引言
與普通的金屬材料相比,鈦具有非常多的優(yōu)點:在力學性能方面,鈦不僅具有較高的比強度,還具有優(yōu)異的韌性和抗疲勞性;在化學性能方面,鈦在自然條件下就可以形成致
密的氧化膜,該氧化膜能抵抗外界多種化學介質(zhì)的腐蝕,具有優(yōu)異的耐腐蝕性能;更值得一提的是,鈦合金在550℃高溫下長期使用,仍能保持較好的持久強度和熱穩(wěn)定性,且當
氧、氫、氮等含量較低時,在超低溫度條件下仍具有良好的延性和韌性。目前,鈦及鈦合金的應用主要分為航空航海和一般工業(yè)等傳統(tǒng)的應用以及汽車、計算機、體育用品等新的應用領域。
鈦及鈦合金的化學性能比較活潑,在高溫狀態(tài)極易氧化,對熱加工(如鑄造、鍛造及焊接等)不利。除此之外,鈦及鈦合金的切削加工也較難,主要是鈦在切削加工時容易粘刀,嚴重影響到鈦及鈦合金的表面質(zhì)量。因此,鈦及鈦合金的加工與普通金屬的加工有較大差異,對于鈦及鈦合金的加工,在方法上有其特殊的要求。目前,隨著加工技術的不斷革新,可用于加工鈦及鈦合金的方法也越來越多。
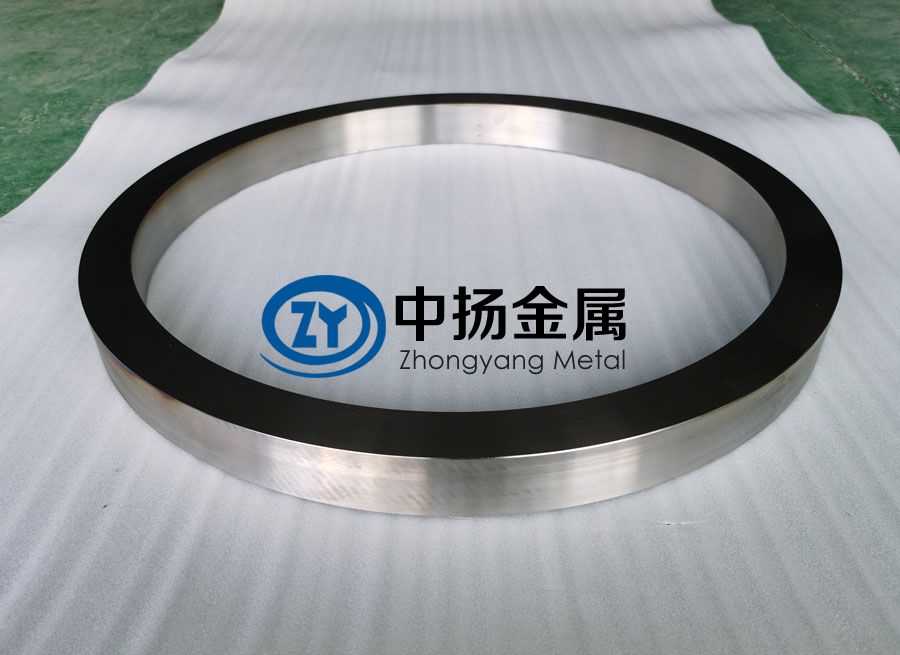
本文針對鈦的不同加工方法進行了探討,從傳統(tǒng)的鑄造、鍛造及焊接到新近發(fā)展起來的新型粉末冶金方法,尤其突出地分析了各種加工方法的優(yōu)點和不足之處,為不同領域所使用的鈦合金成型提供了切實可行的方法,有利于鈦及鈦合金的進一步推廣應用。
1、鈦及鈦合金鑄造成型及應用
1.1 鈦及鈦合金鑄造性能
作為近凈成型技術之一,鑄造技術可以一次性成型形狀復雜的產(chǎn)品,且能提高材料利用率并降低成本。然而,鈦及鈦合金化學性能非?;顫?,在高溫下極易被氧化,因此,對鈦
合金進行鑄造需要采用特種熔煉技術和設備,以防被污染。同時,與其他金屬相比,鈦及鈦合金的鑄造性能與充填補縮能力較差。影響鈦及鈦合金鑄件品質(zhì)的因素頗多,其中主要
影響鑄造性能(關于鈦及鈦合金的鑄造性能主要包括流動性、充填性、澆注和凝固過程形成氣體缺陷的傾向等)而這些影響因素又與合金的成分和性能、鑄型材料的種類以及熔煉、澆注條件相關。
1.2 鈦及鈦合金熔煉方法
鈦工業(yè)生產(chǎn)初期,采用非自耗真空電弧爐熔煉法對鈦及鈦合金進行熔煉,隨著各種技術的發(fā)展,出現(xiàn)了不同熔煉鈦及鈦合金的新工藝,主要有以下3種:(1)非自耗真空電弧爐熔煉法(簡稱NC法)。鈦工業(yè)起步階段,采用非自耗真空電弧爐熔煉的電極主要是石墨電極或鎢一釷合金電極,目前主要采用水冷銅電極進行熔煉,解決了工業(yè)污染問題,從而使非自耗真空電弧爐熔煉法成為鈦及鈦合金熔煉的重要方法之一。(2)真空自耗電弧爐熔煉法(簡稱VAR法)。目前,作為工業(yè)中生產(chǎn)鈦及鈦合金鑄錠的主要方法,真空自耗電弧爐熔煉法有其自身特點,即熔化速度高、能耗低以及鑄錠質(zhì)量優(yōu)異的穩(wěn)定性。該法的主要工作就是電極的制備。常見的方法有單塊電極壓制并焊成自耗電極法、采用按份加料連續(xù)壓制的整體電極以及利用其他熔煉方法制備電極等。(3)冷床爐熔煉法(簡稱CHM 法)。冷床爐熔煉法包括電子束冷床爐熔煉法(EBCHM)及等離子冷床爐熔煉法(PCHM)。電子束熔煉爐的工作原理是利用電子槍對水平傳送過來的原料進行加熱熔化,然后處于熔融狀態(tài)的鈦合金流向中部的精煉爐體,經(jīng)過一定時間精煉,最后注入水冷銅坩堝凝固成鑄錠。
