引言
磁控濺射是一種常見的物理氣相沉積方法,具有沉積溫度低、沉積速度快、方便多個靶材進行材料合成等優(yōu)點,常用于金屬[1-3]、半導體[4-6]、絕緣體[7-9]等多種薄膜材料的制備。然而,在磁控濺射過程中,不同材料的濺射原子角分布差異很大[10],而且合金材料的一些參數(shù)不易設定,因此采用晶振片監(jiān)測沉積薄膜厚度有很大的局限性。在實際使用中,通常選擇控制濺射工藝時間來控制所制備沉積薄膜厚度。具體做法
是:在一小段時間內濺射沉積某種薄膜,采用臺階儀測得厚度值并換算成沉積速率;當制備具體厚度的該材
料薄膜時,只需簡單的比例運算,就可得到沉積該厚度所需要的時間。
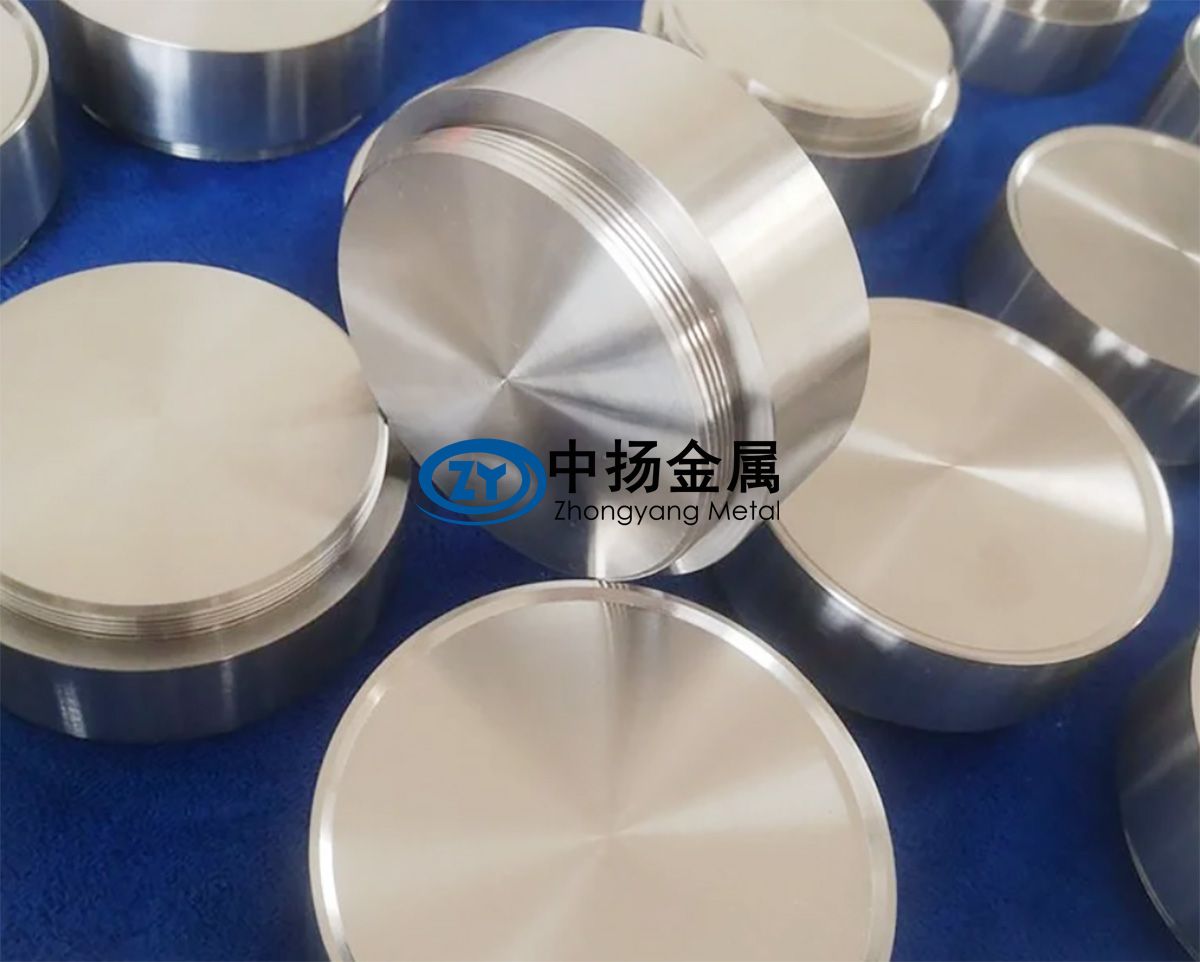
在大量的實驗記錄中發(fā)現(xiàn),通過控制濺射工藝時間來控制薄膜厚度的方法也存在一定的缺陷。當濺射靶材為銅、鋁、鈦、鉻等金屬靶材時,沉積薄膜厚度和濺射工藝時間符合線性規(guī)律,采用濺射工藝時間控制沉積薄膜厚度比較科學。然而,當靶材為氧化鋅、二氧化硅等導熱差的材料時,隨著濺射工藝時間的延長,濺射速率在一定時間后突然增加,出現(xiàn)“濺射失重”現(xiàn)象[10],讓沉積薄膜厚度變得不再可控。為此,根據(jù)所用設備的特點和靶材的實際導熱情況以及濺射時腔內的溫度變化建立數(shù)學模型,采用Matlab軟件模擬靶材表面溫度隨濺射工藝時間的變化關系,闡明氧化鋅、二氧化硅靶材濺射速率突然增加的原因。
1、實驗部分
磁控濺射鍍膜設備為explore-14多靶磁控濺射鍍膜系統(tǒng),共有3個直徑為3in(lin=2.54cm)的水冷靶槍,配備2個直流電源和1個射頻電源。水冷靶槍的常年溫度約為25℃。靶材中心距工件臺中心約為15cm,靶平面與工件臺平面的夾角約為45°。選用直徑3in的銅、鋁、氧化鋅和二氧化硅靶材,靶材純度均為99.999%,靶材厚度為5mm。襯底均為4in清洗干凈的單面拋光硅片。
所有待沉積薄膜的硅片在放置于工件臺之前,貼好十字形聚酰亞胺膠帶,方便后序臺階儀測量薄膜的厚度。
1.1 銅靶材濺射
