鈦是一種高活性金屬元素,經(jīng)常被用在飛機(jī)、火箭、導(dǎo)彈及化工行業(yè)等。根據(jù)鈦及鈦合金金相組織形態(tài),可將其分為α型鈦合金、α+β型鈦合金、β型鈦合金。工業(yè)純鈦由于含有6%以下的鋁和少量中性元素,且退火后幾乎全部為α相,因此屬于α型鈦合金。根據(jù)雜質(zhì)元素含量,一般可將工業(yè)純鈦劃分為三個等級:即TA1、TA2、TA3。TA2作為α鈦合金的一種,為hcp結(jié)構(gòu),電阻率為0.47Ω·mm2/m,密度為4.505g/cm3,一般可生產(chǎn)各種規(guī)格的管材、棒材、帶材、型材和箔材[1]。
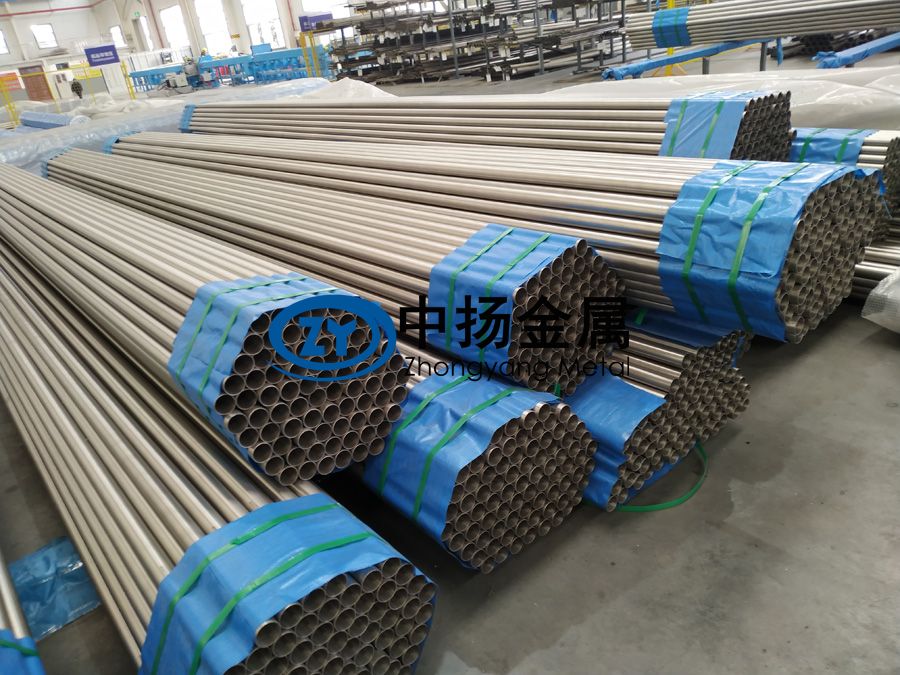
小口徑TA2鈦管材較鎳基合金、不銹鋼等金屬材料具有較高的屈強(qiáng)比、良好的熱穩(wěn)定性,低間隙元素含量、超低溫韌性以及優(yōu)異的抗大氣腐蝕性能,因此,經(jīng)常被用作液體火箭發(fā)動機(jī)的重要組成部件[2-5]。一般小口徑TA2管材尺寸規(guī)格多為(φ4~φ8)mm×(0.8~1.5)mm,主要通過坯料制備(斜軋穿孔或擠壓)加軋制工藝來獲得。但由于小口徑TA2管材使用環(huán)境的特殊性,尺寸精度要求高,管材內(nèi)外表面不允許有裂紋、起皮、針孔等缺陷,因此要制備性能優(yōu)良的TA2小口徑管材是十分不易的[6]。目前國內(nèi)對小口徑TA2管材的制備工藝研究較少,贠鵬飛等[7]研究了軋制Q值對小口徑TA2管材的力學(xué)性能及顯微組織進(jìn)行了研究,邢健等[8]對TA2管材織構(gòu)及性能進(jìn)行了研究,尚笑宇等[9]研究了冷軋變形量對TA2純鈦板材組織性能的影響,楊英子等[10]研究了氧含量及軋制工藝對純鈦管材性能的影響。本文主要通過兩種不同加工工藝制備得到了相同尺寸規(guī)格的高精度小口徑TA2管材,并對比研究了加工工藝對小口徑TA2管材組織及性能的影響。
1、試驗材料與方法
試驗原料采用電弧爐制得的φ96mm×27mm的TA2鈦棒,其中雜質(zhì)元素含量(質(zhì)量分?jǐn)?shù),%)為:0.30Fe、0.15O、0.10C、0.05H、0.15N。TA2棒通過兩種不同加工工藝最終制得φ8mm×1mm的小口徑TA2管材。第1種工藝為:將鈦棒下料、機(jī)加、擠壓得到φ41mm×φ23mm的管坯,再將經(jīng)過表面處理及酸洗后得到的φ39mm×6.25mm管坯進(jìn)行多道次冷軋至φ8mm×1mm,其中從φ39mm×6.25mm至成品φ8mm×1mm的加工率為95%,冷軋退火間的加工率為45%~65%。第2種工藝為將鈦棒下料、機(jī)加、擠壓得到φ24mm×φ15.5mm的管坯,再將經(jīng)過表面處理及酸洗后得到的φ24mm×4.25mm管坯進(jìn)行多道次冷軋至φ8mm×1mm,其中冷軋從φ24mm×4.25mm至成品φ8mm×1mm的加工率為90%,冷軋退火間的加工率在38%~40%。在軋制過程中根據(jù)退火之間的加工率對兩種管材進(jìn)行相應(yīng)的中間退火處理,最后再對兩種φ8mm×1mm的TA2管材成品在680℃保溫1h進(jìn)行成品退火處理。