此外,電子束冷床爐可采用未壓制的殘料、回收料等作為原料,以提高生產(chǎn)效率,同時避免在熔煉過程中由外界引入雜質(zhì)。
1.3 造型材料
由于造型材料是決定鈦及鈦合金鑄件質(zhì)量的關鍵,因此合理選擇造型材料具有舉足輕重的意義。目前,用于鈦及鈦合金鑄造的模型主要有石墨型、砂型和陶瓷型。
石墨型具有良好的高溫穩(wěn)定性,能抵抗液體鈦及鈦合金的剝蝕,石墨型的制備是生產(chǎn)民用鈦鑄件的主要造型工藝,按工藝不同可分為機加工石墨型和石墨搗實型。應當注意的是,生產(chǎn)質(zhì)量要求嚴格的航空鑄件,其機加工型和搗實型在澆鑄前均需進行真空除氣處理。沈陽鑄造研究所蘇貴橋等 采用紅外方法對機加工石墨鑄型進行了預熱處理,設計出合理的紅外線預熱裝置,得出預熱石墨鑄型的最佳溫度為350~400℃ ,能夠滿足相機鏡座、誘導鈦合金輪薄壁鑄件的試驗、生產(chǎn)要求,消除表面冷隔、皺褶以及澆不足等缺陷,提高了鑄件質(zhì)量。洛陽船舶材料研究所的范善君等利用石墨型鑄造制備了鈦合金導輪,與精密鑄造方式相比,該方法制備的導輪精度高、質(zhì)量穩(wěn)定,且不存在蠟模組合時產(chǎn)生的誤差對葉片的分布、尺寸等的影響。此外,根據(jù)鑄型材料性能特點,分型面選擇等可不受常規(guī)準則的限制,靈活地設計出更為符合特形鑄件的鑄型結構形式。鑄型工藝設計對擴大石墨型鑄造的使用范圍,提高鑄件質(zhì)量,簡化鑄型加工工藝以及降低原材料消耗等都有著較大的潛力。
石墨型雖然有很多優(yōu)點,但是也存在一些問題(如費用高、生產(chǎn)石墨能耗高),不利于鈦及鈦合金鑄造的廣泛推廣,為了開發(fā)石墨鑄型的代用品,美國礦山局曾對鋯砂一水玻璃鑄型進行了研究。鋯砂鑄型曾用于有色金屬的鑄造,在普通砂中它的耐火度最高,而水玻璃成本低,生產(chǎn)出的鑄型和泥芯干強度高。我國徐發(fā)等研究了以氧化鋯為涂料的水玻璃鋯砂鑄型,結果表明,其具有良好的高溫性能,能替代石墨粉搗實鑄型,并且成本比石墨粉搗實鑄型低50 ~60 ,造型及鑄型處理周期大大縮短,鑄型發(fā)氣量也比石墨型低得多,通過該工藝能澆鑄出16.5 kg的鈦泵體鑄件,表面污染層僅0.09mm。
陶瓷模殼的性能及制備技術決定了鈦合金精密鑄件的質(zhì)量,其制作與傳統(tǒng)模殼類似。賈清等研究了不同粉料所配制的料漿對模殼表面質(zhì)量與強度的影響,討論了鈦合金精鑄用陶瓷模殼的制備工藝,指出粉料的粒度分布對模殼的表面質(zhì)量有極大影響,需要嚴格控制所用粉料的粒徑。當粉料粒度分布過于集中時,應采取相應措施分散粉料,提高模殼的表面質(zhì)量,進而提高鈦及鈦合金鑄件的表面質(zhì)量。此外,模殼的強度主要依賴于所用粘接劑的性質(zhì),由于粘接劑在高溫下的性能變化直接影響模殼的性能,因此,在生產(chǎn)過程中必須根據(jù)粘接劑的熱分析曲線來確定模殼焙燒溫度 。
1.4 鈦及鈦合金鑄造注意事項
