引言
海洋既是資源開(kāi)發(fā)的重要基地,又是國(guó)土安全的重要屏障。我國(guó)海岸線長(zhǎng)18000多km,可管轄的海域面積達(dá)300萬(wàn)km2,擁有豐富的油、氣資源,礦產(chǎn)資源和生物資源。水下裝備是一類可輔助或替代人類在復(fù)雜、高危的水下特殊環(huán)境中進(jìn)行作業(yè)的工具,主要包括水中兵器、水下運(yùn)載工具和深海空間站,是海洋資源開(kāi)發(fā)和海洋權(quán)益維護(hù)不可或缺的關(guān)鍵元素。水下裝備最早由鐵基材料制成,后為適應(yīng)裝備輕量化的需要改用鋁合金材料。隨著我國(guó)海洋強(qiáng)國(guó)戰(zhàn)略的確立,要求國(guó)家海洋力量的覆蓋從近海、淺海拓展到遠(yuǎn)海、深海。相應(yīng)地,水下裝備必然要滿足遠(yuǎn)航程、長(zhǎng)航時(shí)、大水深的作業(yè)需求,因此水下裝備用結(jié)構(gòu)材料開(kāi)始呈現(xiàn)出全鈦合金化的趨勢(shì),這主要?dú)w因于鈦合金的輕質(zhì)、高強(qiáng)、耐蝕、無(wú)磁等優(yōu)異特性[1-3]。
但是,鈦合金的屈強(qiáng)比大(抗拉強(qiáng)度/屈服強(qiáng)度,約為碳鋼的2倍),熱導(dǎo)率低(平均8W/m.K,約為Fe的1/5),彈性模量小(平均110GPa,約為Fe的1/2),對(duì)H、O、N極度敏感(平均300℃以上快速吸氫、平均450℃以上快速吸氧、平均600℃以上快速吸氮)[4-6],因此相對(duì)于鐵基材料和鋁合金而言,鈦合金產(chǎn)品的加工難度大:在冷加工中表現(xiàn)為材料回彈大、刀具磨損快、材料利用率低,在熱加工中表現(xiàn)為氧化嚴(yán)重、脆化傾向明顯,最終將導(dǎo)致鈦合金產(chǎn)品的尺寸精度差、加工周期長(zhǎng)、批量穩(wěn)定性不足和加工成本高的問(wèn)題[7-8]。此外,隨著水下裝備作業(yè)深度的提高,所用材料厚度急劇增加,隨之帶來(lái)的超規(guī)格鈦合金原材料的制備也是關(guān)鍵技術(shù)瓶頸。
一代裝備牽引一代材料,一代技術(shù)造就一代裝備。水下裝備的快速發(fā)展對(duì)傳統(tǒng)制造技術(shù)提出了嚴(yán)峻挑戰(zhàn),同時(shí)也為增材制造(AdditiveManufactur‐ing,AM)技術(shù)提供了應(yīng)用空間。AM的思想起源于19世紀(jì)末的美國(guó),在20世紀(jì)80年代才得以快速發(fā)展,其發(fā)展的基礎(chǔ)是高能量熱熔覆技術(shù)和快速成形技術(shù)。