引言
國防和國民經(jīng)濟(jì)建設(shè)的巨大需求及結(jié)合第四次工業(yè)革命所帶來的技術(shù)爆炸推動著航空航天領(lǐng)域的復(fù)雜裝備向精密化、一體化、輕質(zhì)化和智能化發(fā)展,這給傳統(tǒng)的制造業(yè)帶來了極大的挑戰(zhàn)。當(dāng)前航空航天領(lǐng)域的主流制造技術(shù)仍為減材或等材制造,面對復(fù)雜的內(nèi)/外部結(jié)構(gòu)、超高的尺寸精度要求、快速試制和小批量定制等需求,該技術(shù)出現(xiàn)了明顯的瓶頸,使得人們將目光轉(zhuǎn)向增材制造領(lǐng)域。
目前,國內(nèi)研究較多的為高溫增材制造技術(shù),如激光熔融、電子束熔融、激光燒結(jié)和光固化等技術(shù)[1-4],難以支撐低溫材料加工、復(fù)雜內(nèi)部結(jié)構(gòu)加工以及功能性復(fù)合材料加工等應(yīng)用。
金屬超聲增材制造(Ultrasonicadditivemanufacturing)也被稱為超聲固結(jié)(Ul-trasonicconsolidation),具有低溫加工的特性,是一種極具潛力的制造技術(shù),自1999年被White等[5]提出后引起了國內(nèi)外學(xué)者的廣泛關(guān)注。
金屬超聲增材制造的基本原理是通過超聲波發(fā)生源產(chǎn)生高頻超聲電信號,再由換能器將電信號轉(zhuǎn)化成超聲波頻率的振動,從而將一系列金屬帶材連接形成結(jié)構(gòu)體。目前常用的帶材寬度為25mm。
為了獲得復(fù)雜的內(nèi)部結(jié)構(gòu)和最終的幾何外形,超聲增材過程中還需要穿插機(jī)械加工,如圖1所示。與超聲金屬焊接類似,增材階段通過換能器驅(qū)動超聲壓頭產(chǎn)生高頻摩擦運(yùn)動,振動頻率可達(dá)20kHz,通過加工過程中的超聲功率器實(shí)現(xiàn)振幅的精確控制。同時,壓頭會被施加一定的下壓力并在數(shù)控系統(tǒng)的控制下進(jìn)行滾動,以實(shí)現(xiàn)金屬帶材的連續(xù)固結(jié)。在必要的情況下,還會通過給基板預(yù)熱來為超聲焊接系統(tǒng)提供額外的能量。在減材階段,采用數(shù)控加對已固結(jié)部分進(jìn)行處理,引入復(fù)雜的內(nèi)部結(jié)構(gòu),并形成滿足精度要求的外形。
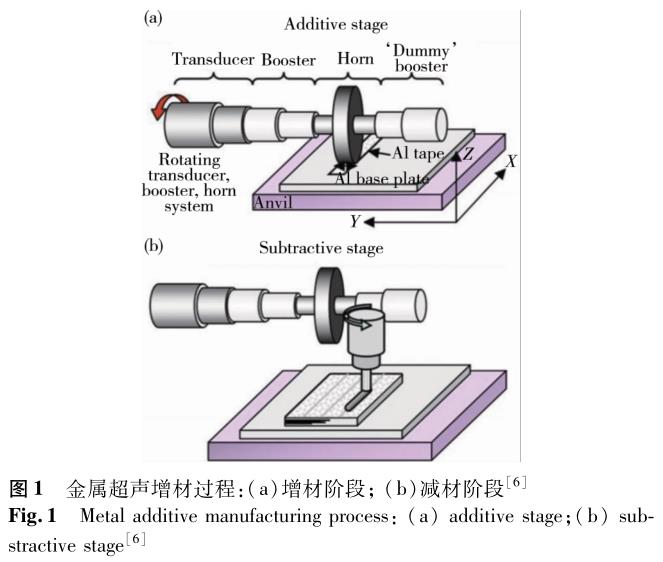
金屬超聲增材制造屬于固相冶金過程,其原理是在高頻摩擦振動和下壓力的作用下,層間界面處的金屬產(chǎn)生高應(yīng)變率的塑性變形,破壞金屬表面的氧化膜,使得金屬間發(fā)生直接接觸、原子擴(kuò)散直至形成冶金結(jié)合。Fujii等[7]詳細(xì)研究了界面形成的過程,如圖2所示,帶有紋理結(jié)構(gòu)的超聲壓頭與金屬箔片首先接觸,在超聲振動的作用下金屬發(fā)生塑性變形,在表面形成微小的凸起(如圖2a—c所示);引入新的金屬箔片后,凸起位置與上層金屬之間產(chǎn)生接觸并形成微小的粘結(jié)(如圖2d所示),伴隨壓頭的振動發(fā)生塑性流動,導(dǎo)致氧化膜破裂形成納米級別的氧化物簇,隨后在下壓力的作用下這些粘結(jié)體發(fā)生變形坍塌,使得界面間直接接觸的區(qū)域逐漸擴(kuò)展,通過原子擴(kuò)散最終形成厚度為10~20μm的冶金結(jié)合層[8]。此外,研究表明,由于塑性變形的影響,界面處還會發(fā)生再結(jié)晶(如圖2f所示)。
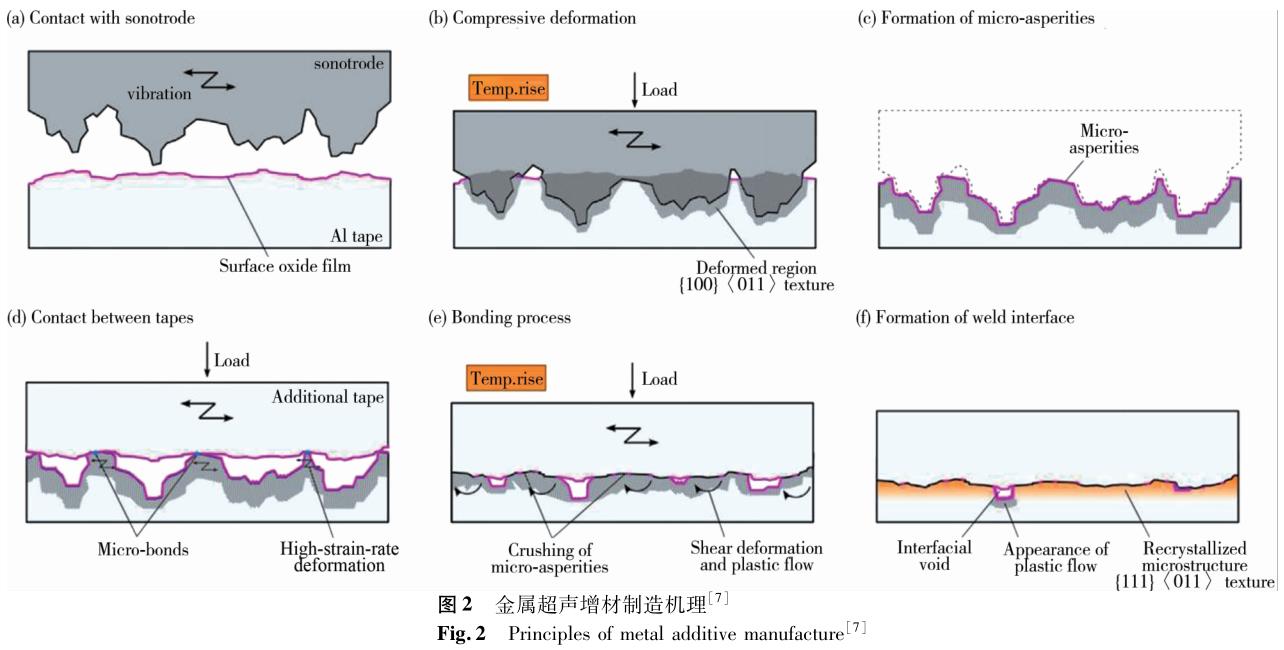
從以上研究可以看出,金屬超聲增材的核心是界面處的熱力耦合過程,即通過界面的溫升和塑性流動來影響結(jié)合質(zhì)量,塑性流動過小,界面結(jié)合強(qiáng)度將會偏低甚至無法結(jié)合,塑性流動過大,則容易導(dǎo)致材料發(fā)生破壞。因此,需要對振幅和下壓力等影響熱力耦合過程的關(guān)鍵工藝參數(shù)進(jìn)行合理的組合,以盡可能提高結(jié)合強(qiáng)度并防止材料發(fā)生破壞。值得注意的是,超聲增材過程中金屬不會熔化,由摩擦和塑性變形產(chǎn)生的溫升不超過材料熔點(diǎn)的1/2(如銅和鋁的溫度為150℃)[9-11],因此區(qū)別于大多數(shù)的高溫增材技術(shù),超聲增材制造過程中幾乎不會發(fā)生金屬氧化現(xiàn)象,不需要控制周圍的氣氛。