對兩種加工工藝制備的φ8mm×1mm的TA2管材分別編號為1#、2#,并對其進(jìn)行性能測試。采用GX51倒置金相顯微鏡進(jìn)行金相組織觀察;采用INSTRON1185萬能材料試驗機(jī)進(jìn)行室溫拉伸性能測試;采用JL-WCS4管棒材超聲波檢測系統(tǒng)對管材缺陷幅值進(jìn)行檢測;采用WA-D600試驗機(jī)對管材進(jìn)行擴(kuò)口、壓扁、彎曲性能測試;采用WT40-7000管材水壓機(jī)進(jìn)行水壓測試。
2、試驗結(jié)果及討論
2.1金相組織
圖1為兩種加工工藝制備的管材冷軋加工態(tài)及退火態(tài)橫斷面金相組織照片。從圖1(a)、(b)中可以看出,兩種工藝得到的冷軋加工態(tài)組織,均未有明顯加工流線。由于軋制使管材變形量非常大,金屬流動充分[11],對比圖1(a)、(b)可看出,1#管材相較2#管材晶粒破碎更為充分,晶界也更為模糊,這是因為1#管材的加工率為95%,冷軋退火間的加工率在45%~65%,金屬流動性更充分,晶粒破碎也更為均勻,因此晶界相對模糊;2#管材冷軋加工率為90%,冷軋退火間的加工率在38%~40%,低于1#管材,晶界較為清晰,且組織內(nèi)部有條紋狀孿晶組織。
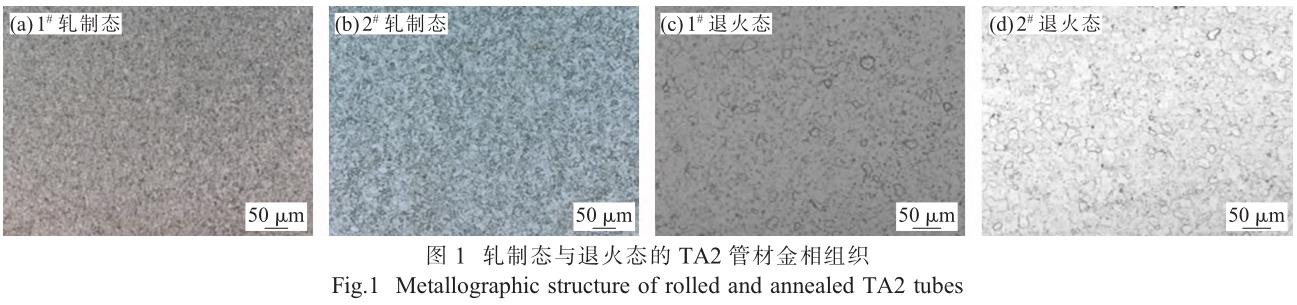
圖1(c)、(d)為兩種工藝管材退火態(tài)金相組織。由圖中可以看出,退火后加工態(tài)組織完全消失,晶粒完全再結(jié)晶并形成組織均勻的等軸晶,其中1#管材晶粒度為9.0級,2#管材晶粒度9.5級,退火后兩者晶粒度略有差異,但差別不大。
2.2室溫拉伸性能
兩種加工工藝制備的TA2管材室溫拉伸性能如圖2所示。從圖中可看出,無論管材是軋制態(tài)還是退火態(tài),1#管材抗拉強(qiáng)度、屈服強(qiáng)度均要明顯高于2#管材,伸長率則要低于2#管材的。經(jīng)過680℃退火后,兩者抗拉強(qiáng)度、屈服強(qiáng)度均有所降低,伸長率有所增加。計算得出,軋制態(tài)1#管材屈強(qiáng)比為0.92,2#管材屈強(qiáng)比0.90,兩者屈強(qiáng)比差距較小,經(jīng)退火后,1#管材屈強(qiáng)比降為0.73,2#管材屈強(qiáng)比降為0.66,兩者屈強(qiáng)比有一定差距。
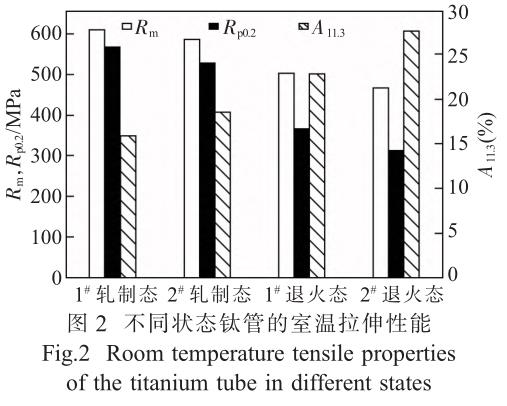