有別于傳統(tǒng)冷加工的減材制造技術(shù)(車、銑、刨、磨、鉆等)和傳統(tǒng)熱加工的等材制造技術(shù)(鑄、鍛、焊等),AM是根據(jù)所設(shè)計(jì)的三維模型,通過(guò)分層處理,利用激光、電子束或電弧為熱源將粉末或絲材進(jìn)行熔化,采用逐層堆積的方式直接實(shí)現(xiàn)零部件的整體成形[9-11]。因此,對(duì)于水下裝備而言,增材制造技術(shù)的引入不僅可以完美避開(kāi)超規(guī)格原材料制備的技術(shù)瓶頸和解決鈦合金傳統(tǒng)加工方式帶來(lái)的質(zhì)量難題,還能為裝備的結(jié)構(gòu)設(shè)計(jì)提供更大的自由度。
由此可見(jiàn),增材制造技術(shù)在水下裝備的建造中有極為廣泛的應(yīng)用前景。然而,任何一項(xiàng)技術(shù)的應(yīng)用,不僅取決于現(xiàn)實(shí)需求,還決定于技術(shù)對(duì)產(chǎn)品的適應(yīng)性和對(duì)潛在風(fēng)險(xiǎn)的考慮。
1、增材制造技術(shù)在鈦合金水下裝備上的適用性分析
鈦合金在增材制造方面最受關(guān)注,也是目前增材制造研究與應(yīng)用最為成熟的材料體系之一,能夠適應(yīng)各種增材制造方法,從以粉末為原料的如激光選區(qū)熔化(selectedlasermelting,SLM)[12-13]和激光熔融沉積(lasermeltingdeposition,LMD)[14-15],到以線材或絲材為原料的弧絲增材制造(wire-arcaddi‐tivemanufacturing,WAAM)[16]技術(shù),其原理如圖1所示[17-18]。
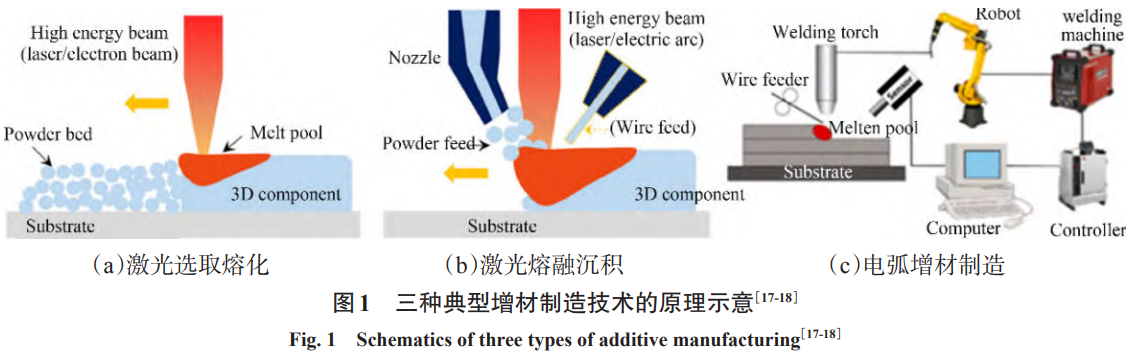
1.1增材制造技術(shù)對(duì)幾何尺寸的適應(yīng)性
成形零件的尺寸是決定增材制造技術(shù)在水下裝備中應(yīng)用的首要因素。增材制造成形零件的幾何尺寸受成形原理的影響較大。對(duì)于SLM技術(shù)而言,由于成形是在真空艙室內(nèi)完成,因而艙室的空間決定了零件的最大成形尺寸。而對(duì)于LMD和WAAM而言,零件成形尺寸無(wú)太多限制,可以打印尺寸數(shù)米長(zhǎng)的零件,可以覆蓋水下裝備90%以上的零部件[19]。盡管其成形零件的尺寸精度和表面粗糙度較SLM技術(shù)差距較大,但通過(guò)后續(xù)的精加工,完全可以滿足裝備的使用要求。