鈦鑄造技術的關鍵主要有兩方面:一是具有性價比高的熔煉爐,二是不與液鈦起反應的性能穩(wěn)定的鑄型。隨著鑄造設備及鑄造技術的發(fā)展,鑄造成型的鈦及鈦合金產(chǎn)品顯示出穩(wěn)步增長的勢頭。然而,在今后的推廣應用中還有以下幾方面的問題需要解決:(1)開發(fā)新的熔煉及鑄造方法,大幅度降低鈦及鈦合金鑄件的生產(chǎn)成本;(2)開發(fā)出鈦及鈦合金廢料回收重熔的新技術,確保在降低成本的同時提高產(chǎn)品的質(zhì)量;(3)陶瓷型及精密鑄件大型化的研發(fā);(4)無損探傷檢測標準的修訂。
2、鈦及鈦合金鍛造成型及應用
2.1 鍛造工藝
鈦及鈦合金冷變形困難,因此,通常需要經(jīng)過熱加工方法變形成各種坯料和鍛件,其中,鈦合金的鍛造加工是一種應用較普遍的方法。這是因為鍛造不僅可以達到尺寸及形狀與產(chǎn)品接近,還能改善鈦合金組織,從而提高其性能。
在鈦合金的熱加工中,加熱溫度極為重要,溫度過低,鈦合金的變形抗力大,且容易產(chǎn)生裂紋等缺陷,溫度過高,組織容易粗化,因此,鈦及鈦合金的鍛造溫度范圍較窄。鈦合金錠的開鍛模通常是在高于 相變溫度下進行的,因為鈦的 相屬于體心立方,而體心立方結構具有較高的塑性,所以對鍛造壓力的要求一般也較低。但終鍛一般在低于β相變溫度下進行,這樣可以防止β晶粒的長大和隨之而來的塑性降低。應變速率的變化對α和α+β鈦合金可鍛性能的影響不大,因此,鈦合金的鍛造按其β轉(zhuǎn)變溫度可分為α+β 鍛造和p鍛造,近年來又出現(xiàn)了近β鍛造、等溫鍛造等新工藝。
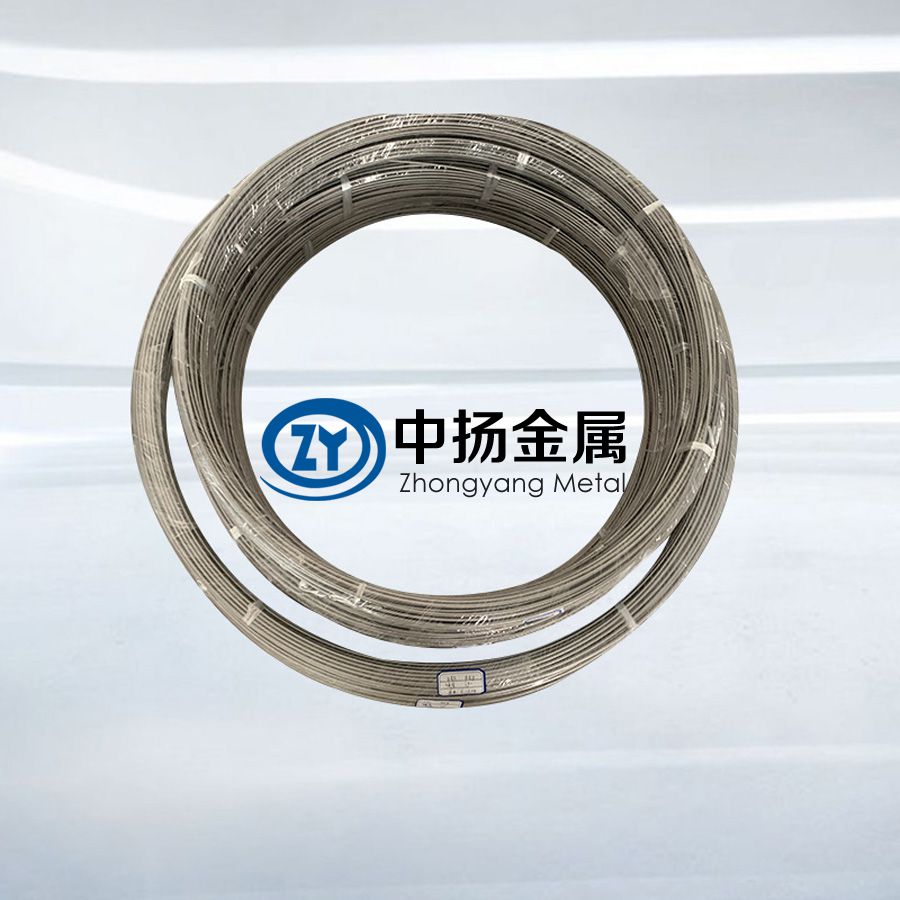
鈦合金的高溫鍛造也稱“β鍛造”,分為兩種,第一種是坯料在β區(qū)加熱,在β區(qū)開始并完成鍛造的工藝方法;第二種是坯料在β區(qū)加熱,在 區(qū)開始鍛造,并控制很大變形量在兩相
區(qū)完成鍛造的工藝方法 。β鍛造的鍛件常存在熱穩(wěn)定性和塑性差等缺點,會導致β脆性出現(xiàn),但通過采取適當?shù)臒徨懞鬅崽幚砑翱刂坪缅懞罄鋮s速度等可以制備出具有良好綜合力學性能的鈦合金鍛件。
α+β兩相合金、 合金在β轉(zhuǎn)變溫度下以中等應變速率鍛造的工藝常被稱為α+β兩相鍛造或常規(guī)鍛造。典型的常規(guī)鍛造組織具有室溫塑性好、強度高等優(yōu)點,然而其斷裂強度、高溫性能及斷裂韌性等較差,且模具對鍛件的冷卻容易在鍛件表面產(chǎn)生裂紋,鍛造后需要進一步加工且加工余量大,材料利用率低,因此,常規(guī)鍛造鈦合金難度較大。但學者們通過研究發(fā)現(xiàn),只要能合理控制鍛造溫度、變形量和處理制度等,就能獲得質(zhì)量較好的鍛件。
近β鍛造工藝是將鈦合金坯料在相變點以下10~15℃加熱鍛造,鍛后水冷,然后進行高溫韌化再低溫強化處理 。
由于近β鍛造溫度控制極為嚴格,因此如何控制加熱鍛造溫度就成了最大的技術難點。同時,加熱鍛造溫度還會受到加熱爐爐溫的不均勻性和鍛造過程中產(chǎn)生的熱效應等因素影響。采用近β鍛造工藝對TC11、TC17及TA15鈦合金進行鍛造,結果表明能獲得較好的綜合性能,如TC11近β鍛造試樣520℃ 的高溫強度與常規(guī)鍛造和IMI685合金β鍛造500
℃的性能相當,塑性和熱穩(wěn)定性與常規(guī)鍛造相當,其疲勞蠕變交互作用壽命長于常規(guī)鍛造 。