在2個直流靶上分別安裝鉻和銅靶材。將腔內抽真空到0.1MPa后,對2個靶材預濺射清洗2min。靶材濺射清洗具體工藝條件為:工作氣壓0.8Pa,濺射功率300W。然后,對已經放置于工件臺上的硅片襯底濺射沉積薄膜。具體做法如下:先在硅片上濺射約10nm的鉻,增加銅和襯底的黏附性。濺射鉻的工藝條件為:濺射功率300W,工作氣壓0.8Pa,濺射工藝時間40s,工件臺旋轉速度10r/min。關閉鉻靶電源,打開銅靶電源對襯底進行濺射。濺射銅的工藝條件為:濺射功率300W,工作氣壓0.8Pa,濺射工藝時間15min,工件臺旋轉速度10r/min。濺射完畢后,取出樣品并測量厚度。更換為全新的銅靶和待沉積的硅片樣品,重復上述制備銅膜的工藝步驟,將濺射工藝時間分別延長為30、45、60、75、90、105、120min。需要注意的是,為了實驗
的嚴謹性,每制備一次新樣品都要更換全新的銅靶材。在所有濺射過程中,為了防止腔內環(huán)境溫度升高,
腔壁吸附的水分子釋放出來影響濺射速率,采用液氮在分子泵前端的冷阱進行制冷。制冷間隔為每30min
加注一次液氮。
1.2 鋁靶材濺射
鋁靶材濺射和銅靶材濺射的工藝步驟相同,濺射前對靶材預濺射清洗2min。鋁靶材的濺射功率為300W,工作氣壓為0.8Pa,工件臺旋轉速度為10r/min,首次濺射工藝時間為15min,后續(xù)濺射工藝時間分別為30、45、60、75、90、105、120min。2個直流靶上分別安裝鈦和鋁靶材,鈦作為鋁膜的黏附層每次沉積約10nm。工藝條件為:濺射功率300W,工作氣壓0.8Pa,濺射工藝時間30s。每制備一次新樣品后都要更換全新的鋁靶材。
1.3 氧化鋅靶材濺射
氧化鋅靶材安裝在射頻電源靶槍上。腔內抽真空到0.1MPa后,對氧化鋅靶材預濺射清洗2min。預濺射功率為300W,工作氣壓為0.8Pa。在沉積氧化鋅薄膜之前,用50W的負偏壓功率對襯底預清洗3min,增加薄膜和襯底的結合力。濺射氧化鋅靶材的工藝條件和濺射銅、鋁靶材的工藝條件相同。每制備一次新樣品都要更換全新的氧化鋅靶材。后續(xù)的系列實驗將濺射工藝時間分別設定為30、45、60、75、90、105、120min,制備好樣品后測量厚度。
1.4 二氧化硅靶材的濺射
二氧化硅靶材的濺射工藝參數(shù)與步驟和氧化鋅靶材的完全相同,實驗細節(jié)不再贅述。
2、實驗結果
去掉硅片上的聚酰亞胺膠帶,采用KLA-TencorP7臺階儀多次測量硅片不同位置所制備樣品薄膜的厚度,求平均值。相同濺射功率、不同濺射工藝時間下沉積的銅、鋁、氧化鋅、二氧化硅薄膜具體厚度如表1和圖1所示。

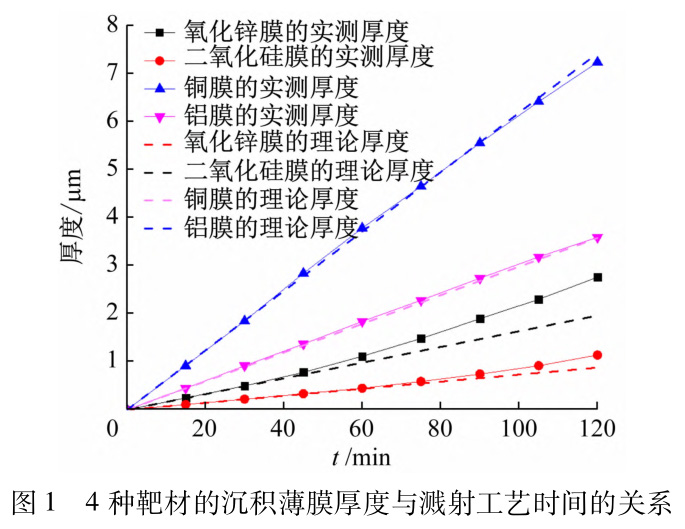