目前,國(guó)外SLM設(shè)備制造商有德國(guó)EOS(Elec‐troOpticalSystems)公司、德國(guó)ConceptLaser公司、德國(guó)SLMSolutions公司、德國(guó)Trumpf公司、美國(guó)3DSystems公司、英國(guó)Renishaw、荷蘭AdditiveIn‐dustries,可見(jiàn)德國(guó)產(chǎn)品居多,并占據(jù)了全球大部分份額。國(guó)內(nèi),以西安鉑力特、長(zhǎng)沙華曙高科和北京易加三維等為代表的企業(yè),和以西北工業(yè)大學(xué)、北京航空航天大學(xué)和華中科技大學(xué)為代表的高校,都相繼研發(fā)出了擁有自主知識(shí)產(chǎn)權(quán)的SLM設(shè)備,并在全球市場(chǎng)中開(kāi)始嶄露頭角。表1給出了以上十家公司SLM設(shè)備最大成形尺寸的調(diào)研結(jié)果。
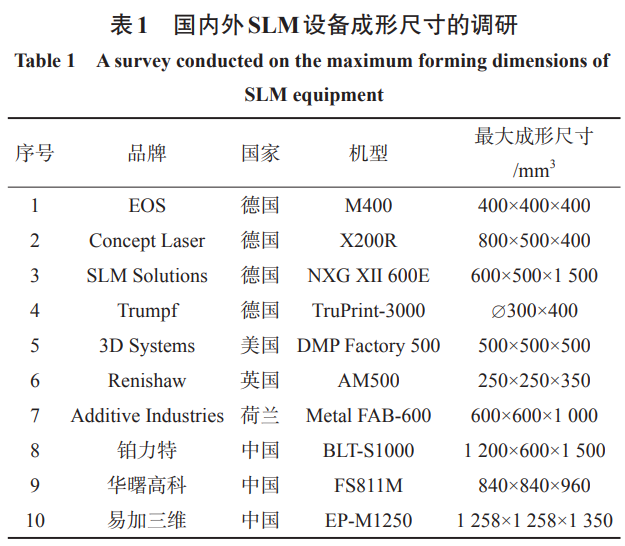
從表1可知,并且隨著成形尺寸的增大,設(shè)備的成本急劇提高。水下裝備的零部件尺寸范圍很廣,并且建造方案的優(yōu)化也可實(shí)現(xiàn)對(duì)大型部件的拆解。因此,從產(chǎn)品的尺寸而言,SLM也能覆蓋水下裝備60%以上的零部件。
1.2增材制造技術(shù)對(duì)產(chǎn)品結(jié)構(gòu)的適應(yīng)性
航空航天領(lǐng)域?qū)︼w行器部件輕量化的要求較為嚴(yán)苛,因此常采用復(fù)雜的鏤空結(jié)構(gòu)實(shí)現(xiàn)結(jié)構(gòu)的減重。得益于增材制造技術(shù)在復(fù)雜形狀成形上的獨(dú)特優(yōu)勢(shì),它能在航空航天領(lǐng)域迅速取得應(yīng)用。盡管水下裝備也有輕量化的要求,但由于作業(yè)環(huán)境的差異,一般不使用鏤空結(jié)構(gòu),因而它的結(jié)構(gòu)復(fù)雜性相對(duì)較低。從增材制造技術(shù)表現(xiàn)出的成形能力來(lái)看,完全能夠勝任水下裝備的結(jié)構(gòu)復(fù)雜性。下文以水下裝備的兩個(gè)典型零件為例,具體分析增材制造技術(shù)在水下裝備建造中的優(yōu)勢(shì)。
(1)螺旋槳。