從第一臺超聲增材設(shè)備出現(xiàn)至今已經(jīng)20余年[5],經(jīng)過國內(nèi)外同行的不懈研究,超聲增材設(shè)備不斷完善,超聲增材技術(shù)所能加工的材料也逐漸增加,但是真正用于工程實(shí)際的超聲增材部件仍然受到限制。
對超聲增材加工的部件進(jìn)行拉伸試驗(yàn)和疲勞試驗(yàn)[12-16],結(jié)果表明,拉伸破壞形式主要是層間脆性斷裂,而疲勞失效也主要發(fā)生在界面,說明超聲增材部件的特性主要受層間結(jié)合性能的影響。
由于超聲增材系統(tǒng)過于復(fù)雜,加工中的過程控制參數(shù)也較多,不同材料、不同參數(shù)組合所形成的層間界面微結(jié)構(gòu)與粘結(jié)質(zhì)量也各不相同,導(dǎo)致加工出的部件性能有很大區(qū)別。為了充分理解增材制造的物理過程,從而更好地指導(dǎo)其實(shí)際加工過程,目前國內(nèi)外的研究主要集中在以下幾個方面:(1)層間結(jié)合機(jī)理;(2)超聲固結(jié)工藝參數(shù)優(yōu)化及建模;(3)異種材料結(jié)合特性;(4)支撐材料。本文從上述四個領(lǐng)域出發(fā),綜述超聲增材技術(shù)的理論和關(guān)鍵技術(shù)的研究進(jìn)展,分析其在航空航天領(lǐng)域的應(yīng)用現(xiàn)狀,并展望未來增材制造技術(shù)的發(fā)展趨勢。
1、超聲增材制造的研究現(xiàn)狀
1.1層間結(jié)合機(jī)理
針對超聲增材層間結(jié)合機(jī)理,已有學(xué)者分別從實(shí)驗(yàn)和數(shù)值模擬等方面進(jìn)行了大量研究。其中,最早發(fā)表相關(guān)研究成果的是英國拉夫堡大學(xué)的研究團(tuán)隊(duì)[17-19],他們研究了A13003材料層間嵌入纖維后界面處的微觀組織,發(fā)現(xiàn)界面處存在再結(jié)晶晶粒,表明金屬表面氧化層破裂并非層間結(jié)合的唯一因素,塑性變形也是重要原因之一(如圖3a所示)。
Mariani等[20]、Dehoff等[14]和Shimizu等[21]對超聲增材A16061和A13003材料的界面微結(jié)構(gòu)進(jìn)行了觀察(如圖3b所示),并提出界面塑性變形將導(dǎo)致動態(tài)再結(jié)晶,而再結(jié)晶過程中的晶界遷移伴隨著原子的擴(kuò)散和原子間結(jié)合的形成,這是超聲增材過程中結(jié)合形成的主要原因。
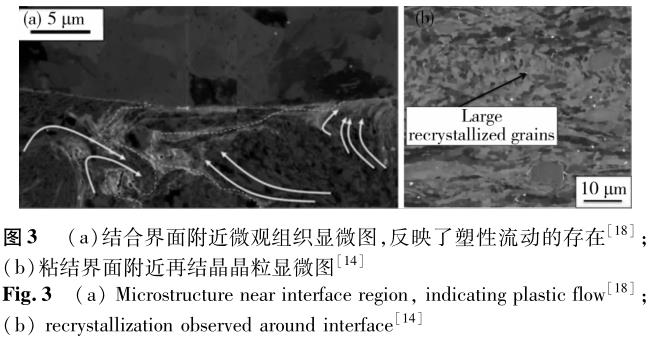
進(jìn)一步的微結(jié)構(gòu)觀察實(shí)驗(yàn)表明,在加工過程中,由于界面處塑性變形,主要在結(jié)合界面以下一定厚度區(qū)域內(nèi)發(fā)生動態(tài)再結(jié)晶現(xiàn)象,而界面以上只有很薄的區(qū)域出現(xiàn)了晶粒細(xì)化[8,14,22-24]。
同時,由于界面細(xì)小晶粒的存在,界面處材料的顯微硬度比本體材料高[25]。針對超聲增材過程的數(shù)值模擬研究工作主要集中在通過有限元數(shù)值模擬對超聲固結(jié)過程中的熱力耦合過程與結(jié)合形成過程的關(guān)系進(jìn)行分析。
對超聲增材過程中熱力耦合過程的數(shù)值模擬研究[26-28]表明,超聲增材加工過程中界面摩擦熱和塑性變形均會受到過程變量的影響,而塑性變形是結(jié)合形成的主要原因。Pal等[29-30]還將熱力耦合模型與位錯本構(gòu)模型相結(jié)合,對結(jié)合過程中位錯等結(jié)構(gòu)的變化進(jìn)行研究,結(jié)果表明,加工過程中界面處的晶粒破碎以及動態(tài)疲勞破壞會導(dǎo)致層間結(jié)合變?nèi)酢?/p>
1.2超聲固結(jié)過程參數(shù)優(yōu)化
