序言
TC4鈦合金是一種α+β雙相鈦合金,其經(jīng)過熱處理后,具有高比強(qiáng)度、高比模量[1-2]。除此之外,還具備優(yōu)秀的耐熱性、耐蝕性以及可焊性,因此得到了航空航天制造領(lǐng)域的廣泛青睞[3-4]。目前,TC4鈦合金在飛機(jī)生產(chǎn)中主要用于制造飛機(jī)壁板等關(guān)鍵薄壁零部件[5]。激光焊接技術(shù)作為一種先進(jìn)連接技術(shù),由于其能量密度大、精度高等優(yōu)點(diǎn),在薄壁焊接構(gòu)件中獲得了廣泛的應(yīng)用[6-7]。然而,現(xiàn)有的航空航天復(fù)雜薄壁零件存在焊縫間隙均勻度低、裝配精度不足等問題[8-9],需依據(jù)不同的間隙將焊縫分為多段,并采用不同的焊接技術(shù)和標(biāo)準(zhǔn),導(dǎo)致焊縫數(shù)量急劇增加,生產(chǎn)效率下降的同時(shí),嚴(yán)重?fù)p害了焊接接頭的服役性能[10-11],因此深入研究不等間隙結(jié)構(gòu)自適應(yīng)激光焊接技術(shù)至關(guān)重要。通過調(diào)控工藝參數(shù)提升鈦合金結(jié)構(gòu)焊接質(zhì)量的研究較多,如劉黎明等[12]通過調(diào)制激光能量與電弧能量之間的配比,顯著提升了薄板結(jié)構(gòu)焊縫的表面成形;盧鳳桂等[13]通過改變激光焊接擺動(dòng)形式,在抑制飛濺的同時(shí),實(shí)現(xiàn)了焊接質(zhì)量的進(jìn)一步提升。然而隨焊接過程實(shí)時(shí)調(diào)控焊接功率以實(shí)現(xiàn)復(fù)雜難焊結(jié)構(gòu)的高精高質(zhì)量焊接仍是激光焊接廣泛應(yīng)用所面臨的難題之一,桂珍珍等[14]采用漸變功率的雙面激光焊接,實(shí)現(xiàn)了3-6mm變厚度TC4-BTi6431S異種鈦合金試板的可靠連接,張?chǎng)伍w等[15]通過對(duì)雙光束激光焊接的排布模式以及漸變功率進(jìn)行了比較及優(yōu)化,實(shí)現(xiàn)了不同厚度鈦合金板材的高質(zhì)量連接。本文基于航空復(fù)雜鈦合金不等間隙焊接組結(jié)構(gòu)的高效高質(zhì)量連接工藝需求,針對(duì)1.2mm薄板TC4鈦合金設(shè)計(jì)并開展了不等間隙自適應(yīng)激光焊接工藝與仿真研究?;谠囼?yàn)結(jié)果,建立了1.2mm厚TC4鈦合金不等間隙自適應(yīng)激光焊接過程三維瞬態(tài)熱流耦合模型,對(duì)焊接過程中的溫度場(chǎng)、流場(chǎng)分布進(jìn)行了數(shù)值模擬;探究了不同工藝參數(shù)條件下焊縫輪廓特征,并結(jié)合仿真結(jié)果研究了裝配間隙、激光功率密度變化對(duì)熔池形狀及流動(dòng)行為特征的影響,為不等間隙鈦合金薄板結(jié)構(gòu)的高效高質(zhì)量焊接提供了可靠手段。