3、分析與討論
由實驗測試結果可知,銅、鋁2種金屬的沉積薄膜厚度和濺射工藝時間幾乎呈線性變化。在濺射工藝時間40~80min區(qū)間內,銅膜的實際沉積厚度比理論值略有增加。造成這種結果的原因可能是:隨著銅靶材的消耗、刻蝕槽的加深,更多的磁場力線露出靶面,對電子的束縛能力更強,電子與氬氣碰撞產生更多的氬離子,造成濺射產額增加,薄膜的沉積速率略快;當濺射工藝時間超過90min,刻蝕槽的繼續(xù)加深導致“空心陰極效應”現(xiàn)象的產生,加速銅膜沉積速率的降低[11]。在濺射工藝時間60~105min區(qū)間內鋁薄膜沉積速率略增加,在105~120min區(qū)間內沉積速率略下降,這是因為鋁靶的濺射速率比銅靶慢,變化趨勢也會相應延遲。
氧化鋅和二氧化硅薄膜實際沉積厚度在前期與理論值較吻合,當濺射工藝時間繼續(xù)增加后,實際厚度逐漸比理論值偏大,甚至出現(xiàn)了“濺射失重”的現(xiàn)象。這可能是由靶材的導熱性能不好、靶材表面溫度過高所造成的。根據(jù)所用濺射鍍膜設備的具體特點和靶材的導熱情況嘗試建立數(shù)學模型。
當靶材的濺射功率為300W時,大約只有1%的入射離子能量轉移到逸出的濺射原子中[12]。剩下的能量一部分消耗在靶材的表層,轉化為晶格的熱振動,使靶材表面溫度升高;另一部分用于氬氣電離,釋放的熱量以熱輻射的形式對外傳熱。設靶材表面溫度為T,當時間為t、冷水靶槍的溫度恒定為25時,溫度與時間的關系為

其中:S為實際導熱面積;λ為材料的平均導熱系數(shù);h為靶材厚度;K為靶材和靶槍兩界面間的傳熱系數(shù);m為靶材質量;c為靶材比熱容;Q為濺射時整個腔體吸收的熱量。
以銅靶材為例,在濺射過程中氬離子轟擊主要集中在刻蝕槽區(qū)域,靶材底部的實際導熱面積S約為4cm2,平均導熱系數(shù)λ約為400W/(m.K),厚度h為5mm,K約為1mW/(m2.K),m約為0.2kg,c約為0.4mJ/(kg·℃),腔體吸收的熱量Q與靶材表面的溫度存在比例關系(Q=200T)。代入以上數(shù)據(jù),銅靶材表面溫度與濺射工藝時間的關系為
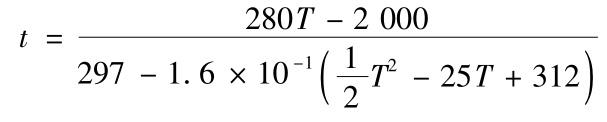
將另外3種材料的平均導熱系數(shù)、靶材質量、靶材比熱容等數(shù)據(jù)代入式(1)后,用Matlab軟件模擬出靶材表面溫度隨濺射工藝時間的變化,如圖2所示。