由于超聲增材制造過程控制變量復(fù)雜,研究者大多通過實(shí)驗(yàn)來優(yōu)化過程參數(shù),并建立過程控制變量與粘結(jié)層微結(jié)構(gòu)和性能之間的關(guān)系。在第一代低功率超聲增材設(shè)備(SolidicaAlpha)[31]面世之初,Friel等[32-35]就通過剝離試驗(yàn)研究了振動振幅、焊接速度和下壓力對層間結(jié)合強(qiáng)度的影響,結(jié)果表明,提高振幅、降低速度和提高下壓力更有利于提高結(jié)合強(qiáng)度。Truog和Wolcott等[9-11,36]圍繞高功率增材制造設(shè)備開展研究,得到相似的結(jié)論,即高振幅、低速度有利于提高界面結(jié)強(qiáng)度,不同的是下壓力增加到一定程度(4000N)之后對界面結(jié)合強(qiáng)度不再產(chǎn)生影響。
Kong等[33-34]考慮壓力、速度和振動振幅這三個過程控制變量,通過實(shí)驗(yàn)試錯法建立了Al3003和Al6061的工藝參數(shù)操作窗口。Ram等[27-29]通過剝離試驗(yàn)和線性焊接密度(Linearweldingdensity,LWD)研究了A13003材料的層間結(jié)合強(qiáng)度以及層間結(jié)合完整度(如圖4所示),結(jié)果表明,升高基體預(yù)熱溫度以及采用使界面發(fā)生較大塑性變形的工藝參數(shù)有利于增加結(jié)合強(qiáng)度。桑健等[40]進(jìn)一步研究了基體加熱溫度對結(jié)合強(qiáng)度的影響,結(jié)果表明,銅箔固相結(jié)合強(qiáng)度在加熱溫度為100℃時最佳,為24.420N/mm,并隨界面最高溫度的升高先增大后減小。
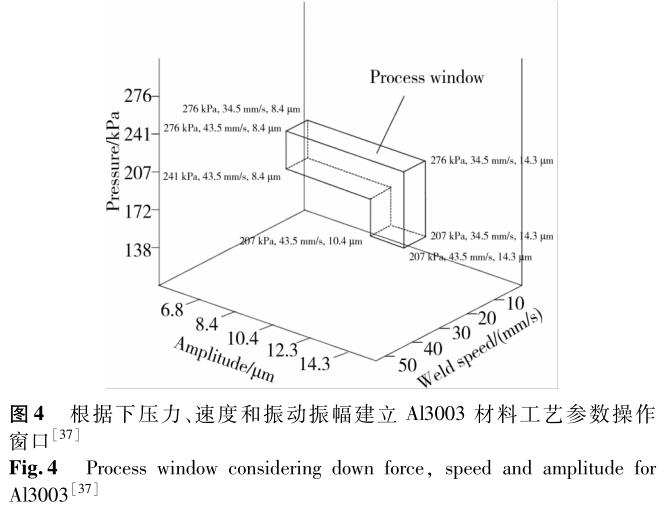
近年來,利用數(shù)值模擬技術(shù)開展層間結(jié)合特性研究受到廣泛關(guān)注。Kelly等[41-43]開發(fā)了基于聲學(xué)軟化模型的材料模型,以描述增材制造過程中材料的變形行為,利用有限元仿真建立過程參數(shù)(振幅、速度和下壓力)與焊接能量之間的關(guān)系,隨后通過試驗(yàn)建立焊接能量與層間結(jié)合強(qiáng)度之間的關(guān)系。除此以外,也有研究者圍繞超聲增材過程中的中間變量,建立其與層間結(jié)構(gòu)的關(guān)系,以得到在不同材料間具有泛化能力的模型或工藝窗口。
張松等[44-46]通過超聲固結(jié)實(shí)驗(yàn)及宏觀/微觀相結(jié)合的元胞自動機(jī)模型開展數(shù)值模擬研究。
不同于以往以振幅、速度和下壓力等作為控制變量,他們提出超聲增材過程中界面溫度和塑性應(yīng)變是影響層間結(jié)合的關(guān)鍵變量,并且上述關(guān)系不受材料特性的影響,通過研究該關(guān)鍵變量與界面微結(jié)構(gòu)特性以及層間結(jié)合質(zhì)量的關(guān)系,建立了鋁合金系列材料的過程圖,過程圖中已知材料操作窗口可支撐對未知材料進(jìn)行反向設(shè)計,實(shí)現(xiàn)不同材料加工過程的優(yōu)化。
此外,加工過程中隨著固結(jié)高度的增加,會出現(xiàn)層間結(jié)合強(qiáng)度逐漸減弱的現(xiàn)象。Robinson等[47]、Zhang等[48]和Gibert等[49]分別采用實(shí)驗(yàn)、有限元模型以及非動態(tài)Rayleigh-Ritz模型等手段研究了超聲固結(jié)過程中固結(jié)高度與帶材寬度之間的關(guān)系,均得到兩者之比約為1∶1。Gibert等[50]還研究了加工過程中的振動對焊接性能的影響,即當(dāng)結(jié)構(gòu)件的長、寬比大于0.7時(見圖5),加工時可能會引發(fā)結(jié)構(gòu)共振,導(dǎo)致粘結(jié)層產(chǎn)生缺陷甚至被破壞,并且他們建立了預(yù)測鋁合金是否發(fā)生共振的過程圖。
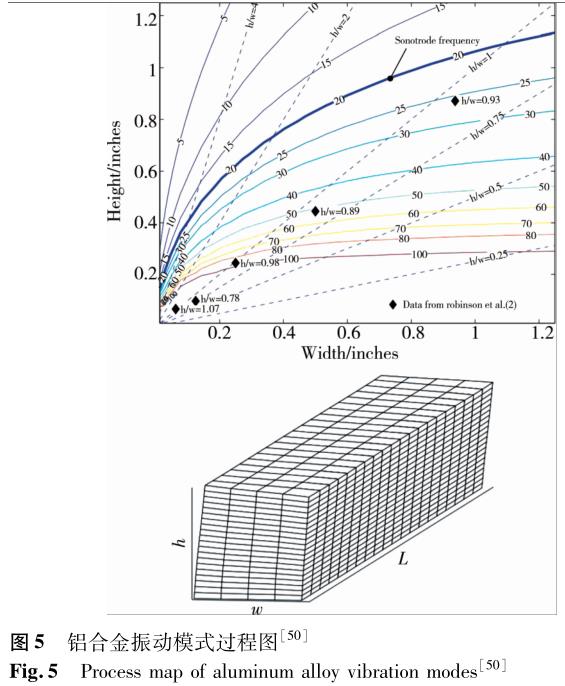
1.3異種材料及復(fù)合材料結(jié)合特性研究
隨著超聲增材技術(shù)應(yīng)用領(lǐng)域的不斷擴(kuò)展,異種材料結(jié)合或在帶材中嵌入功能纖維而形成具有特殊功能的復(fù)合材料等也不斷受到關(guān)注。
針對超聲增材實(shí)現(xiàn)異種材料結(jié)合的研究最早是由猶他州立大學(xué)的Ram等[5152]開展,他們通過對不同金屬帶材與Al3003結(jié)合的界面微觀組織研究,評估界面結(jié)合強(qiáng)度。隨后大量科研人員研究不同材料間的結(jié)合特性[53-57],結(jié)果表明,在鈦、銀、鉭、鋁、鉬、不銹鋼、鎳、鎳基合金、銅和MetPreg?幾種材料中,所有面心立方體金屬之間都可以很好地結(jié)合,只有Al1100和Al3003可以很好地與鉬、鉭和鈦這三種非面心立方體金屬很好地結(jié)合,而Al6061和以上三種金屬的結(jié)合能力適中。