1、自適應(yīng)激光焊接方法
試驗(yàn)選用TC4鈦合金作為母材金屬,板材尺寸為400mm×100mm×1.2mm,其合金成分及含量如表1所示。
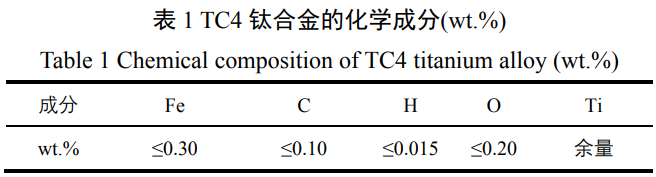
焊前2h內(nèi)用砂紙去除鈦板表面的氧化膜,再用丙酮擦洗,最后對(duì)表面進(jìn)行烘干處理以保持母材干燥。在激光不等間隙自適應(yīng)焊接實(shí)驗(yàn)中,激光發(fā)生器為德國(guó)通快公司生產(chǎn)的Trudisk-12003型光纖激光器,焊接機(jī)器人選用KR60HA型高精度焊接機(jī)器人;本實(shí)驗(yàn)過程中,被焊的1.2mm鈦合金板材由夾具夾緊,起始段焊縫間隙為0mm,終末段焊縫間隙為0.2mm,TC4鈦合金不等間隙自適應(yīng)激光焊接原理圖如圖1所示。
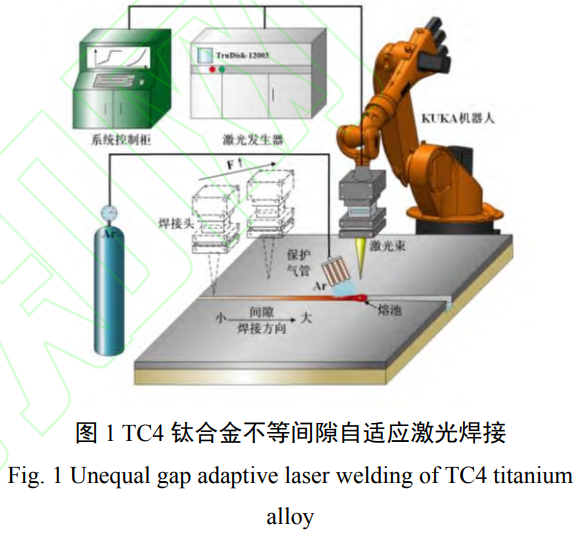
經(jīng)前期試驗(yàn)探索,厚度為1.2mm、間隙為0-0.2mm的鈦合金最優(yōu)工藝參數(shù)區(qū)間如表2所示,在焊前通過激光視覺設(shè)備獲取焊縫起始位置以及裝配間隙信息,并將數(shù)據(jù)反饋至激光焊接系統(tǒng)控制柜,控制柜確定焊接機(jī)器人起始點(diǎn)與終止點(diǎn),并基于間隙信息輸出適配的焊接工藝參數(shù)。在焊接開始后,隨著間隙的線性變化,實(shí)時(shí)調(diào)整激光功率及離焦量,最終優(yōu)質(zhì)高效地實(shí)現(xiàn)不等間隙激光焊接。
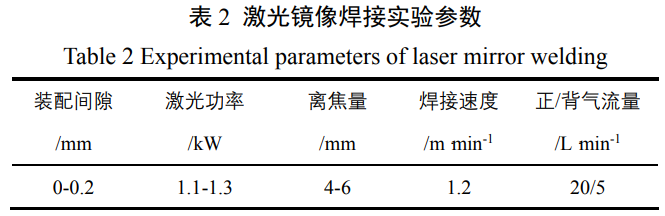
2、三維瞬態(tài)熱-流耦合模型建立
2.1幾何模型及網(wǎng)格劃分
建立的有限元模型如圖2所示,為兼顧計(jì)算精度及效率,對(duì)激光焊接作用區(qū)域的網(wǎng)格進(jìn)行了細(xì)化。整體網(wǎng)格模型中,最小單元邊長(zhǎng)為0.05mm,總體網(wǎng)格單元數(shù)量為514560。
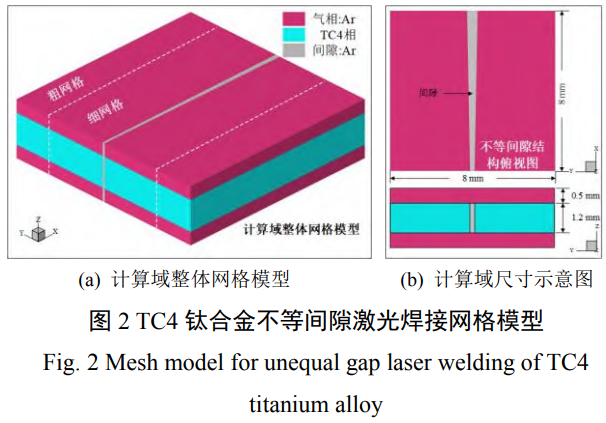
2.2控制方程
在TC4鈦合金不等間隙自適應(yīng)激光焊接過程中,熔池高溫液態(tài)金屬、金屬蒸氣流動(dòng)與傳熱行為中的所有物理量均遵循對(duì)應(yīng)的守恒原理,即質(zhì)量守恒方程、動(dòng)量守恒方程和能量守恒方程組成的三維控制方程組[16-17]。
(1)質(zhì)量守恒方程如下:

其中,ρ為材料密度,t為焊接時(shí)間,u、v、w分別為x、y、z方向的流體流速分量。
(2)動(dòng)量守恒方程如下:X軸方向:
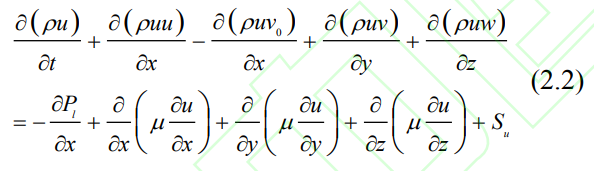
Y軸方向:
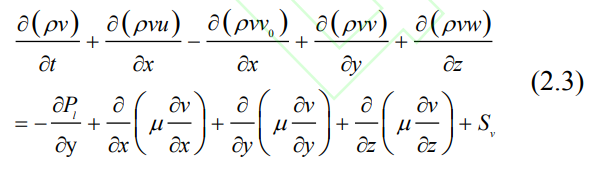
Z軸方向:
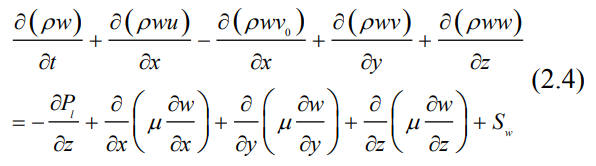
其中,P1為流體壓力,v0為焊接速度,μ為流體粘度,Su、Sv、Sw分別為x、y、z方向的動(dòng)量源項(xiàng)。
(3)能量守恒方程如下:
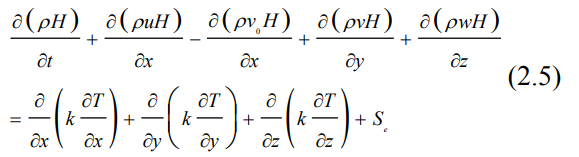
其中,k為材料熱導(dǎo)率,H為混合焓,Se為能量源項(xiàng),其表達(dá)式如下[17]:
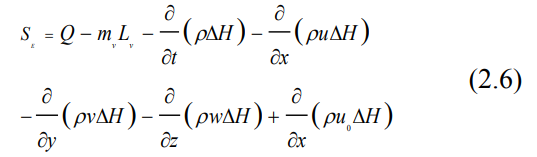
其中,Q為激光熱源能量,mv、Lv和△H分別表示單位體積的液相向氣相轉(zhuǎn)變時(shí)的質(zhì)量、蒸發(fā)潛熱和相變潛熱。
2.3激光焊接熱源模型
高斯熱源模型熱流呈高斯分布,即熱源中心熱流密度最高,隨著遠(yuǎn)離中心熱流密度迅速降低。該模型可用于模擬熱流密度集中的激光束熱源。高斯面熱源模型的熱流密度分布如下
式:
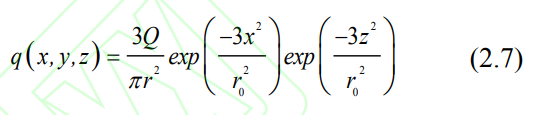
其中,x,y,z分別為三維空間內(nèi)的方向坐標(biāo),Q為激光熱源有效功率,r為高斯面熱源有效作用半徑。
高斯圓柱體熱源的熱流密度分布如下式:
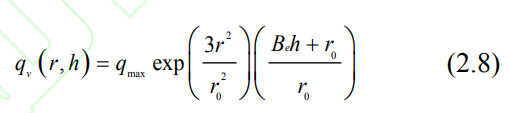
其中,qv為高斯圓柱體內(nèi)部熱流密度,其主要由距離中心點(diǎn)半徑r和到圓柱體熱源上界面的距離h決定,qmax為高斯圓柱體熱源中心的最大熱流密度,r0表示高斯圓柱體熱源作用的有效半徑,Be為圓柱熱源在z方向的線性衰減系數(shù)。
3、結(jié)果與討論
3.1不等間隙自適應(yīng)激光焊接熔池流動(dòng)行為研究
在TC4鈦合金不等間隙自適應(yīng)激光焊接過程中,由于激光能量密度和裝配間隙的實(shí)時(shí)變化,導(dǎo)致在焊接起始段與終末段分別存在X形和Y形兩種熔池形狀。圖3顯示了激光焊接起始段及終末段的焊接熔池形貌及模擬校核結(jié)果,比較兩者可以發(fā)現(xiàn)焊縫輪廓形狀及熔池表面輪廓的仿真結(jié)果與試驗(yàn)結(jié)果基本一致,兩者吻合良好。

為探究不等間隙自適應(yīng)激光焊接過程中熔池形狀的轉(zhuǎn)變過程及其影響因素,本研究對(duì)焊接過程中兩類形狀的熔池溫度場(chǎng)及流場(chǎng)分布進(jìn)行了分析。如圖4、5所示,在自適應(yīng)激光焊接前段,激光能量密度較高,表面金屬被逐層熔化、氣化,最終形成較深的匙孔。在反沖壓力的主導(dǎo)作用下,匙孔尖端附近的流體流速較快,最高可達(dá)1.468m.s-1,該處強(qiáng)烈的流體沖擊熔池底部,并且在表面張力的作用下由熔池中心向四周流動(dòng),最終在底部形成環(huán)流,形成X形熔池。