等溫鍛造是指自始至終模具與工件保持相同的溫度,以低應變速率進行變形的一種鍛造方法。與常規(guī)鍛造相比,等溫鍛造主要有以下優(yōu)點:可以鍛造出尺寸可控、形狀復雜、精度高的鍛件,節(jié)省了原料,降低了成本;鍛造工序少,減少了鍛造作業(yè)量,提高了生產(chǎn)效率;鍛造溫度較高,使坯料易于充滿模具型腔,減少了對模具的磨損;鍛件質(zhì)量好,一般無殘余應力。利用等溫鍛造的諸多優(yōu)點,可使鈦合金的加工變得更加容易,目前大多用于制造航空航天工業(yè)中的飛機零部件,如寶鋼集團的周建華等將等溫鍛造技術用于TC4鈦合金
翼芯、氣瓶等精密優(yōu)質(zhì)鍛件的生產(chǎn)(如圖1所示)。采用等溫鍛造工藝,利用鈦合金超塑性的變形能力,其變形參數(shù)易精確控制,并克服了傳統(tǒng)鍛造中由死區(qū)引起的組織不均勻,可生產(chǎn)出表面質(zhì)量良好、尺寸精確和性能穩(wěn)定的航天用鈦合金精鍛件。與普通鍛造相比,等溫鍛件的材料用量可減少30%~60%,且縮短了加工工時,降低了零件成本,同時,等溫鍛件的組織更均勻、細小,質(zhì)量更穩(wěn)定。
然而,等溫鍛造也有一些缺點:需要溫度可控的加熱系統(tǒng);需要耐高溫的模具;需要高溫下使用的潤滑劑以及額外的防止工件和模具氧化的保護裝置。
2.2 鍛造過程中應注意的問題
在鈦及鈦合金鍛造過程中,應注意以下幾方面的問題:
(1)對合金成分的敏感性。個別鈦合金的鍛造性能和力學性能并不太受合金元素變化的影響,卻受間隙元素(如氧、碳和氮)變化的影響。例如鈦合金的氧含量由0.1 提高到0.2 ,將使TC4的β轉(zhuǎn)變溫度升高40℃ ,強度提高15% 。
(2)污染和缺陷的排除。在空氣中對鈦進行加熱而產(chǎn)生的硬的、富α的皮下層難以用機械加工方法除掉,根據(jù)加熱時間不同,該層的厚度一般介于0.13~0.64 mm,在氫氟酸中浸
蝕鍛件,以0.025mm/min蝕除表層。但污染較嚴重時,還需要除去厚磷皮,要求進行兩次處理,即先在鹽槽中完成除磷皮工作,然后再完成上述酸蝕過程。(3)設備的清理。在
鍛造時必須小心,以免鈦與鋼磷皮接觸,否則會發(fā)生“熱劑”類型的反應,使鍛模毀壞。鈦會使氧化鐵在高壓高溫條件下所爆發(fā)的放熱反應中得到還原。因為爐膛和鍛造設備可能
是鋼磷皮的來源,所以在用來加熱鈦之前,應進行徹底的清理。(4)潤滑。鈦毛坯在加熱時形成的磷皮有很大摩擦作用,引起模具很快磨損,因此有必要使用潤滑劑。模鍛鋼和其他有色金屬所用的潤滑劑不能滿足上述全部要求。石墨與水玻璃和滑油混合的膏狀潤滑劑會使鈦合金表面產(chǎn)生裂紋,其原因是表面上存在脆性的 層,在變形時被破壞,這些裂紋是應力集中源,繼續(xù)變形時可能向金屬內(nèi)部擴展。對于鈦合金來說,玻璃潤滑劑是目前所研制的潤滑劑中最好的。
在模鍛和局部擠壓變形條件下,如玻璃涂料的成分選擇得當,則能保持液態(tài)摩擦。
3、鈦及鈦合金焊接成型及應用