對不同材料所加工形成的結(jié)構(gòu)而言,含有較多韌性材料的結(jié)構(gòu)在失效前的能量吸收能力也更好。不同金屬帶材與Al3003結(jié)合及界面微觀組織如圖6所示。
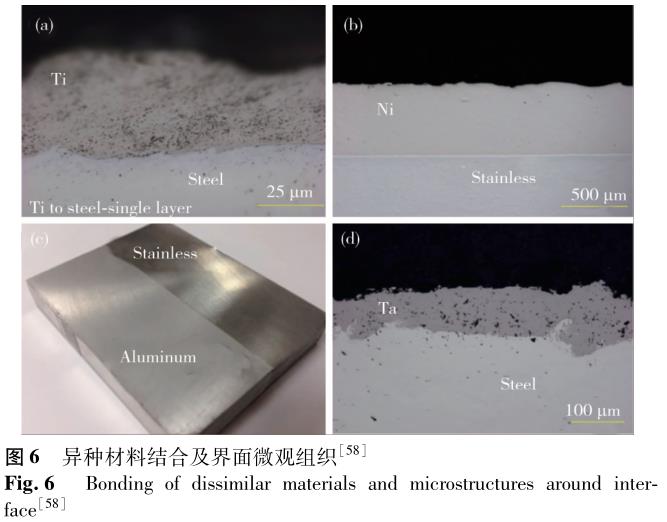
超聲固結(jié)過程冷加工和逐層疊加的特性使得其在某些特殊領(lǐng)域具有天然優(yōu)勢,如金屬帶材中層間嵌入結(jié)構(gòu)強(qiáng)化纖維和嵌入式傳感器等。
在嵌入纖維的結(jié)合原理方面,Mariani等[20]、Kong等[5960]通過觀察嵌入纖維的金屬帶材微結(jié)構(gòu)特征研究纖維與金屬帶材之間的結(jié)合機(jī)理,發(fā)現(xiàn)由于纖維周圍金屬的塑性流動使得纖維被機(jī)械地固定(見圖7a),金屬帶材與纖維之間并沒有發(fā)生明顯的擴(kuò)散或者化學(xué)反應(yīng)。
在嵌入纖維的結(jié)合強(qiáng)度研究方面,Kong等[61]研究了不同類型纖維(SiC、NiTi形狀記憶合金)嵌入鋁合金帶材時結(jié)合強(qiáng)度隨工藝參數(shù)的變化情況(見圖7b),并將該應(yīng)用擴(kuò)展到埋覆集成纖維和電子元器件等方向;Obielodan等[54]、Hahnlen等[62-63]在鋁帶材中嵌入結(jié)構(gòu)強(qiáng)化纖維制備了復(fù)合材料結(jié)構(gòu)件(見圖7c),試驗(yàn)表明纖維增韌的復(fù)合材料具有更高的比強(qiáng)度和剛度;Yang等[64]研究發(fā)現(xiàn)Al3003帶材嵌入SiC纖維時的結(jié)合強(qiáng)度主要受振動振幅、焊接速度、下壓力、基體預(yù)熱溫度以及嵌入纖維方向等過程變量的影響,優(yōu)化工藝參數(shù)為振幅20μm、焊接速度34mm/s、下壓力1700N、基體預(yù)熱溫度422K以及纖維方向45°。
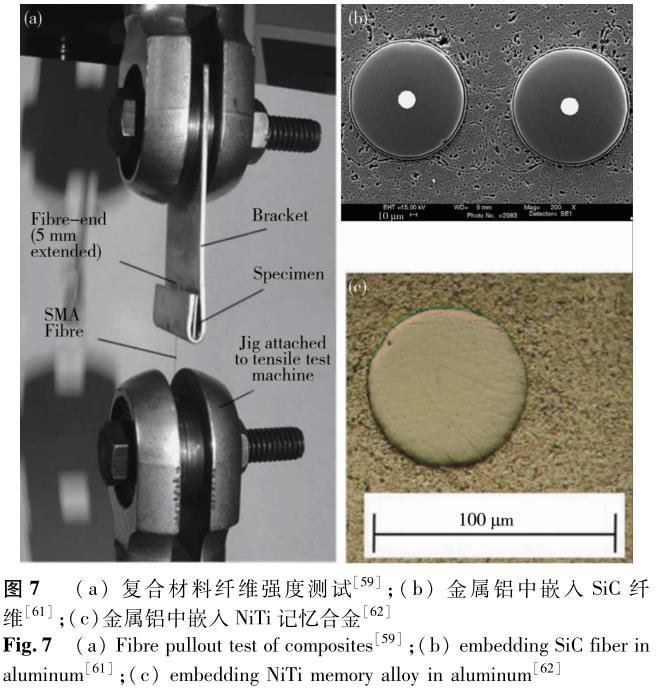
1.4支撐材料研究
由于超聲增材制造過程會帶給金屬帶材較大的下壓力,為了獲得復(fù)雜、精細(xì)的內(nèi)部結(jié)構(gòu),與其他高溫增材制造技術(shù)相比,金屬超聲增材制造過程需要更多的支撐材料,研究支撐材料對最終成形零件形狀和性能的影響十分重要。
猶他州立大學(xué)的Swank等[65-66]是最早開展超聲增材制造支撐材料研究的團(tuán)隊(duì),他們通過研究發(fā)現(xiàn)選擇堅硬且熔點(diǎn)高于焊接溫度的支撐材料更容易獲得高質(zhì)量的結(jié)構(gòu)件,并以此為據(jù)提出了多種適用于超聲增材制造過程的支撐材料類型,如無鉛焊料等。此外,克萊姆森大學(xué)和愛迪生焊接研究所的相關(guān)團(tuán)隊(duì)[67]也開展了支撐材料的研究。
2、金屬超聲增材技術(shù)在航空航天領(lǐng)域的應(yīng)用
從2014年開始,NASA噴氣實(shí)驗(yàn)室(JPL)與美國Fabrisonic公司合作,探索使用金屬超聲增材技術(shù)制備一體化熱管理系統(tǒng)來替代原有的分體式外部換熱管道,以達(dá)到減輕質(zhì)量、縮短加工時間的目的。圖8a為采用超聲增材技術(shù)打印的一體化換熱器,通過綜合利用支撐材料和機(jī)械加工,可實(shí)現(xiàn)將換熱管道打印到部件結(jié)構(gòu)中,從而提高換熱器的換熱效率和魯棒性。上述換熱器已經(jīng)通過NASAJPLTL6質(zhì)量測試,用于2020年NASA火星探測任務(wù)。據(jù)悉,利用增材制造技術(shù)打印的換熱器的質(zhì)量減少了30%,而制造周期也有一定的縮短。此外,利用超聲增材制造技術(shù)容易實(shí)現(xiàn)異種材料結(jié)合的特點(diǎn),可在換熱器的局部高溫區(qū)域采用導(dǎo)熱率高的銅,而其余位置采用輕質(zhì)鋁或鋁合金,從而在提高換熱性能的基礎(chǔ)上降低質(zhì)量損失(見圖8b)。
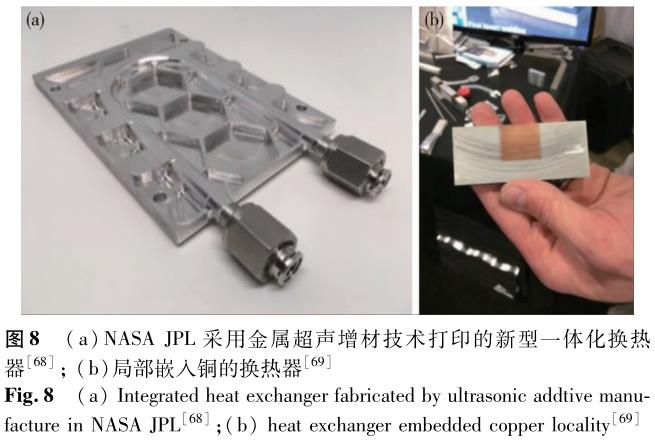