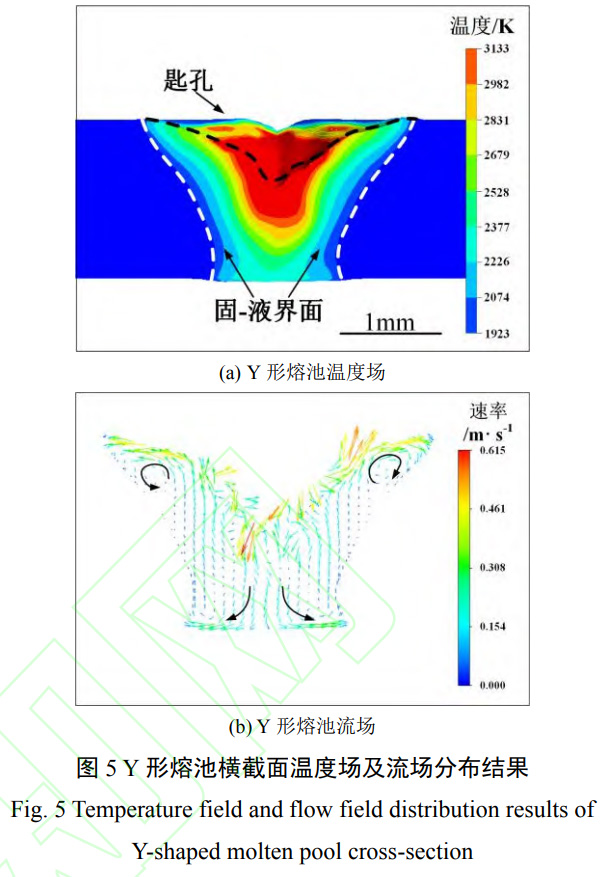
而隨著焊接過程的進(jìn)行,焊件間隙逐漸增大。盡管激光功率隨離焦量的變大由1。1kW提升至1.3kW,但是激光能量密度的下降導(dǎo)致匙孔深度逐漸減小,其尖端的流體速度也降低,最高0.615m.s-1,僅為上一階段的42%。由于流速的降低,匙孔尖端的流體不再具有對(duì)底部強(qiáng)烈的沖擊作用,僅在重力、反沖壓力以及熱浮力的共同作用下向熔池底部流動(dòng),雖有表面張力的作用使得底部熔池同樣往四周流動(dòng),但是由于流速較慢,無法形成穩(wěn)定持續(xù)的Marangoni環(huán)流,因而呈現(xiàn)Y形熔池。
兩種熔池形狀的流場(chǎng)分布對(duì)比如圖6、7所示。對(duì)比兩者流場(chǎng)分布可以看出,X形熔池內(nèi)熔融金屬最大流速可達(dá)1.474m.s-1,而Y形熔池內(nèi)最大流速僅為0.878m.s-1,這種流速的差異導(dǎo)致了匙孔尖端下方熔融金屬的流動(dòng)行為的不同。對(duì)于X形熔池,高速向下的熔融金屬可以快速到達(dá)熔池底部并且在表面張力的作用下往熔池前沿和后端流動(dòng),形成渦流。與此同時(shí),熔池上表面流體在表面張力和反沖壓力的共同作用下也在熔池上方形成渦流,上下熔池的渦流最終又在熔池中部匯集。而對(duì)于Y形熔池,由于不具備大量高速向下的高能流體,無法在熔池底部產(chǎn)生渦流,底部熔池的流動(dòng)狀態(tài)也較為平緩,但上表面熔池依舊受反沖壓力與表面張力的共同作用,最終熔池內(nèi)熔融金屬由熔池頂部后端向底部前沿緩慢流動(dòng)。
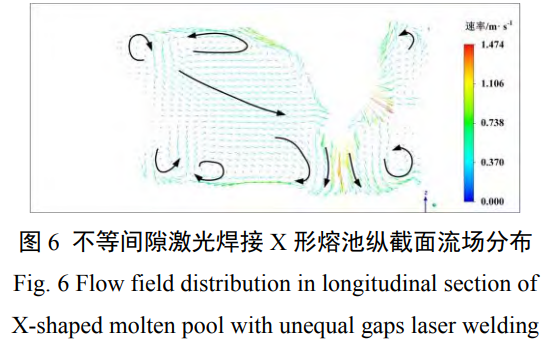
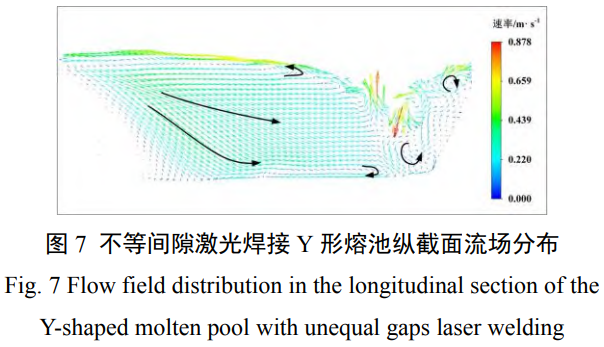
3.2不等間隙自適應(yīng)激光焊接匙孔演變過程研究
圖8、9所示為兩種類型熔池內(nèi)匙孔形態(tài)及匙孔壁面流體流動(dòng)行為分布結(jié)果??梢钥闯觯琗形熔池對(duì)應(yīng)的匙孔形態(tài)表現(xiàn)為長(zhǎng)錐形,同時(shí)存在匙孔開口,而Y形熔池對(duì)應(yīng)的匙孔形態(tài)則是呈現(xiàn)扁平的陀螺形,但匙孔開口面積更大。對(duì)匙孔壁面上的流體進(jìn)行分析,可以看出,不論哪種形態(tài)的匙孔,其高速流體均出現(xiàn)在匙孔尖端,但流速差異較大,前者可達(dá)1.858m.s-1,而后者僅為前者的57%,為1.056m.s-1。