類(lèi)產(chǎn)品中的缺陷是具有可檢性和可控性的。
3.2 X 射線檢測(cè)結(jié)果
(1)選取具有代表性的三種樣品進(jìn)行 X 射線檢測(cè),具體方法是每個(gè)樣品從相互垂直的兩個(gè)方向進(jìn)行 X 射線檢測(cè)。如圖 18-20。
從圖中的檢測(cè)情況可以看出,由于鈮鉿合金比較致密,上述三種樣品中,僅 3# 樣品可以發(fā)現(xiàn)其內(nèi)部存在的缺陷,其它兩種樣品是無(wú)法發(fā)現(xiàn)樣品中所存在的缺陷的。
(2)檢測(cè)結(jié)果如下 :如圖 21-26。
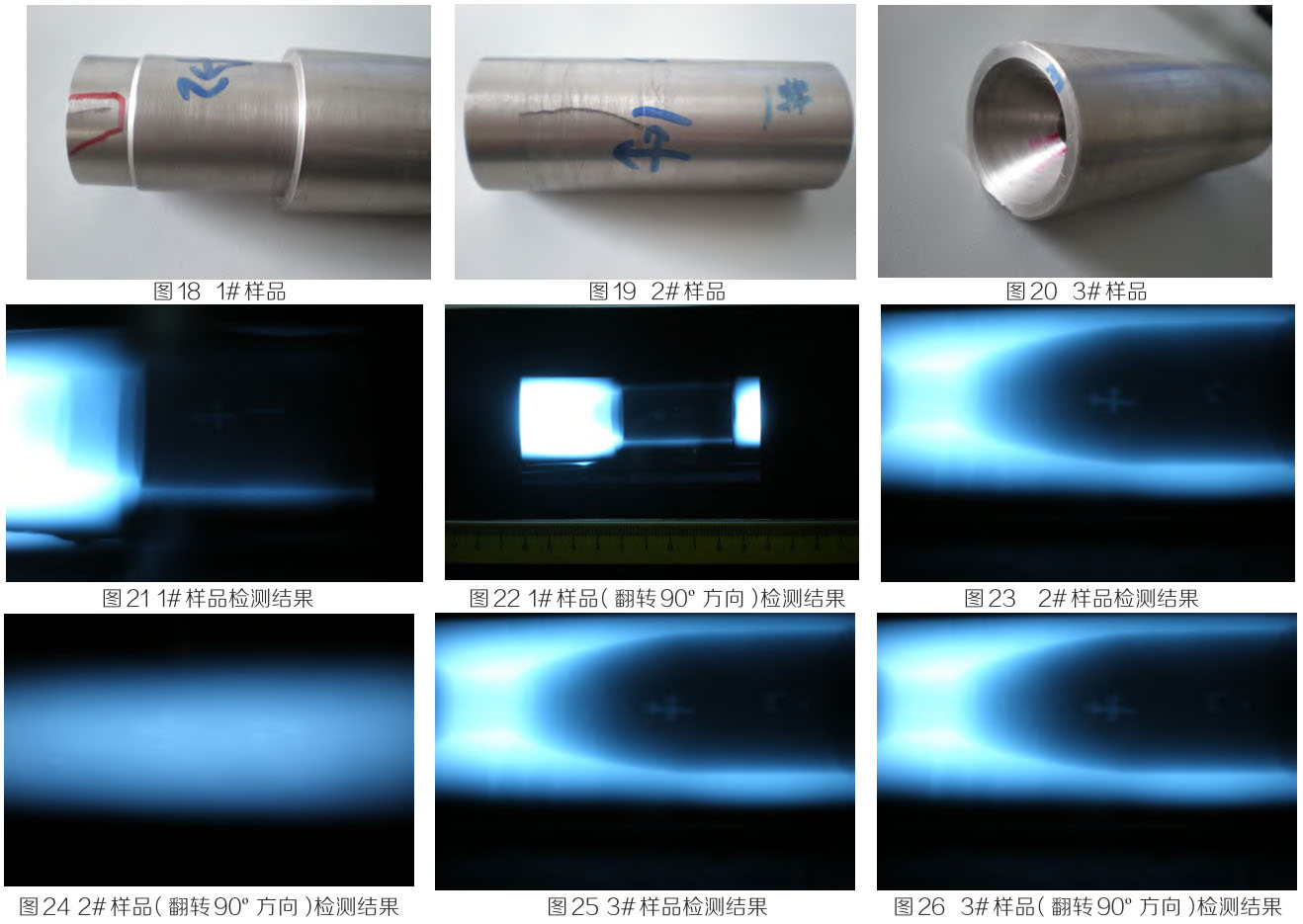
4、 缺陷特征及原因分析
4.1 缺陷特征
通過(guò)對(duì)缺陷部位進(jìn)行多方位的觀察,我們發(fā)現(xiàn)該缺陷具有如下特征 :
第一類(lèi)缺陷裂紋從棒材表面向內(nèi)部逐漸延伸,裂紋長(zhǎng)度及深度不等,與棒材整體存在一定的角度,大部分約為 45度,并且在分布上沒(méi)有規(guī)律可循,具有典型的鍛造折疊裂紋特征。
第二類(lèi)缺陷為機(jī)加后發(fā)現(xiàn)的內(nèi)表面裂紋,該缺陷大部分處于棒材的中心部位,并且均在棒材的一端。
第三類(lèi)缺陷為機(jī)加后發(fā)現(xiàn)的外表面較淺的小缺陷,由于此時(shí)棒材已進(jìn)行了部分機(jī)加工,外徑變小,缺陷已部分切除掉,但通過(guò)對(duì)殘留部分進(jìn)行觀察,可以判定同屬于第一類(lèi)缺陷。其在分布上是隨機(jī)的。
通過(guò)對(duì)上述樣品存在三類(lèi)缺陷部位進(jìn)行觀察,缺陷部位沒(méi)有存在異類(lèi)金屬和非金屬所形成的夾雜和偏析,不存在冶金缺陷問(wèn)題。
4.2 缺陷產(chǎn)生原因分析
該批產(chǎn)品經(jīng)過(guò)熔煉——擠壓—鍛造——機(jī)加——檢查——入庫(kù)這些工序后交付用戶。產(chǎn)品在后期生產(chǎn)過(guò)程中需要不斷進(jìn)行修磨、加熱、鍛造及切頭等工序,并最終進(jìn)行表面加工至合同所要求的尺寸公差范圍內(nèi)。在這里修磨及鍛造是非常重要的,若坯料表面修磨不徹底,或由于局部修磨較深,則鍛造后將產(chǎn)生裂紋將或坯料折疊,最終導(dǎo)致成品外表面存在裂紋和折疊 ;壓下量增大有利于提高產(chǎn)品的鍛透性,改善金屬的內(nèi)部組織,但如果過(guò)大,繼續(xù)鍛造時(shí)就會(huì)形成折疊 ;同樣對(duì)送進(jìn)量的控制也是非常重要的,若送進(jìn)量過(guò)小或鍛造過(guò)程中送進(jìn)量控制不理想 , 也容易產(chǎn)生橫向折疊,即我們所說(shuō)的鍛造折疊。