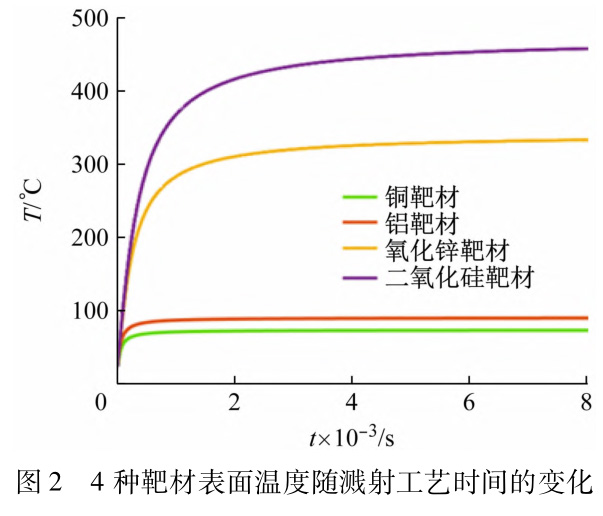
由圖2模擬結果可知,對于銅、鋁2種靶材,在濺射開始時靶材表面溫度迅速升高。隨著靶材表面和水冷靶槍溫差變大,熱量傳輸更加迅速。由于銅、鋁的導熱性能良好,在工藝開始的10min后,濺射產生和導走的熱量趨于平衡,銅靶和鋁靶表面溫度不再升高,分別約為75℃和94℃。兩者均沒有達到材料“濺射失重”的臨界溫度,所以在整個實驗中沉積薄膜厚度和濺射工藝時間幾乎是呈線性變化的。
對于氧化鋅和二氧化硅2種靶材,由于材料的導熱性能較差,加上材料溫度的升高,因此導熱性能隨之下降[13]。靶材表面的熱量向水冷靶槍傳輸比較困難,靶材表面溫度不斷升高。在約345℃和472℃時,氧化鋅和二氧化硅靶材表面溫度趨于穩(wěn)定。靶材表面溫度的升高造成材料鍵長增加和穩(wěn)定性變差。
當溫度達到某一臨界值時,氬離子轟擊靶材表面,更多的原子克服材料間的鍵能而逸出靶面,因此出現(xiàn)了“
濺射失重”現(xiàn)象。在相同的工藝條件下,氧化鋅靶材“濺射失重”現(xiàn)象比二氧化硅靶材出現(xiàn)較早,這可能
是由氧化鋅的鍵能約為270kJ/mol,而二氧化硅的鍵能約為799kJ/mol[14],氧化鋅靶材中氧和鋅鍵能較低的緣故造成的。
4、結語
在使用磁控濺射鍍膜設備沉積薄膜時,隨著濺射工藝時間的延長,銅、鋁靶材的濺射速率變化不大,而
氧化鋅、二氧化硅等靶材出現(xiàn)突然加速的“濺射失重”現(xiàn)象。由靶材表面溫度與濺射工藝時間的變化關系
可知,氧化鋅和二氧化硅導熱性能不良造成靶材表面溫度比銅、鋁靶材表面溫度高。靶材表面溫度超出“
濺射失重”的臨界溫度,可能是氧化鋅和二氧化硅靶材濺射速率突然增加的原因。
參考文獻(References):
[1]?。裕螅澹耄铮酰?,MartinhoF,MiakotaD,etal.Thee
ffectofsoft-annealingonsputteredCu2ZnSnS4thi
n-filmsolarcells[J].AppliedPhysicsA,2022,128:
970.
[2]?。蹋椋?,WangQ.Compositioncontrolandselecti
veinfraredradiativepropertiesofcopperalloyoxi
desbyDCreactivesputtering[J].JournalofPhysic