分析認(rèn)為,退火前,隨著冷軋變形量的增加,等軸狀的α晶粒受到擠壓,晶粒明顯碎化,位錯密度增加,金屬中的這種高密度位錯纏結(jié)在一起,增加了位錯運動的阻力,使位錯運動困難,需要增加外力來使位錯運動,因此管材抗拉強(qiáng)度增加[12]。由于1#管材加工率及退火之間的加工率均大于2#管材的,軋制后管材加工硬化程度也明顯更高,經(jīng)相同溫度退火,材料組織發(fā)生動態(tài)再結(jié)晶,消除了部分內(nèi)應(yīng)力,因此抗拉強(qiáng)度、屈服強(qiáng)度有所降低,伸長率升高。同時,2#管材加工硬化程度較低,退火后組織內(nèi)應(yīng)力釋放更加充分,晶粒更為均勻,因此屈強(qiáng)比下降程度較1#管材屈強(qiáng)比下降程度更大。綜合可以看出,適當(dāng)降低TA2管材冷軋加工率,有利于提高管材拉伸性能。
2.3超聲波探傷
圖3為兩種工藝鈦管超聲波探傷后的縱波曲線。對比可看出,2#管材波形曲線較1#管材曲線整體更為平緩,缺陷幅值上下波動也相對較小??梢缘贸?#鈦管質(zhì)量要明顯優(yōu)于1#管的。分析認(rèn)為,1#管材存在的微小缺陷要遠(yuǎn)遠(yuǎn)多于2#管材,這是因為1#管材在軋制過程中隨著加工道次增加,管材加工率也在增大,隨之管材加工硬化程度加深,盡管進(jìn)行了一定溫度的退火處理,但內(nèi)應(yīng)力及一些微小缺陷也無法完全消除,進(jìn)而可能造成管材存在許多肉眼無法觀察到的起皮、針孔、凹坑等缺陷。2#管材雖經(jīng)過多道次軋制后也存在一定加工硬化,但由于其加工率及道次間加工率較小,加工硬化程度較小,通過退火處理后內(nèi)應(yīng)力得到一定的釋放,因此管材質(zhì)量也相對更優(yōu)。
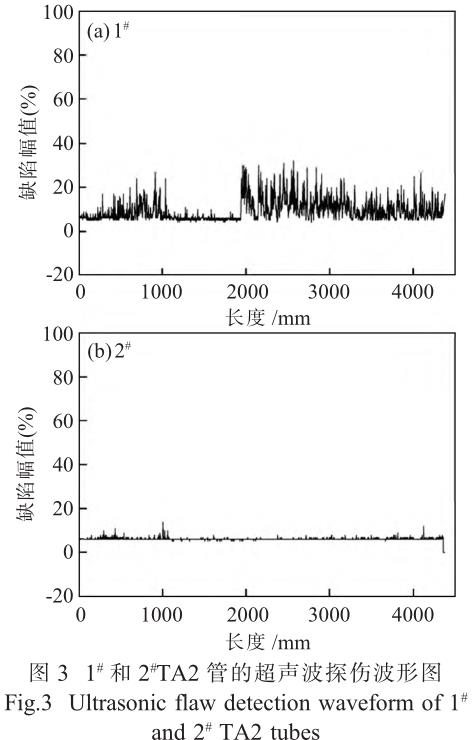
2.4其他力學(xué)性能
管材的其他力學(xué)性能還包括擴(kuò)口、壓扁、彎曲以及水壓測試等。表1為兩種不同工藝管材的其他相關(guān)力學(xué)性能測試結(jié)果。其中管材擴(kuò)口試驗的擴(kuò)口率均為30%,彎曲試驗壓頭尺寸均為4倍外徑尺寸,壓扁率為0.7,水壓測試要求打壓42MPa/5s。在以上相同測試條件下,兩種管材試樣均未發(fā)生開裂和水漏現(xiàn)象。但在壓扁試驗中,1#管材在內(nèi)壁6點(鐘)、12點(鐘)產(chǎn)生開裂,而2#管材未開裂。因此,第2種加工工藝制備的TA2管材較第1種加工工藝制備的管材性能更優(yōu)。
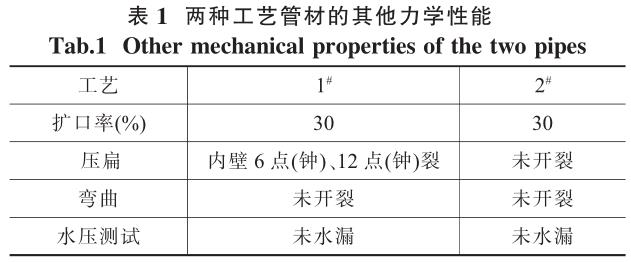
分析認(rèn)為,1#管材在壓扁試驗中內(nèi)壁6點、12點位置開裂,2#管材未開裂。這是因為1#管材冷軋加工率及道次加工率均大于2#管材,加工硬化程度更大,由于幾何學(xué)原因,1#管材在6點、12點位置較2#管材更易產(chǎn)生極高的應(yīng)力,從而導(dǎo)致內(nèi)壁開裂。
3、結(jié)論