大多數(shù)鈦合金可以使用氧乙炔焊的方法進行焊接,并且所有的鈦合金均可以使用固態(tài)焊接方法進行焊接(如等離子弧焊、激光和電子束焊接),事實上,鈦合金焊接接頭產(chǎn)生裂紋的傾向性要比黑色金屬(如鐵合金、鎳合金)小得多。盡管鈦合金具有如此良好的性質(zhì)和其他一些優(yōu)異的焊接特性,但人們還是認為鈦合金的焊接是相當困難的,主要在于鈦合金焊接對于氣體保護的要求特別高。由于在焊接過程中引入的N 、O 和含碳物質(zhì)使得鈦合金的熔化焊接頭變脆,因此待焊區(qū)一定要清理干凈并使用惰性氣體保護。含有氧、氮、氫等雜質(zhì)元素的純鈦的塑性和韌性急劇下降。而氣孔的存在更會大大降低接頭的強度,為了改善接頭強度性能,必須減少焊接接頭中的氣孔。常用的減少鈦合金焊接接頭中氣孔的措施主要有以下幾個方面心 :(1)使用高純氬氣或氦氣進行保護;(2)鈦合金部件和焊料要保持干燥;(3)待焊鈦合金部件的部位與焊料進行徹底清洗,保持清潔。
鈦及鈦合金的焊接工藝主要有鎢極氬弧焊、真空電子束焊及激光焊。
鎢極氬弧焊時常被稱為TIG焊,是一種在非消耗性電極和工作物之間產(chǎn)生熱量的電弧焊接方式;電極棒、溶池、電弧和工作物臨近受熱區(qū)域都是由氣體狀態(tài)的保護隔絕大氣混入,對于薄壁件的焊接采用常規(guī)焊接方法易出現(xiàn)焊穿、變形大以及焊接性能不穩(wěn)定等現(xiàn)象。實踐表明,對薄壁鈦板采用脈沖氬弧焊可避免出現(xiàn)上述現(xiàn)象。王玉文等采用鎢極氬弧焊對某型號衛(wèi)星用鈦合金高壓氣瓶進行了焊接,通過對焊接工藝及參數(shù)的控制,摸索出了一套衛(wèi)星用鈦合金高壓氣瓶焊接方法,提高了焊縫質(zhì)量和焊接一致性,該方法同樣也可用于導彈用鈦合金的焊接。
真空電子束焊是利用定向高速運動的電子束流撞擊工件使動能轉(zhuǎn)化為熱能而使工件熔化,形成焊縫。作為組成物質(zhì)的基本粒子,電子是一個傳導能量的極好介質(zhì),當電子受到阻擋減速后,電子以熱能的方式精確地在作用點釋放能量,而周圍的材料依然保持原來的冷狀態(tài)。由于真空電子束焊具有深度熔化的效應,所以能夠加工出非常窄非常深的焊縫。電子束很容易進行偏轉(zhuǎn),因此能夠?qū)ζ溥M行精確的控制。真空電子束焊的缺點是焊縫中易出現(xiàn)氣孔,結構尺寸易受真空室限制,不適合于大批量生產(chǎn)。電子束焊接時,焊接接頭中產(chǎn)生相當大的殘余應力,且隨焊件厚度的增加而增大。目前主要采用完全真空退火來消除焊接后的殘余應力。
電子束焊接已廣泛用于汽車、航空航天、核工業(yè)等行業(yè),現(xiàn)已發(fā)展到石油、化工、機械、儀表儀器、精密加工等行業(yè)。尤其在航空工業(yè)中許多零件都需要焊接,如空氣導管是某渦
扇發(fā)動機上典型的薄壁筒形零件,要求電子束焊后保持極高的精度,如何保證焊后達到技術要求的尺寸精度是主要攻關目標。曲伸等針對TC4這類材料,采用工藝襯套和合適的家
具保證了電子束焊接薄壁空氣導管的精度要求。經(jīng)過試車運轉(zhuǎn)考驗,證明電子束焊可完全滿足設計要求。激光技術采用偏光鏡反射激光產(chǎn)生的光束使其集中在聚焦裝置中產(chǎn)生能量巨大的光束,如果焦點靠近工件,工件就會在幾毫秒內(nèi)熔化和蒸發(fā),這一效應可用于焊接工藝。由于激光焊接具有能量集中、焊接成型好、操作簡單、易于檢測等優(yōu)勢,非常適合焊接各種鈦合金材料,在飛機鈦合金零部件的焊接中必將成為主導方向。代永朝等對厚度為2mm的TC4合金板材進行了激光焊接。焊縫的宏觀形貌如圖2所示,可以看到焊縫完全焊透,消除了自熔焊時焊縫的凹陷和咬邊 。