s:ConferenceSeries,2022,2248:012008.
[3]?。蹋椋睿?,ZhangY,ZhuZ,etal.Radiofrequency
sputteredfilmsofcopper-dopedzinctelluride[J].
ChemicalPhysicsLetters,2021,767:138358.
[4]?。粒酰纾酰螅簦椋睿?,UdupaKR,BhatKU.Characteriza
tionofDcmagnetronsputteredcopperthinfilmona
luminumtouchsurface[J].Transactionsoftheindianin
stituteofMetals,2019,72(6):1683-1685.
[5]?。佴桑欤洇桑颚桑恚?,Ka?arE,Kιsacιk?,etal.investig
atingmechanicalpropertiesofB4Cfilmsproduced
bymagnetronsputteringPVD[J].SolidStateScienc
es,2023,146:107336.
[6] 付學成,烏李瑛,權雪玲,等.Mg和V2O5共濺射制備+4價釩的氧化物薄膜[J]
.紅外技術,2022,44(1):79-84.
[7] 焦宇澤,杜欣欣.CdTe薄膜射頻磁控濺射法制備研究[J].光源與照明,2023(8
):57-59.
[8] 許 飛,朱江轉,陸 慧,等.射頻反應磁控濺射生長ZAO薄膜的光電性質[J].
實驗室研究與探索,2019,38(11):46-50.
[9] 郝蘭眾,劉云杰,張亞萍,等.金屬Pd摻雜對MoS2/Si異質薄膜微結構和光
伏性能的影響[J].實驗室研究與探索,2017,36(6):
13-17.
[10] 張以忱.真空鍍膜技術[M].北京:冶金工業(yè)出版社,2009.
[11] 鄭澤林,付學成,王 英,等.鋁濺射沉積速率與刻蝕槽深度變化關系研究[J].真空
科學與技術學報,2018,38(7):610-614.
[12] 石玉龍,閆鳳英.薄膜技術與薄膜材料[M].北京:化學工業(yè)出版社,2015.
[13] 黃 昆.固體物理學[M].北京:高等教育出版社,2002.
[14] 夏玉宇.化學實驗室手冊[M].2版.北京:化學工業(yè)出版社,2015.
相關鏈接