螺旋槳是水下裝備的關(guān)鍵推進(jìn)裝置,一般采用鑄造和機(jī)械加工完成。但對(duì)于鈦合金鑄造螺旋槳而言,過(guò)高的制造成本和繁瑣的工藝是目前普遍面臨的困境,這是因?yàn)椋孩僭阼T造過(guò)程中需要控制鑄造溫度和氣氛(以真空為宜),以防止氧化、氮化和碳化等不良反應(yīng),保證鑄件質(zhì)量;②鑄造模具應(yīng)優(yōu)選陶瓷或石墨(或涂層)等具有高溫耐磨、耐腐蝕和熱震穩(wěn)定等特性的材料,以確保鑄件的質(zhì)量;③鈦合金的流動(dòng)性和充型性較差,鑄件容易出現(xiàn)縮松問(wèn)題,因此需要對(duì)鑄件進(jìn)行真空熱等靜壓處理[20-21]。因此,對(duì)于批量小的螺旋槳,采用厚板機(jī)械加工的方式更加便捷,但也不得不接受材料利用率極低(20%~30%)的問(wèn)題。
據(jù)報(bào)道,Damen集團(tuán)、德國(guó)螺旋槳制造商Pro‐marin、軟件供應(yīng)商Autodesk和鹿特丹增材制造實(shí)驗(yàn)室(RAMLAB)于2017年合作完成了世界上首個(gè)弧絲增材制造三葉鎳鋁青銅合金螺旋槳(直徑1.35m、重量400kg),通過(guò)了相關(guān)的性能測(cè)試,并獲得了法國(guó)船級(jí)社的認(rèn)證[22]。
近日,中國(guó)船舶集團(tuán)汾西重工有限責(zé)任公司聯(lián)合西安鉑力特采用LMD技術(shù)完成了七葉鈦合金螺旋槳(直徑800mm,重量30kg)的試制,如圖2所示,正在申請(qǐng)中國(guó)船級(jí)社的認(rèn)證。
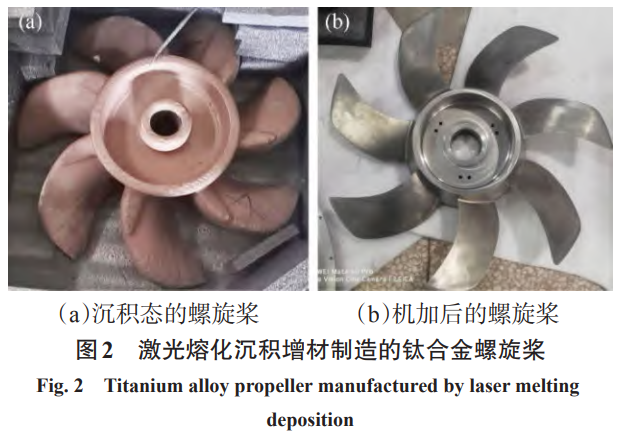
(2)空心殼體。
空心殼體是水下裝備中加工難度最大的部件之一,一般是通過(guò)鍛環(huán)拼焊的方式完成,裝配難度大,焊縫數(shù)量多,焊接變形大,材料利用率低,加工周期長(zhǎng)。近日,中國(guó)船舶集團(tuán)汾西重工聯(lián)合西安鉑力特完成了空心殼體的LMD試制,如圖3所示,制件順利通過(guò)了力學(xué)性能測(cè)試和外水壓測(cè)試。與傳統(tǒng)加工方式對(duì)比,材料利用率由50%提高至95%,加工周期由7天縮短到1天,制造成本降低了20%。
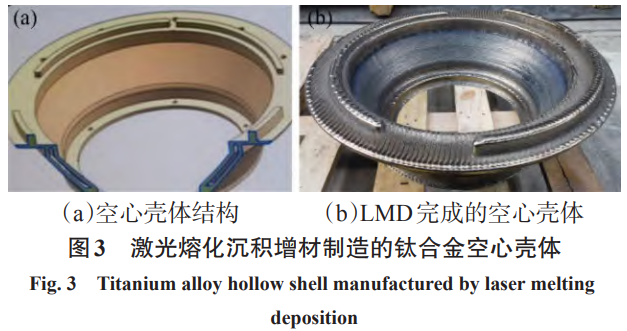
(3)壓力容器。
在國(guó)外,Breddermann及其團(tuán)隊(duì)通過(guò)LMD技術(shù)成功制備了TC4鈦合金半球殼體,如圖4所示[23]。并對(duì)其進(jìn)行了細(xì)致的評(píng)估與測(cè)試,以探索其在水下裝備中的應(yīng)用潛力。這項(xiàng)研究揭示了AM過(guò)程中為確保壓力外殼的可靠性,必須保證材料屬性的一致性、尺寸精度和表面質(zhì)量達(dá)到設(shè)計(jì)要求。