經(jīng)研究發(fā)現(xiàn),焊接接頭強度可達母材強度的99.5%,滿足飛機鈦合金結構損傷的修復要求。趙穎等對鈦合金蒙皮骨架結構進行了激光焊接,研究了不同激光焊接工藝對其焊縫成型的影響,觀察了焊縫的微觀組織形貌。結果表明:焊縫熔深、熔寬隨著激光功率的升高和焊接速度的降低而逐漸增加;骨架的寬度、厚度以及蒙皮與骨架間的間隙量對熔深、熔寬的影響不大,間隙量增大使焊縫表面咬邊、凹陷明顯,蒙皮上焊縫的顯微硬度值略高于骨架上焊縫硬度值。然而,激光焊接也有一些缺點:焊件位置需非常精確,務必在激光束的聚焦范圍內(nèi);焊件需使用夾治具時,必須確保焊件的最終位置與激光束將沖擊的焊點對準;設備昂貴等。
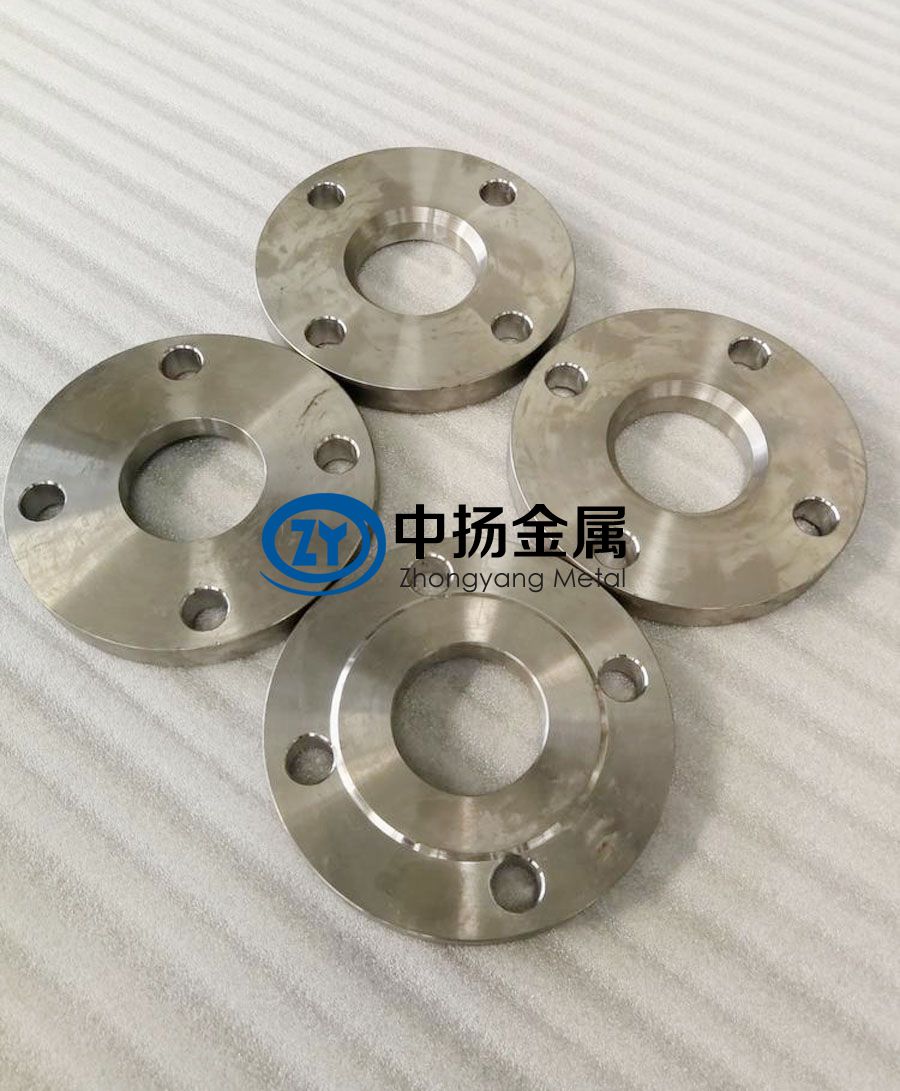
對于鈦及鈦合金而言,除上述幾種焊接方法外,還有諸如等離子弧焊、電子束焊及擴散焊等方法,在焊接過程中,應注意各自優(yōu)點,選取合適的方法,盡可能地避免在焊接過程
中出現(xiàn)缺陷??傊?,鈦及鈦合金焊接之前,一定要進行認真的清理,因為污物易在焊縫中產(chǎn)生氣孔和非金屬夾雜,使焊縫的塑性和耐腐蝕性顯著下降。常用的清理方法有切削加
工或噴丸處理等機械清理方法和酸洗再進行清洗等化學清理方法。
4、鈦及鈦合金粉末冶金及應用
鈦及鈦合金加工企業(yè)主要關注的是降低加工成本,希望通過技術創(chuàng)新解決生產(chǎn)經(jīng)營難題。在眾多的制備方法中,粉末冶金作為一種低成本加工方法在鈦及鈦合金領域應用極為廣泛??紤]到鈦液本身易發(fā)生化學反應的特點,鈦合金必須在惰性氣體保護下或高真空環(huán)境中進行加工,這將使得傳統(tǒng)的鍛造工藝成本很高。而采用粉末冶金技術制造鈦合金產(chǎn)品,能夠提高材料使用效率并且降低加工成本,該項技術已成為研發(fā)低成本鈦合金工藝的重要研究方向。日本TKK公司以鈦粉和混合中間合金粉為原料,通過混料、壓坯并燒結,成功制備了鈦合金產(chǎn)品。國內(nèi)利用粉末冶金對鈦合金進行加工也做了不少工作,如湖南大學胡紫英等采用粉末冶金法成功制備出力學性能與骨匹配的開孔型多孔鈦,其孔隙率分布在8.6 ~34.5 之間,平均孔徑隨孔隙率的增加而降低;通過應力一應變曲線分析得到其彈性模量在7.2~9.9GPa之間,接近人骨彈性模量,此多孔鈦有望成為理想的人工骨修復材料。除上述傳統(tǒng)的粉末冶金燒結外,最近還出現(xiàn)了不少新型的粉末冶金技術,主要包括如下幾種方法。
4.1 新型高能量源直接燒結鈦粉末的冶金加工技術
隨著科技進步,利用高能量源直接燒結鈦粉末的冶金加工也逐步成熟并走向應用,該技術的特點是基于“分層制造”成形的思想,制造成型的零件尺寸及形狀幾乎可以達到最終
要求,很適合形狀復雜的鈦及鈦合金零件的加工,其主要包括電子束選區(qū)熔覆技術、直接金屬激光燒結快速成型技術等。