在長(zhǎng)錐形匙孔壁面上,以匙孔中部為分界存在著三種流向不同的流體,在匙孔上部,流體沿著匙孔壁向上流動(dòng),平均流速在0.973m.s-1左右,而在匙孔中部,存在著繞匙孔壁流動(dòng)的流體,其平均流速較小,在0.530m.s-1左右,匙孔底部則是沿匙孔壁向下的流體,是匙孔壁上的高速流體區(qū)域,均速在1.416m.s-1左右。對(duì)于陀螺形匙孔,其壁面上幾乎只存在沿壁面向上的流體,其平均流速也只有0.670m.s-1,僅在匙孔尖端部分存在少量向下流體。
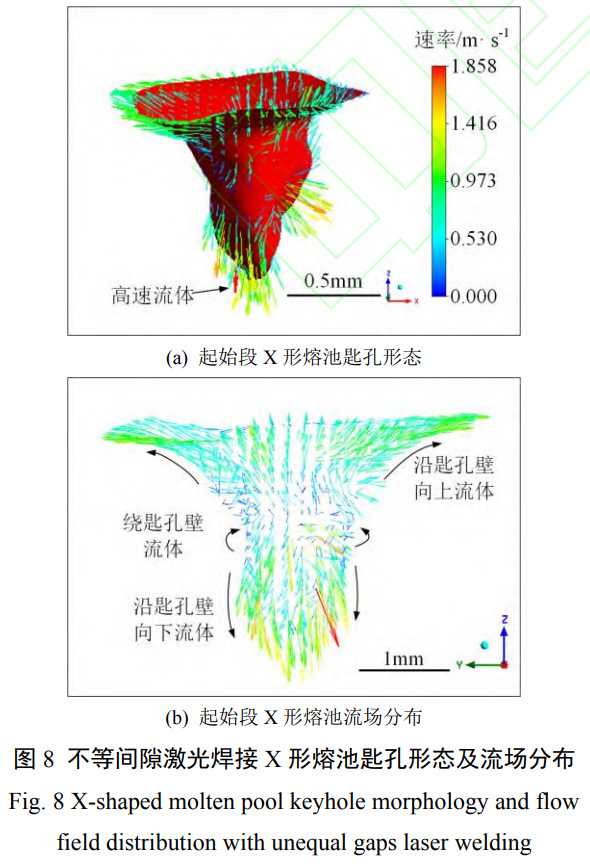
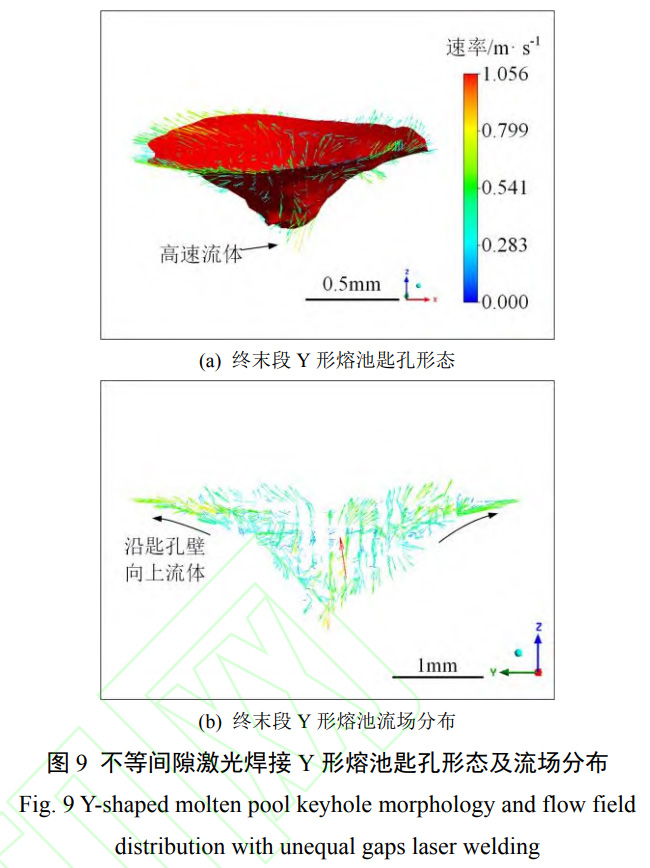
針對(duì)不等間隙自適應(yīng)激光焊接過程匙孔形態(tài)及局部區(qū)域受力演變行為進(jìn)行分析。首先對(duì)點(diǎn)1的受力情況變化進(jìn)行分析,由于點(diǎn)1位于熔池上表面,受激光束的直接照射而具有極高溫度,因此反沖壓力較大,點(diǎn)1在平衡狀態(tài)下的受力關(guān)系可描述為:

式中,G為重力,F(xiàn)s為界面表面張力,Pv為反沖壓力,Pm和Fv分別為熔池流體靜壓力和流體動(dòng)壓力,F(xiàn)f為蒸氣-金屬摩擦力。由于匙孔壁對(duì)激光能量的菲涅爾吸收效應(yīng)以及等離子體對(duì)激光能量的逆韌致吸收[18-19],匙孔尖端處也具有極高的溫度,從而存在較大的反沖壓力。位于匙孔壁尖端的點(diǎn)2處的受力關(guān)系可表述為:

但由于激光能量密度在時(shí)刻減小,匙孔壁的溫度也會(huì)隨之降低,反沖壓力減小的同時(shí),匙孔壁的平衡狀態(tài)遭到破壞,匙孔壁點(diǎn)1處附近的熔融金屬將被向上推動(dòng),使得匙孔孔徑減小,匙孔壁曲率減小,但由于光斑半徑以及裝配間隙的增大,表面熔池變得更寬,并且因?yàn)殚g隙增大,使得其對(duì)填充金屬的需求量增多而在熔池表面產(chǎn)生凹陷,匙孔的開口在這兩者的共同作用下反而有所增大。匙孔尖端則由于反沖壓力的減小而縮短。此刻點(diǎn)1處的受力情況如圖10(b)所示,其受力關(guān)系可描述為:

點(diǎn)2處合力的最終效果是使得匙孔縮短。其瞬間狀態(tài)下受力關(guān)系可表述為:

綜上可知,隨著激光功率密度的減小和裝配間隙的增大,匙孔壁的力學(xué)作用始終處于動(dòng)態(tài)變化過程中,匙孔形態(tài)由最初的長(zhǎng)錐形逐漸縮小拓寬,最終呈現(xiàn)為開口較大,深度較小的陀螺形。
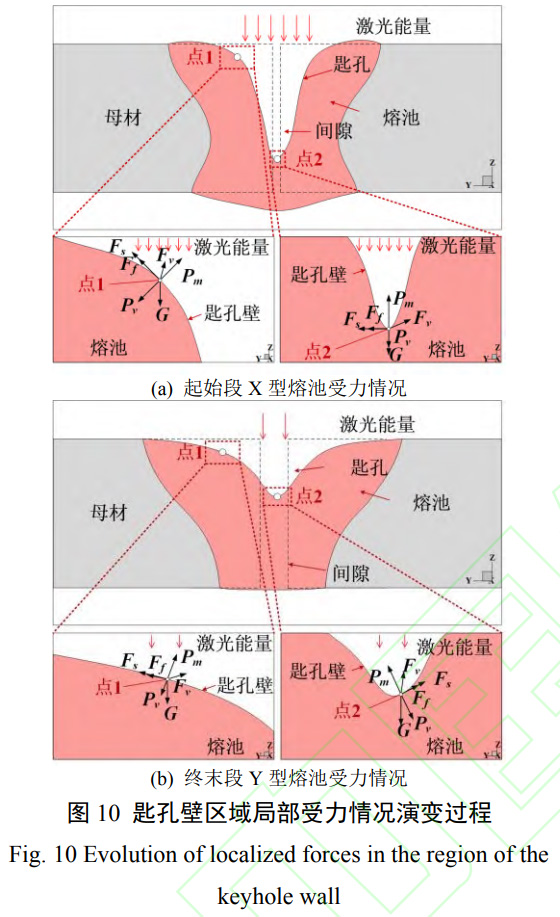
3.3熔池流動(dòng)行為對(duì)焊縫輪廓形狀均勻性的影響規(guī)律研究