盡管鈦合金半球體在表面質(zhì)量、壁厚一致性以及內(nèi)部孔洞率方面存在挑戰(zhàn),但通過(guò)優(yōu)化構(gòu)建方向和引入支撐結(jié)構(gòu),第二批半球體在尺寸精度上取得了顯著進(jìn)步。此外,進(jìn)行的破壞測(cè)試表明,第一批半球體在6.2~6.9MPa的壓力下開(kāi)始屈曲,并在約7.1MPa時(shí)發(fā)生破壞,而第二批的一個(gè)半球體承受壓力達(dá)29.8MPa才發(fā)生破壞,這一結(jié)果對(duì)于水下鈦合金裝備的未來(lái)發(fā)展具有重要的啟示作用。
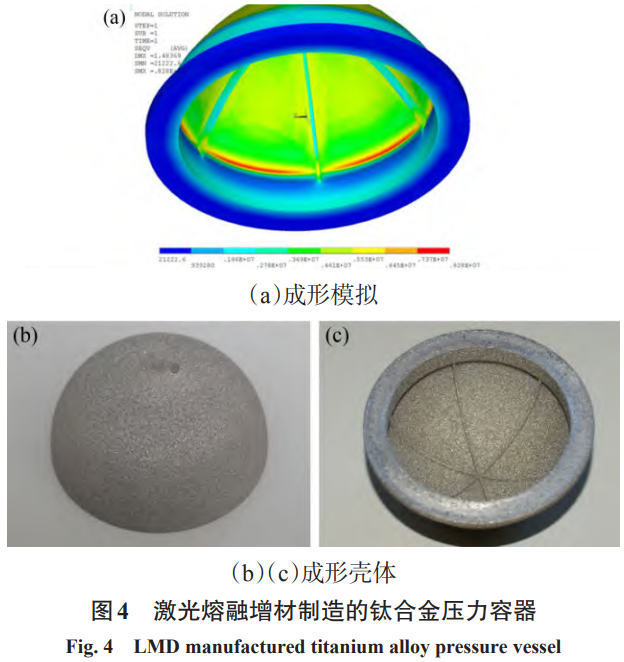
1.3增材制造技術(shù)對(duì)材料成分及性能的滿足性
航空航天行業(yè)的增材制造經(jīng)驗(yàn)和大量的研究結(jié)果能夠證明,通過(guò)該技術(shù)加工的零部件的化學(xué)成分和力學(xué)性能是可以保證的[24]。水下裝備用鈦合金材料主要是α鈦合金和α+β鈦合金,以TA2和TC4最為常見(jiàn),材料的性質(zhì)采用GJB944A-2018的要求,如表2所示。
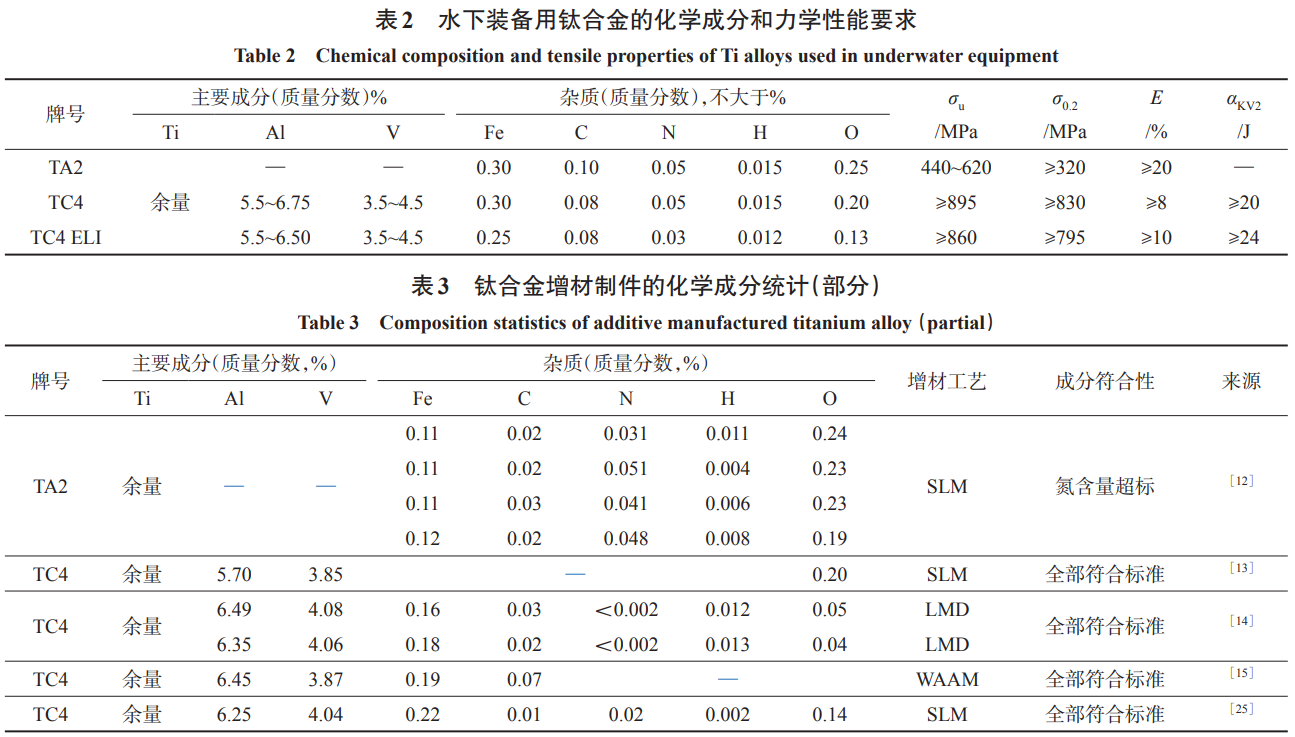
本文統(tǒng)計(jì)了部分關(guān)于TA2和TC4增材制件的元素含量測(cè)試的研究結(jié)果,如表3所示??梢钥闯?,三種主要增材制造技術(shù)獲得的樣件在化學(xué)成分上都能達(dá)到標(biāo)準(zhǔn)要求,并且沒(méi)有出現(xiàn)成分偏析問(wèn)題。
TC4增材制件抗拉強(qiáng)度和斷裂延伸率的統(tǒng)計(jì)結(jié)果如圖5所示,SLM的性能最好[26],其次是LMD[14]和電子束熔絲增材(EBM)[27],都能完全滿足標(biāo)準(zhǔn)要求。對(duì)于WAAM[28],需要在特定工藝窗口下才能達(dá)到標(biāo)準(zhǔn)要求。值得注意的是,對(duì)于TC4鈦合金增材制件,沖擊功普遍較鍛件低,表現(xiàn)出一定的脆性。
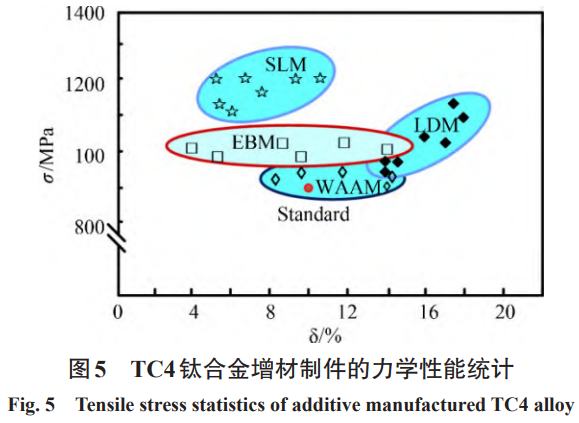
2、增材制造技術(shù)鈦合金應(yīng)用研究現(xiàn)狀