隨著數(shù)字孿生技術(shù)的興起,NASA聚焦航空解決方案項(xiàng)目(Convergencyaeronauticssolution,CAS)中的數(shù)字孿生子項(xiàng)目,正在探索嵌入式傳感器技術(shù),目的是對實(shí)際運(yùn)行系統(tǒng)的信息進(jìn)行實(shí)時采集,修正數(shù)字孿生模型以支撐運(yùn)行時的決策乃至快速設(shè)計。然而,航空航天設(shè)備多工作于極端環(huán)境,在部件外部安裝傳感器一方面可能干擾部件正常工作,另一方面絕大部分常規(guī)傳感器難以應(yīng)用于高溫高壓環(huán)境,導(dǎo)致目前實(shí)際使用的傳感器數(shù)量較少,采集的信息十分有限。利用超聲增材技術(shù)可以將對溫度敏感的傳感器直接嵌入結(jié)構(gòu)件中,如NASA與Fabrisonic公司合作[70],將直徑為195μm的光纖應(yīng)變傳感器(工作溫度:-180~260℃)嵌入鋁合金結(jié)構(gòu)件中,如圖9a所示,通過準(zhǔn)靜態(tài)和循環(huán)拉伸試驗(yàn)可知,經(jīng)校準(zhǔn)后傳感器的測量結(jié)果符合精度要求;隨后上述技術(shù)被用于NASA數(shù)字孿生項(xiàng)目中,在結(jié)構(gòu)件內(nèi)部應(yīng)力集中的區(qū)域(如圖9b所示),利用增材制造技術(shù)布置了30個光纖應(yīng)變傳感器,提前預(yù)測部件的疲勞壽命。為了進(jìn)一步擴(kuò)展傳感器的使用溫度范圍,光纖表面還沉積了一層金屬涂層。
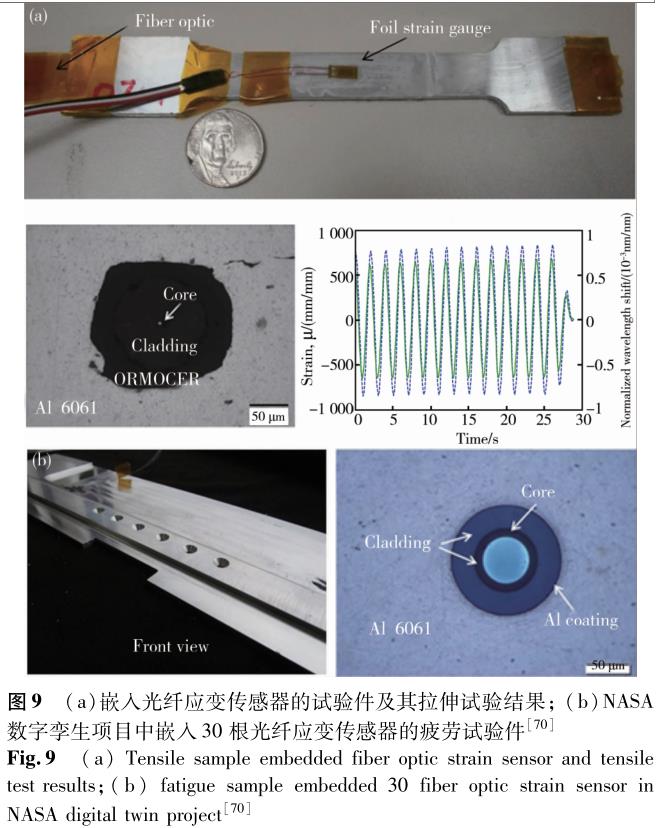
在役修復(fù)和快速替換是航空航天裝備維修保障的未來發(fā)展方向[71],而增材制造作為一種快速制造技術(shù),是目前最佳的實(shí)現(xiàn)途徑?;诩す饣螂娮邮母邷卦霾募夹g(shù)會使得局部區(qū)域的金屬呈熔融狀態(tài),需要嚴(yán)格控制周圍環(huán)境的氣氛,且原有基體中熱影響區(qū)域的尺寸和微結(jié)構(gòu)都將發(fā)生明顯的變化,導(dǎo)致殘余應(yīng)力增大、強(qiáng)度降低、修復(fù)區(qū)域組織非均勻化等,進(jìn)而影響修復(fù)后部件的疲勞特性乃至使用安全性。超聲增材制造作為一種低溫固態(tài)連接技術(shù),能夠克服上述不足,且由于金屬不會熔化,不需要控制周圍環(huán)境,對待修復(fù)部件尺寸沒有要求,使用領(lǐng)域更加廣泛。圖10為采用超聲增材制造修復(fù)直升機(jī)機(jī)翼前緣,通過逆向工程可以構(gòu)建出失效部件的2D或3D幾何結(jié)構(gòu),通過與原始部件進(jìn)行對比,獲得磨損區(qū)域的幾何特征,進(jìn)而驅(qū)動超聲增材設(shè)備將Al7075材料打印到磨損區(qū)域,修復(fù)幾何外形。
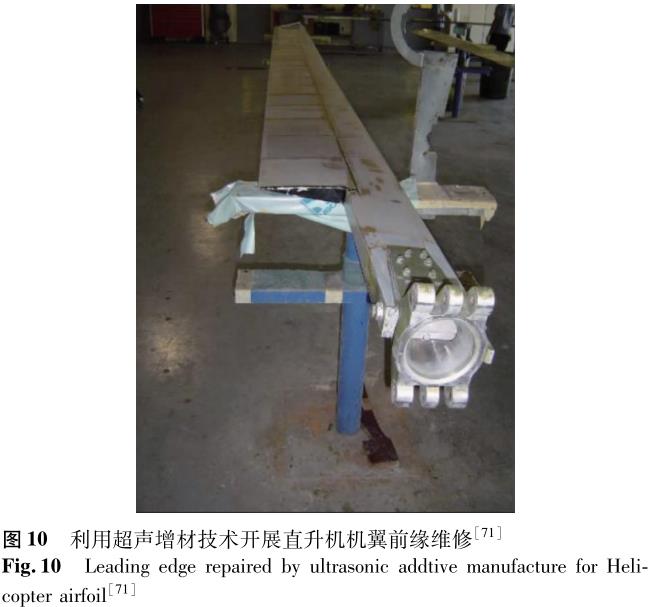
此外,超聲增材技術(shù)也常用于結(jié)構(gòu)減重,如制造點(diǎn)陣結(jié)構(gòu)和復(fù)合材料金屬連接件等。Geoge等[39]設(shè)計了一款納米衛(wèi)星(電離層擾動層析遙感器,TOROID)以測量低緯度電離層中的閃爍行為,進(jìn)而提供更精確的定位。
其中,基于模塊化的設(shè)計理念,為了將測量設(shè)備固定在衛(wèi)星上,需要采用具有蜂窩結(jié)構(gòu)的輕質(zhì)面板作為衛(wèi)星的主體結(jié)構(gòu)(見圖11a)。采用超聲增材技術(shù)制造蜂窩結(jié)構(gòu),不僅提供了較多的安裝空間,能夠獲得比復(fù)合材料更輕的質(zhì)量,還具有可在結(jié)構(gòu)內(nèi)部埋入電子元器件的優(yōu)勢。試驗(yàn)表明,該蜂窩結(jié)構(gòu)的剛度達(dá)到1151N/mm,能夠支撐衛(wèi)星的發(fā)射。
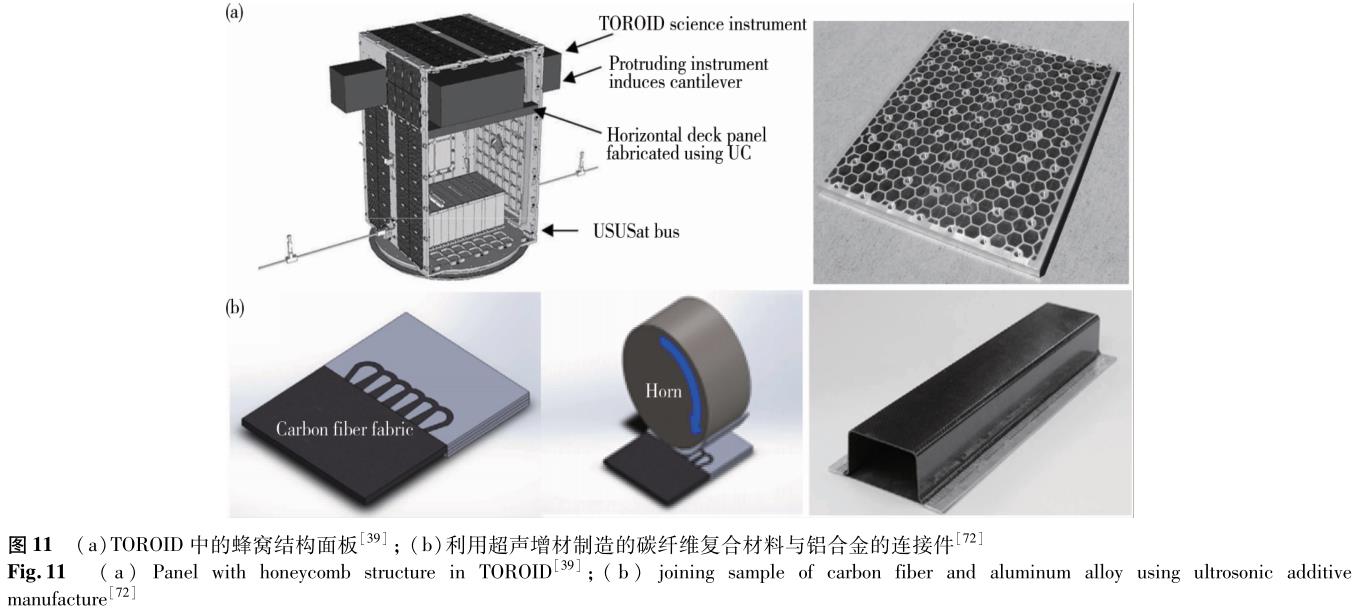