從前述受力關(guān)系可知,表面張力與反沖壓力時(shí)熔池流動(dòng)的主要驅(qū)動(dòng)力,其在大小及方向上的動(dòng)態(tài)變化將會(huì)對(duì)熔池流動(dòng)行為產(chǎn)生顯著影響,其中匙孔內(nèi)壁表面張力與溫度的經(jīng)驗(yàn)公式如下所示:

式中,γ0為材料熔點(diǎn)下的表面張力,T為該點(diǎn)溫度,Tm為材料熔點(diǎn)溫度。
匙孔內(nèi)壁反沖壓力與溫度的經(jīng)驗(yàn)公式如下:

式中,P0為材料沸點(diǎn)下的反沖壓力,Lv為材料的汽化潛熱,T為該點(diǎn)溫度,Tg為材料沸點(diǎn)溫度,kB為玻爾茲曼常數(shù)。
圖11解釋了匙孔動(dòng)態(tài)變化過程對(duì)熔池流動(dòng)行為的影響,進(jìn)而揭示了TC4鈦合金不等間隙自適應(yīng)激光焊接過程熔池流動(dòng)特性對(duì)焊縫輪廓形狀均勻性的影響規(guī)律。對(duì)于熔池上表面及其附近區(qū)域,無論在哪個(gè)階段,其內(nèi)部流體流動(dòng)均受表面張力與反沖壓力的共同驅(qū)動(dòng),表面張力主導(dǎo)該區(qū)域流體流動(dòng)方向并加速流體流動(dòng),反沖壓力則是提供更強(qiáng)的流動(dòng)驅(qū)動(dòng)力,很大程度上增大該區(qū)域流體流速。在熔池上表面附近區(qū)域,由于存在較大的溫度梯度,熔池在表面張力的驅(qū)動(dòng)下由中心高溫處向四周低溫處流動(dòng),該區(qū)域擁有較大流速進(jìn)而形成Marangoni環(huán)流,同時(shí),匙孔壁面屬于高溫區(qū)域因而對(duì)附近熔池內(nèi)流體施加了強(qiáng)大的反沖壓力,在表面張力與反沖壓力的共同作用下,在熔池上表面區(qū)域形成高速的Marangoni環(huán)流。隨著激光功率密度的減小,匙孔壁面溫度降低,對(duì)該區(qū)域熔池內(nèi)流體施加的反沖壓力也就減弱,流體流速減緩,但熔池流動(dòng)方向未發(fā)生改變,最終形成低速低能的Marangoni環(huán)流。
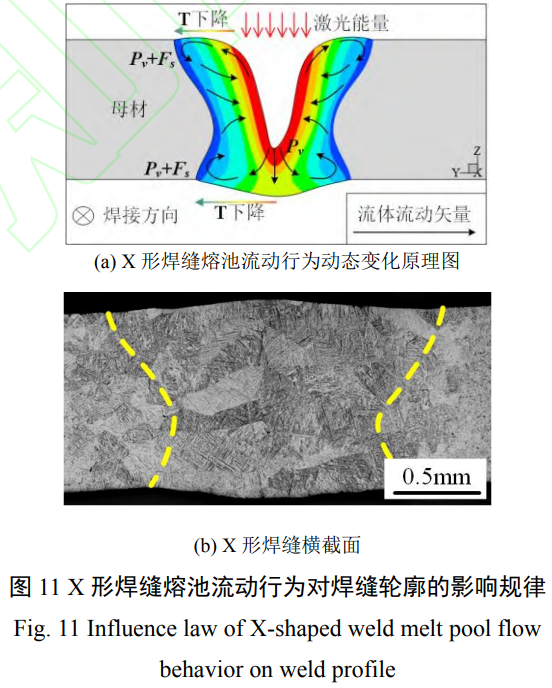
不同于熔池上表面,隨著焊接過程的進(jìn)行,熔池底部的流動(dòng)行為開始有所不同。當(dāng)激光能量密度較高時(shí),匙孔尖端對(duì)熔池底部流體施加了較強(qiáng)的反沖壓力,此時(shí)該區(qū)域熔池流動(dòng)由反沖壓力主導(dǎo),高能高速流體向下沖擊,使得熔池底部產(chǎn)生下榻,如圖11(a)所示。流體以高速狀態(tài)到達(dá)熔池下表面后,受表面張力的驅(qū)動(dòng)又向四周高速流動(dòng),最終在熔池底部也形成了由反沖壓力和表面張力共同驅(qū)動(dòng)的高能高速M(fèi)arangoni環(huán)流。