(1)采用冷軋加工率90%,冷軋退火間的加工率在38%~40%工藝制得的φ8mm×1mm小口徑TA2管材較冷軋加工率95%,冷軋退火間的加工率在45%~65%工藝制得的同規(guī)格TA2管材的力學(xué)性能更優(yōu)。
(2)采用冷軋加工率90%,冷軋退火間的加工率在38%~40%工藝制得的TA2管退火后的晶粒組織更為均勻,超聲波探傷缺陷幅值波動更為平緩。
(3)在相同退火條件下,適當(dāng)降低TA2鈦管的冷軋加工率,減少管材因軋制而產(chǎn)生的加工硬化,有利于獲得具有良好質(zhì)量的小口徑TA2管。
參考文獻(xiàn):
[1]《稀有金屬材料加工手冊》編寫組.稀有金屬材料加工手冊[M].北京:冶金工業(yè)出版社,1984.
[2]Boyer R R.An overview on the use of titanium in the aerospace industry [J].Materials Science and Engineering A,1996,213(1/2):103-114.
[3]龐繼明,李明利,李明強(qiáng),等.退火溫度對 TA1 鈦管材組織和性能的影響[J].鈦工業(yè)進(jìn)展,2011,28(2):26-28.
[4]林永新.鈦及鈦合金管材生產(chǎn)技術(shù)現(xiàn)狀[J].稀有金屬快報,2005,24(2):1-2.
[5]邢 健 ,楊 英 麗 ,郭 荻 子 ,等.軋 制 及 軋 制 加 拉 拔 工 藝 制 備 的TA2 管材組織和性能[J].鈦工業(yè)進(jìn)展,2012,29(3):19-21.
[6]張凱悅,姚修楠,蔡文博,等.一種制備航天用高精度小口徑 TA2管材的方法:CN111496008A[P].2020-05-08 [2022-04-08].
[7]贠鵬飛,楊英麗,郭荻子,等.軋制 Q 值對小口徑 TA2 管材組織和性能的影響[J].鈦工業(yè)進(jìn)展,2012,29(2):24-27.
[8]邢健,巨建輝,楊英麗,等.TA2 管材織構(gòu)及性能研究[J].稀有金屬材料與工程,2013,42(8):81-85.
[9]尚笑宇,李壯,蔡一欽,等.冷軋變形量對 TA2 純鈦板材的組織和力學(xué)性能的影響[J].金屬加工(熱加工),2020(8):81-83.
[10]楊英麗,盧亞鋒,郭荻子,等.氧含量及軋制工藝對純鈦管材性能的影響[J].鈦工業(yè)進(jìn)展,2011,28(5):27-30.
[11]楊小玉.TA2 合金管材的織構(gòu)和承載性能研究 [J]. 鑄造技術(shù),2014,35(3):500-502.
[12]Parmar V,Changel A K,Srinivas B.Relationship between dislocation density and antibacterial activity of cryo-rolled and cold-rolledcopper[J].Materials,2019,12(2):1-11.
相關(guān)鏈接