Guo等[72]利用超聲增材技術(shù)將碳纖維增韌聚合物復(fù)合材料(CFRP)與鋁合金板連接(見圖11b),其實(shí)現(xiàn)方式是通過超聲增材制備鋁合金板時,利用機(jī)械加工在其邊緣加工出一系列環(huán)形槽道,隨后將碳纖維繞成圈放置于槽道中,再利用超聲增材在其表面繼續(xù)打印鋁合金帶材,重復(fù)上述過程即可形成復(fù)合材料-金屬連接件。這可直接使用普通焊接方式將鋁合金與原有金屬結(jié)構(gòu)連接,從而實(shí)現(xiàn)在結(jié)構(gòu)設(shè)計中加入復(fù)合材料減重的同時不改變原有金屬結(jié)構(gòu)的加工工藝,降低制造成本,實(shí)現(xiàn)結(jié)構(gòu)減重。試驗(yàn)結(jié)果表明,采用超聲增材技術(shù)制備的復(fù)合材料-鋁合金連接件的抗拉強(qiáng)度可達(dá)125MPa,優(yōu)于其他加工方式。
3、展望
航空航天領(lǐng)域的復(fù)雜裝備往往在極端環(huán)境中工作,承受著高溫、高壓和高負(fù)荷,對部件的壽命和可靠性提出了極高的要求。此外,第四次工業(yè)革命激發(fā)了智能化設(shè)備的發(fā)展勢頭,數(shù)字孿生是未來的發(fā)展方向之一。
為了獲得虛實(shí)交互,需要精確采集實(shí)際設(shè)備工作過程中的狀態(tài)參數(shù),而先進(jìn)的傳感器技術(shù)是實(shí)現(xiàn)的基礎(chǔ)。
隨著超聲增材技術(shù)的發(fā)展及其可適用材料的不斷擴(kuò)展,結(jié)合當(dāng)前航空航天復(fù)雜裝備的應(yīng)用需求,可以推測未來超聲增材技術(shù)在航空航天領(lǐng)域?qū)⒂芯薮蟮膽?yīng)用潛力。
金屬超聲增材加工過程中的增材與冷加工使得該技術(shù)能在部分領(lǐng)域取得創(chuàng)新性的成果,總結(jié)起來大體分為三類(見圖12):
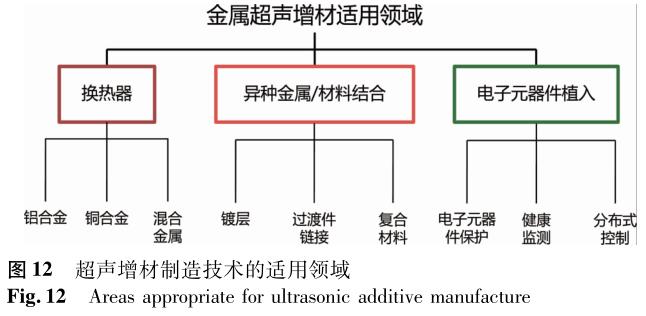
(1)一體化換熱器。
由于超聲增材加工過程中能引入機(jī)械加工,可以在鋁合金、銅合金和其他金屬結(jié)構(gòu)件內(nèi)部構(gòu)造出光滑、準(zhǔn)確的換熱通道,或者在結(jié)構(gòu)件外部構(gòu)造出一體化的換熱結(jié)構(gòu),這是常規(guī)加工方法難以實(shí)現(xiàn)的,可用于制造航天飛行器或者航空發(fā)動機(jī)中的換熱器結(jié)構(gòu)以及受外載荷較輕的熱端部件,如低壓渦輪靜子葉片等。
(2)異種材料結(jié)合。
超聲增材過程溫度較低,金屬間化合物很難形成,容易實(shí)現(xiàn)異種材料結(jié)合的金屬基復(fù)合材料,從而提升制造件的性能,比如制備表面覆層、過渡連接件和復(fù)合材料結(jié)構(gòu)件等,也可用于失效部件局部區(qū)域的表面修復(fù);同時通過工藝設(shè)計,可以實(shí)現(xiàn)金屬與非金屬材料的連接,進(jìn)而達(dá)到功能增強(qiáng)與減重的目的。
(3)電子元器件植入。
同樣得益于超聲增材技術(shù)的低溫加工特性,可將一些對熱敏感的電子元器件或傳感器植入金屬基體中,一方面能夠獲得應(yīng)力集中區(qū)域等關(guān)鍵位置精確的測量信息,另一方面也能防止傳感器被磨損或破壞。
例如,采用增材制造將傳感器和微處理控制系統(tǒng)等電子元器件埋入航天器或其子系統(tǒng)的外殼中,構(gòu)建一體化智能蒙皮,實(shí)現(xiàn)智能感知、預(yù)測與控制,從而提高飛行器或其子系統(tǒng)的使用性能。
4、結(jié)語
金屬超聲增材制造技術(shù)由于具有低溫加工特性,在制造過程中不會引發(fā)金屬材料熔化,因此相對于其他高溫增材技術(shù),其有著獨(dú)特的適用領(lǐng)域,如異種材料結(jié)合、熱敏電子元器件植入等。國內(nèi)外對超聲增材的研究主要集中在層間結(jié)合機(jī)理、超聲固結(jié)過程參數(shù)優(yōu)化、異種材料或復(fù)合材料結(jié)合特性研究及支撐材料研究等四個方面。