并且變形量?jī)H集中在表面,使內(nèi)外組織不均。就會(huì)形成前面的說(shuō)的第一類(lèi)缺陷。
另外,在鍛造過(guò)程中,由于其變形特點(diǎn),使棒坯的心部和表層金屬流動(dòng)性有很大的差異,在棒材的頭部均會(huì)產(chǎn)生不同程度的縮尾,通常對(duì)該縮尾采用鋸切的方法去除,隨后通過(guò)目視檢驗(yàn)確認(rèn),因縮尾僅位于棒材頭部區(qū)域,通常的方法是可以完全去除的,但由于該類(lèi)產(chǎn)品在機(jī)加工中較粘,棒材表面和兩端在進(jìn)行車(chē)(磨)光及切頭后機(jī)加后金屬屑非常容易將缺陷掩蓋,與機(jī)加工后的痕跡混淆在一起,如果個(gè)別非常小的裂紋,檢查員目視不易發(fā)現(xiàn)很容易引起漏檢,棒材在加工過(guò)程中形成的縮尾如果未徹底切除干凈就會(huì)形成前面的說(shuō)的第二類(lèi)缺陷。
5、 結(jié)論
上述缺陷的產(chǎn)生原因是由于在鍛造過(guò)程未將鍛造折疊和上一道鍛造折疊因未修磨干凈所產(chǎn)生的裂紋以及鍛造縮尾未清除干凈而保留了下來(lái)形成的。
通過(guò)上面的檢測(cè)情況可以看出,超聲波檢測(cè)是可以發(fā)現(xiàn)的,因此通過(guò)進(jìn)一步的工作,對(duì)該類(lèi)產(chǎn)品的這種缺陷具有可檢性和可控性 ;而 X 射線檢測(cè)則無(wú)法有效發(fā)現(xiàn)此類(lèi)問(wèn)題。
制定合理的生產(chǎn)工藝,加強(qiáng)對(duì)鍛造過(guò)程中壓下量及送進(jìn)量控制,最大程度避免上述缺陷的產(chǎn)生。
加強(qiáng)對(duì)機(jī)加工后產(chǎn)品檢查力度,不漏檢和誤判,確保產(chǎn)品符合使用要求。
參考文獻(xiàn):
[1]李青云等 . 稀有金屬材料加工手冊(cè) [M]. 北京 :冶金工業(yè)出版社,1984.25-28.
[2]史亦偉等 . 超聲檢測(cè) [M]. 北京 :機(jī)械工業(yè)出版社 ,2012.22-25.
[3]鄭世才等 . 射線檢測(cè) [M]. 北京 :機(jī)械工業(yè)出版社 ,2011.40-42
無(wú)相關(guān)信息