此外,由于流速較快,上半部熔池內(nèi)流體大部分參與環(huán)流運(yùn)動(dòng),還有一部分則分流向熔池中部流去,下半部熔池同樣如此,一小部分流體脫離環(huán)流向上往熔池中部流動(dòng),最終在熔池中部形成如圖8所示的繞匙孔壁流體。當(dāng)熔池冷卻凝固后,就形成了如圖11(b)所示的X形焊縫。
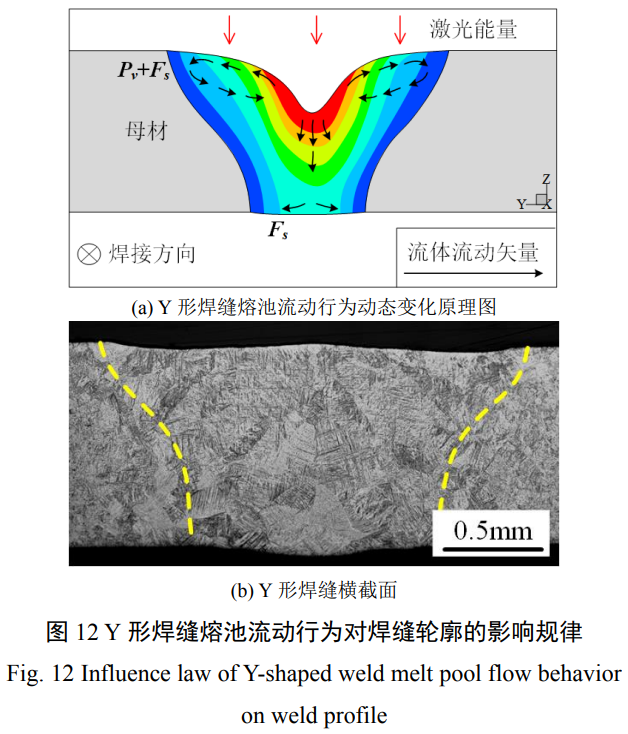
而當(dāng)激光功率密度下降時(shí),匙孔尖端所施加的反沖壓力已不足以驅(qū)動(dòng)該處流體向熔池底部沖擊,流體不再具備高能高速的特性,同時(shí),熔池下表面的溫度梯度也不足以提供較大表面張力梯度,因此此時(shí)的熔池?zé)o法在底部形成Marangoni環(huán)流,最終凝固成為如圖12(b)所示的Y形焊縫。綜上所述,在TC4鈦合金不等間隙自適應(yīng)激光焊接過程中,為兼容線性增大的裝配間隙,激光光斑半徑需要相適配的增大,同時(shí)又要保證焊件的焊接質(zhì)量,不能出現(xiàn)未焊透或者焊穿等嚴(yán)重缺陷,因此在實(shí)際焊接過程中激光功率密度是呈減小趨勢(shì)的,激光功率密度改變破壞了匙孔壁面上的平衡受力關(guān)系,使其力學(xué)條件隨時(shí)處于新的動(dòng)態(tài)變化中,這就導(dǎo)致了匙孔形態(tài)的動(dòng)態(tài)變化,進(jìn)一步影響了熔池流動(dòng)行為,最終造成了TC4鈦合金不等間隙自適應(yīng)激光焊接過程焊縫輪廓形狀的顯著差異。
4、結(jié)論
(1)在TC4鈦合金不等間隙自適應(yīng)激光焊接過程中,存在長(zhǎng)錐形和陀螺形兩種匙孔形態(tài)。在長(zhǎng)錐形匙孔作用的熔池區(qū)域,其上下表面附近存在兩股環(huán)流,上表面是主要由表面張力驅(qū)動(dòng)的Marangoni環(huán)流,下表面則由反沖壓力主導(dǎo),表面張力共同驅(qū)動(dòng)的環(huán)流。而陀螺形匙孔作用的熔池區(qū)域則不存在下表面環(huán)流。
(2)TC4不等間隙自適應(yīng)激光焊接過程焊縫輪廓形狀差異與熔池內(nèi)流體流動(dòng)行為及匙孔動(dòng)態(tài)行為密切相關(guān)。隨焊接間隙增大,所需的光斑半徑擴(kuò)大,作用于熔池的激光功率密度快速下降,減小熔池內(nèi)反沖壓力的同時(shí)抑制了熔池內(nèi)流體的高速流動(dòng),使得熔池由X形向Y形演變。
參考文獻(xiàn)
[1] 賈晨鵬, 黃一鳴, 趙圣斌, 等. TC4 鈦合金激光深熔焊等離子體羽流熱力學(xué)行為研究[J]. 中國(guó)激光, 2023, 50(20): 67-73.