目前對超聲增材層間結(jié)合機(jī)理的研究表明,界面處金屬的塑性變形和隨之產(chǎn)生的動態(tài)再結(jié)晶是層間結(jié)合產(chǎn)生的原因。為了提高結(jié)合質(zhì)量,需要對振動振幅、下壓力、速度、形狀和基底溫度等過程參數(shù)進(jìn)行優(yōu)化,目前針對鋁合金系列(如Al3003、Al6061等)材料利用試驗(yàn)和數(shù)值仿真建立了過程窗口,可用來指導(dǎo)實(shí)際加工過程。關(guān)于異種材料及復(fù)合材料結(jié)合機(jī)理,研究重點(diǎn)在于結(jié)合形成的機(jī)理及微觀組織和性能表征。此外,為了拓展超聲增材的實(shí)際應(yīng)用范圍,也有部分學(xué)者致力于研究支撐材料對制造過程的影響,提出選擇依據(jù)以指導(dǎo)實(shí)際加工。在工程應(yīng)用方面,針對復(fù)雜服役環(huán)境下的航空航天領(lǐng)域復(fù)雜裝備,綜合使用超聲增材制造制備高效換熱通道、纖維增韌復(fù)合材料,并將熱敏電子元器件埋入結(jié)構(gòu)件中,形成具備結(jié)構(gòu)功能一體化和狀態(tài)實(shí)時感知的智能結(jié)構(gòu)件,將推動航空航天復(fù)雜裝備朝著輕質(zhì)、高效和智能的方向發(fā)展。
參考文獻(xiàn)
1HuangQS,LiLQ,GaoBB.DefenseManufacturingTechnology,2012(5),26(inChinese).黃秋實(shí),李良琦,高彬彬.國防制造技術(shù),2012(5),26.
2LyuYX.FineandSpecialtyChemicals,2014,22(11),14(inChi-nese).
呂延曉.精細(xì)與專用化學(xué)品,2014,22(11),14.
3WangHM,ActaAeronauticaetAstronauticaSinica,2014,35(10),2690(inChinese).
王華明.航空學(xué)報,2014,35(10),2690.
4YinYG,BaiPK,LiuB.PowderMetallurgyTechnology,2006(2),142(inChinese).
尹貽國,白培康,劉斌.粉末冶金技術(shù),2006(2),142.
5WhiteD.AdvancedMaterialsandProcesses,2003,161(1),64.
6GraffKF,ShortM,NorfolkM.In:InternationalSoldFreeformFabrica-tionSymposiumAnAdditiveManufacturingConference.Austin,2010,
pp.362.
7FujiiHT,ShimizuS,SatoYS,etal.ScriptaMaterialia,2017,135,125.
8FujiiHT,SriramanMR,BabuSS.Metallurgical&MaterialsTransac-tionsA,2011,42A(13),4045.
9TruogASR,BabuS.In:ASMProceedingsoftheInternationalConfe-rence:TrendsinWeldingResearch.ChicagoIL,2013.
10WolcottPJ,HehrA,DapinoMJ.JournalofMaterialsResearch,2014,29(17),2055.
11WolcottPJ,HehrA,PawlowskiC,etal.JournalofMaterialsProcessingTechnology,2016,233,44.
12SchickDE,BabuSS,LippoldJC,etal.WeldingJournal,2010,89(5),105S.
13SchickD,BabuSS,FosterDR,etal.RapidPrototypingJournal,2011,17(5),369.
14DehoffRR,BabuSS.ActaMaterialia,2010,58(13),4305.
15WolcottPJ,DapinoM.In:23rdAnnualInternationalSolidFreeformFabricationSymposium-AnAdditiveManufacturingConference,
SFF2012.Austin,2012,pp.428.
16HeXH,ShiHJ,ZhangYD,etal.MaterialsLetters,2013,112,47.
17JohnsonKHR,DickensP,WestG,GuptaA.In:MaterialsScienceandTechnologyConferenceandExhibition,MSandT′07-′ExploringStructure,Processing,andApplicationsAcrossMultipleMaterialsSys-tems′.Detroit,2007,pp.2618.