電子束選區(qū)熔覆技術是采用高能量的電子束轟擊預先混合均勻的鈦混合粉料并逐層燒結的制造技術。鈦金屬粉末在電子束的轟擊下會熔化燒結成一層并與下層已降溫成型的一層粘接。鈦金屬粉末在電子束的轟擊下被逐層燒結堆積,直至整個零件的最上面一層燒結完成,而未燒結區(qū)域的粉末形態(tài)沒有變化,掃除后便可得到所需的三維鈦合金零件。楊鑫等研究了ELI TA7金屬粉末電子束選區(qū)熔化快速成型件的顯微組織和力學性能。研究結果表明,在一定條件下,Z字型掃描路線可以有效提高燒結件的致密度、室溫強度和延伸率。燒結件的相對密度可達97 ,抗拉強度為740MPa,延伸率為8 ,接近鍛件的性能 。經(jīng)分析可知,致密度高的原因是電子束高的能量利用率在燒結過程中產(chǎn)生瞬時液相,同時真空下粉末的表面得到凈化,提高了燒結活性;而過快的冷凝過程有助于產(chǎn)生細小的晶粒,同時致密度的提高以及晶粒的細化均有助于燒結件力學性能的提高。
直接金屬激光燒結快速成型技術綜合運用先進的激光技術、粉體技術和計算機控制技術實現(xiàn)直接加工成型近致密金屬零件。德國EOS公司新開發(fā)的激光選區(qū)熔化設備EOSIN TM 280采用束源質(zhì)量高的Yb光纖激光器, 將激光束光斑直徑聚焦到100um,大幅提高激光掃描的速度,縮短成型時間,其成型零件性能與鍛件相當,典型應用如圖3所示
4.2 金屬粉末注射成型技術(MIM)
金屬粉末注射成型技術(MIM) 是目前發(fā)展較快的近凈成型粉末冶金技術,可制造高精度的復雜鈦合金零件,被認為是目前最具優(yōu)勢的鈦合金成型技術之一。
粉末注射成型(Powder injection molding, PIM) 是將塑料注射成型引人粉末冶金行業(yè)而形成的一項新型粉末冶金成型技術。該項技術自問世以來就得到廣泛關注,1992年日
本鎢業(yè)公司通過該技術制造出首件鈦合金運動夾板,隨著技術的日益成熟, 鈦的MIM產(chǎn)品在醫(yī)療器械、牙科植人體、汽車領域、高爾夫球頭和表帶等方面有廣泛應用。李挺等以
氯化鈉作為造孔劑,利用金屬注射成型工藝制備多孔鈦,研究燒結溫度、造孔劑粒度和含量對多孔鈦孔隙度、微觀形貌和力學性能的影響,結果表明,隨著燒結溫度的升高,多孔鈦的孔隙度逐漸下降而抗壓強度和彈性模量逐漸升高;并討論了MIM多孔鈦植人體的最佳燒結溫度為1100~1200℃,NaCl的最優(yōu)粒度為150~250um。
目前注射成型工藝已成功用于制造純鈦粉、TiA1、TC4、Ti-Mo-Al和其他一些鈦基粉末。
4.3溫壓成型技術
溫壓技術是近幾年新發(fā)展起來的一次壓制、一次燒結工藝,制造高密度、高性能粉末冶金結構零件的一項可行的新技術。它是在混合物中添加高溫新型潤滑劑,然后將粉末和模具加熱至150℃左右進行剛性模壓制,最后采用傳統(tǒng)的燒結工藝進行燒結的技術。與普通的粉末冶金相比,該技術的主要特點就是能夠提高燒結零件的致密度。何世文等研究了鈦合金粉末的溫壓成型行為,發(fā)現(xiàn)在同一壓制力下,鈦合金粉末的生坯密度均在140°℃左右達到最大值,高于或低于這一溫度, 生坯密度反而降低。在壓制壓力為500MPa下,溫壓成型的脫模力比室溫成型的脫模力降低27.7%,同時改善了鈦合金的顯微組織。
4.4 熱等靜壓成型技術
熱等靜壓(Hot isostatic pressing, HIP) 工藝是將制品放置到密閉的容器中,向制品施加各向同等的壓力,同時施以高溫,在高溫高壓的作用下,制品得以燒結和致密化。采用熱等靜壓制成的鈦合金零部件具有優(yōu)異的力學性能,且節(jié)約成本,幾乎可以實現(xiàn)零部件的近凈成型,同時制得的零件致密度高,幾乎可達到100%。