[2] Ma Chao, Li Yue, Cheng Lihong, et al. Numerical analysis of gravity-induced coupling dynamics of keyhole and molten pool in laser welding[J]. International Journal of Thermal Sciences, 2024, 201, 108987.
[3] Yan Tingyan, Liu Yuan, Wang Jianfeng, et al. Bridging microstructure and crystallography with the crack propagation behavior in Ti-6Al-4V alloy fabricated via dual laser beam bilateral synchronous welding[J]. Journal of Materials Science & Technology, 2024, 1741-14.
[4] 成奇, 郭寧, 張迪, 等. NiTi 形狀記憶合金與異種材料激光焊接研 究進(jìn)展[J]. 機(jī)械工程學(xué)報(bào), 2023, 59(16): 182-191.
[5] 鄒武裝. 鈦及鈦合金在航天工業(yè)的應(yīng)用及展望[J]. 中國(guó)有色金屬, 2016(01): 70-71.
[6] 張健, 楊銳. 激光焊接鈦合金薄板時(shí)的功率控制[J]. 中國(guó)激光, 2012, 39(01): 77-80.
[7] James D C, Larry P C, Henry R P. Titanium alloys on the F-22 fighter airframe[J]. Advanced Materials and Processes, 2002, 160(5): 25-28.
[8] 葉澤濤, 李悅, 馬龍飛, 等. 液氮冷卻對(duì)TC4鈦合金激光焊接微觀 組織、殘余應(yīng)力與變形的影響[J]. 電焊機(jī), 2023, 53(07): 60-66.
[9] 顧俊, 劉釗鵬, 徐友鈞, 等. 鈦合金及其激光加工技術(shù)在航空制造中的應(yīng)用[J]. 應(yīng)用激光, 2020, 40(03): 547-555.
[10] Wen Peng, Yelkenci D, Chen Junhong, et al. Numerical analysis of the effect of welding positions on formation quality during laser welding of TC4 titanium alloy parts in aerospace industry[J]. Journal of Laser Application, 2019, 31(2): 022401.
[11] 高向東, 馮燕柱, 桂曉燕, 等. 激光入射角影響焊接熔池匙孔瞬態(tài) 行為數(shù)值模擬[J]. 機(jī)械工程學(xué)報(bào), 2020, 56(22): 82-89.
[12] 劉黎明, 史吉鵬, 王紅陽. 低功率激光誘導(dǎo)電弧復(fù)合焊接鈦合金 薄板工藝研究[J]. 機(jī)械工程學(xué)報(bào), 2016, 52(18): 38-43+50.
[13] Hao Yu, Li Liqun, Sun Yu, et al. Dynamic behavior of keyhole and molten pool under different oscillation paths for galvanized steel laser welding[J]. International Journal of Heat and Mass Transfer, 2022, 192: 122947.
[14] 桂珍珍. 變厚度 TC4-BTi6431S 鈦合金激光雙面焊接工藝基礎(chǔ)研 究[D]. 武漢: 華中科技大學(xué), 2014.
[15] Zhang Xinge, Li Liqun, Chen Yanbin, et al. Numerical Simulation Analysis of Dual-Beam Laser Welding of Tailored Blanks with Different Thicknesses[J]. Metals, 2019, 9(2): 135.
[16] 汪任憑. 激光深熔焊接過程傳輸現(xiàn)象的數(shù)值模擬[D]. 北京: 北京工業(yè)大學(xué), 2011.
[17] 陳帥. 2219 鋁合金雙激光束雙側(cè)同步焊接過程熔池特性研究[D]. 南京: 南京航空航天大學(xué), 2021.
[18] Ai Yuewei, Jiang Ping, Wang Chunming, et al. Experimental and numerical analysis of molten pool and keyhole profile during high-power deep-penetration laser welding[J]. International Journal of Heat and Mass Transfer, 2018, 126: 779-789.
[19] 彭南翔. 激光深熔焊接鋁合金孔內(nèi)菲涅爾吸收研究[D]. 長(zhǎng)沙: 湖南大學(xué), 2018.
第一作者:馬超,男,博士研究生.主要從事激光焊接相關(guān) 研究工作.Email: machaonuaa@163.com
通信作者:占小紅,男,博士,教授,博士生導(dǎo)師,主要從事激光加工、增材制造、焊接與先進(jìn)連接技術(shù)與裝備,以及材料加工工藝建模與仿真等方面的教研工作.E-mail:xiaohongzhan_nuaa@126.com
相關(guān)鏈接