18JohnsonKEH,HigginsonR,HarrisR.ProceedingsoftheInstitutionofMechanicalEngineers,PartL:JorunalofMaterials:DesignandApplica-tions,2011,225(4),277.
19FrielRHR.ProceedingsoftheInstitutionofMechanicalEngineers,PartL:JournalofMaterials:DesignandApplications,2010,224(1),31.
20MarianiE,GhassemiehE.ActaMaterialia,2010,58(7),2492.
21ShimizuS,FujiiHT,SatoYS,etal.ActaMaterialia,2014,74,234.
22SriramanMR,BabuA,ShortM.ScriptaMaterialia,2010,62(8),560.
23SriramanMFH,GonserM.In:ProceedingsoftheTwentyFirstInterna-tionalSolidFreeformFabricationSymposium.UniversityofTexas,Aus-tin,2010.
24JohnsonK.InterlaminarSubgrainRefinementinUltrasonicConsolida-tion.Ph.D.Thesis,OlivetNazareneUniversity,USA,2008.
25SojiphanKSM,BabuS.In:ProceedingsoftheTwentySecondAnnualInternationalSolidFreeformFabricationSymposium.UniversityofTexas,Austin,2010.
26ZhangCLL.WeldingJournal,2008,87(7),187.
27ZhangCS,LiL.Metallurgical&MaterialsTransactionsB,2009,40(2),196.
28SiddiqAGE.JournalofManufacturingScienceandEngineering,2009,131(4),041007.
29PalDSBE.VirtualandPhysicalPrototyping,2012,7(1),65.
30PalD,StuckerB.JournalofAppliedPhysics,2013,113(20),64.
31HehrA,NorfolkM.RapidPrototypingJournal,2019,26(3),445.
32FrielRJ,HarrisRA.In:TwentyThirdInternationalSolidFreeformFabricationSymposiumAnAdditiveManufacturingConference.Austin,2012,pp.354.
33KongCY,SoarRC,DickensPM.MaterialsScience&EngineeringA,2003,363,99.
34KongCY,SoarRC,DickensPM.JournalofMaterialsProcessingTech-nology,2004,146(2),181.
35KongCSR,DickensP.ProceedingsoftheInstitutionofMechanicalEn-gineers,PartC:JournalofMechanicalEngineeringScience,2005,219(1),83.
36WolcottPJ,SridharanN,BabuSS,etal.ScienceandTechnologyofWeldingandJoining,2016,21(2),114.
37RamG,YangY,StuckerBE.JournalofManufacturingSystems,2006,25(3),221.
38RobertBT.JournalofManufacturingProcesses,2007,9(2),87.
39GeorgeJSB.VirtualandPhysicalPrototyping,2006,1(4),227.
40SangJ,WangB,ZhuXM,etal.MaterialsReportsB:ResearchPapers,2018,32(9),104(inChinese).
桑健,王波,朱訓(xùn)明,等.材料導(dǎo)報:研究篇,2018,32(9),104.
41KellyGS,AdvaniSG,GillespieJW,etal.JournalofMaterialsPro-cessingTechnology,2013,213(11),1835.
42KellyGS,JustMS,AdvaniSG,etal.JournalofMaterialsProcessingTechnology,2014,214(8),1665.
43KellyGAS,GillespieJ.InternationalJournalofAdvancedManufacturingTechnology,2015,79(912),1931.
44ZhangSong,YiDalong,ZhangHui,etal.RapidPrototypingJournal,2015,21(4),461.
45SongZ,ZhengL,HuiZ.In:ProceedingsoftheASME2014InternationalMechanicalEngineeringCongressandExpositionIMECE2014.Montreal,2014,pp.37203.
46YiD,ZhangS,ZhangH,etal.MaterialsScienceandTechnology,2017,33(6),744.
47RobinsonCJ,ZhangC,JanakiGD,etal.In:InternationalSolidFree-formFabricationSymposium,Austin,2006,pp.502.
48ZhangCS,LiL.Ultrasonics,2010,50(8),811.
49GibertJM,AustinEM,FadelG.RapidPrototypingJournal,2010,16(4),284.
50GibertJM,McculloughDT,FadelGM,etal.In:23rdAnnualInter-nationalSolidFreeformFabricationSymposiumAnAdditiveManufacturingConference.Austin,2012,pp.385.
51RamG,RobinsonC,YangY,etal.RapidPrototypingJournal,2007,13(4),226.
52AdamsBNC,AydelotteB,AhmadiS,etal.ActaMaterialia,2008,56(1),128.
53BourellD,ObielodanJO,CeylanA,etal.RapidPrototypingJournal,2010,16(3),180.
54ObielodanJ,StuckerB.InternationalJournalofAdvancedManufacturingTechnology,2014,70(14),277.
55GraffKDJ,KeltosJ,ZhouN,etal.Ch8:ultrasonicweldingofmetals,inAWSWeldingHandbook,2001.
56HanYJ,JiangB,HouHL,etal.ChineseJournalofRareMetals,2020(6),597(inChinese).
韓玉杰,姜波,侯紅亮,等.稀有金屬,2020(6),597.
57WangB,ZhangHT,ZhuXM,etal.JournalofMechanicalEngineering,2018,54(22),95(inChinese).
王波,張洪濤,朱訓(xùn)明,等.機(jī)械工程學(xué)報,2018,54(22),95.
58https://fabrisonic.com/resources/.
59KongCY,SoarRC,DickensPM.CompositeStructures,2004,66(1-4),421.
60KongCY,SoarR.AppliedOptics,2005,44(30),6325.
61KongCY,SoarRC.MaterialsScience&EngineeringA,2005,412(1-2),12.
62HahnlenR,DapinoMJ.ProcSpie,2010,7645,15.
63HahnlenR,DapinoMJ.CompositesPartB,2014,59,101.
64YangY,JanakiRGD,StuckerBE.JournalofEngineeringMaterialsandTechnology,2007,129(4),538.
65SwankMSB.In:20thAnnualInternationalSolidFreeformFabricationSymposium,SFF2009.AustinTX,2009.
66SwankMSB,MedinaF,WickerR.In:20thAnnualInternationalSolidFreeformFabricationSymposium,SFF2009.AustinTX,2009.
67GibertJMD,FadelG,JohnsonK.In:23rdAnnualInternationalSolidFreeformFabricationSymposium-AnAdditiveManufacturingConference,SFF2012.AustinTX,2012.
68https://fabrisonic.com/.
69https://3dprint.com/220995/heat-exchanger-whitepaper/.
70HehrA,NorfolkM,WenningJ,etal.JOM:theJournaloftheMinerals,Metals&MaterialsSociety,2018,70(3),315.
71SchwopeLA,FrielRJ,JohnsonK,etal.In:MeetingProceedingsRTOMP-AVT-163-AdditiveTechnologyforRepairofMilitaryHardware.Bonn,2009,pp.22.
72GuoHQ,GingerichMB,HeadingsLM,etal.CompositeStructures,2019,208,180.
相關(guān)鏈接