熱等靜壓是高性能材料生產(chǎn)和新材料開發(fā)不可或缺的手段。王亮等采用熱等靜壓預合金粉工藝對TC4粉末冶金技術進行了研究,同時就原料粉狀態(tài)對粉末鈦合金性能的影響進行了初步研究并進行了近凈成型工藝試驗。結果表明,采用預合金粉工藝制備的TC4粉末合金材料性能優(yōu)良,且可實現(xiàn)近凈成型 。HIP在制備鈦制品件方面也顯示出極好的應用前景,歐陽洪武等采用徑向熱壓工藝制備了高徑比為10.7、密度為3.79g/cm的TiAl基合金汽車發(fā)動機排氣門,為制備合格的TiAl基合金排氣門探索了一條新的途徑 。
除上述幾類鈦合金粉末冶金成型方法外,還有電火花燒結及輻射微波燒結等新型方法。
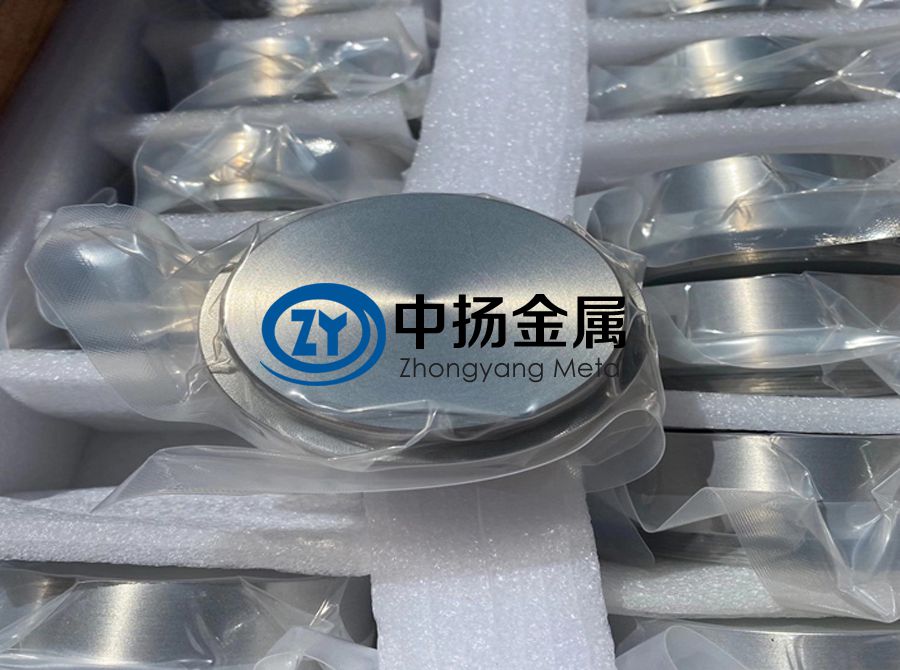
5、鈦及鈦合金機械加工及應用
眾所周知,鈦合金加工性較差,主要有以下幾個方面的原因:(1)粘刀現(xiàn)象嚴重。鈦合金材料的粘刀現(xiàn)象極為嚴重,易產(chǎn)生積屑瘤,引起工件尺寸變化,進而影響到產(chǎn)品裝配質(zhì)量,甚至會導致零件報廢。(2)化學活性大。鈦合金在600℃以上時,與氣體發(fā)生劇烈的化學反應。吸收氣體后鈦合金表面的硬度明顯上升,鈦與氧、氮產(chǎn)生間隙固溶體,對刀具有強烈的磨損作用。(3)鈦合金的彈性模量低,彈性變形大,接近后刀面處工件的回彈量大,因此已加工表面與后刀面的接觸面積大,摩擦非常嚴重。(4)鈦合金的熱導率低,為鐵的1/5,極大地限制了刀尖的冷卻條件,使刀具磨損加劇。
鑒于上述原因,在加工鈦合金時,首先要求切削速度低,因為切削速度對切削刃的溫度影響很大,切削速度越快,則切削刃溫度劇增,切削刃溫度直接影響刀具壽命,因此要求合適的切削速度;其次,切削深度要大,實踐表明,切削深度對刀刃溫度影響較小,所以采用低切削速度,大切削深度對鈦合金的加工是有利的;再次,采用適當?shù)睦鋮s液,鈦合金的加工過程中,使用冷卻液可以把刀刃的熱量帶走,沖走切屑,以降低切削力,因此合理地應用冷卻液是提高生產(chǎn)力和改善工件表面質(zhì)量的有力措施;此外,刀具材料的選擇也尤為重要,常用的切削鈦合金的刀具材料有YG6、YG8、Wll2CrMo等。
6、結語
目前,鈦及鈦合金的加工主要針對航空航天領域,而對于民用鈦品而言,還不具規(guī)模,主要原因是鈦制品的成本太高,難以像鋼材一樣大規(guī)模地運用。其中,在鈦及鈦合金制品中,加工成本又占很大比例。從上述介紹的不同加工方法來看,鈦及鈦合金存在的主要加工問題有:一是加工難度大。鈦合金性能決定了其熱加工需要保護性氣氛,以防氧化等,
加工中需要注意的事項較多,如鍛造溫度區(qū)間的控制、激光熔覆等加工的零件尺寸小等。二是加工的設備費用較高,如RP技術,普通企業(yè)無力承受其高額的設備費用,因此也就無
力進行大規(guī)模的鈦制品生產(chǎn)。
除此之外,限制鈦及鈦合金產(chǎn)品大量應用的另一個重要原因是人們對鈦合金制品在普通工業(yè)中應用的宣傳力度不夠。其實從長遠來看,鈦合金制品的成本比普通鋼材還低。隨著科技的不斷進步,鈦及鈦合金產(chǎn)品的制備技術會越來越簡單易行,加工成本也會越來越低,鈦及鈦合金制品必將在更廣泛的領域中彰顯出獨特的魅力。
相關鏈接