針對(duì)增材制造(AM)中TC4鈦合金的應(yīng)用,目前在生物醫(yī)學(xué)、航空航天以及汽車行業(yè)的研究和應(yīng)用已經(jīng)取得了顯著的進(jìn)展。在生物醫(yī)學(xué)領(lǐng)域,AM技術(shù)被廣泛應(yīng)用于定制化植入物的制造,包括但不限于牙科植入物、顱骨修復(fù)板、下頜骨假體、頸椎融合器械、骨盆植入物、髖關(guān)節(jié)和踝關(guān)節(jié)假體等[29-31]。得益于鈦合金卓越的生物相容性和機(jī)械性能,使其成為生物醫(yī)學(xué)領(lǐng)域植入材料的優(yōu)選。AM技術(shù)能夠依據(jù)患者的具體情況,定制出完美匹配的植入物,極大地提升了手術(shù)效果和患者康復(fù)速度。
在航空航天領(lǐng)域,AM技術(shù)則主要用于生產(chǎn)性能要求極高、工作環(huán)境極端的零部件,如各種發(fā)動(dòng)機(jī)零件、航天器結(jié)構(gòu)構(gòu)件等[32-33]。利用AM技術(shù)可以顯著減少材料浪費(fèi),并能生產(chǎn)出傳統(tǒng)制造方法難以實(shí)現(xiàn)的復(fù)雜結(jié)構(gòu)零件,不僅提升了零件性能,還實(shí)現(xiàn)了質(zhì)量的大幅減輕,這對(duì)追求極致效率和能耗最小化的航空航天產(chǎn)業(yè)至關(guān)重要。
在汽車行業(yè)中,AM技術(shù)則主要應(yīng)用于快速原型制造、復(fù)雜或定制化汽車零件的生產(chǎn),例如制動(dòng)卡鉗、活動(dòng)尾翼支架和尾管裝飾蓋等[34]。在賽車設(shè)計(jì)領(lǐng)域,減重和設(shè)計(jì)自由度的提升尤為關(guān)鍵,AM技術(shù)在這一領(lǐng)域展現(xiàn)出巨大的應(yīng)用潛力。通過(guò)輕量化設(shè)計(jì),可以有效提升燃油經(jīng)濟(jì)性,降低排放,符合汽車產(chǎn)業(yè)的可持續(xù)發(fā)展目標(biāo)。
就海洋鈦合金裝備而言,深海環(huán)境的獨(dú)特條件,如高靜水壓力、低溫和低溶解氧含量,對(duì)水下裝備所用鈦合金的耐腐蝕性提出了挑戰(zhàn)。這些因素可能影響材料的腐蝕行為,尤其是增加了局部腐蝕和應(yīng)力腐蝕開(kāi)裂的風(fēng)險(xiǎn)。Pazhanivel研究表明[35],通過(guò)SLM技術(shù)制備的TC4鈦合金,在NaCl環(huán)境下進(jìn)行慢應(yīng)變速率試驗(yàn)(SSRT)時(shí),其應(yīng)力腐蝕開(kāi)裂敏感性有所增加。這主要?dú)w因于α/β相界面的腐蝕敏感性增加以及氫化物的形成。SLM技術(shù)中的快速冷卻速率促進(jìn)了晶粒細(xì)化,這雖然提高了材料的強(qiáng)度,但也可能導(dǎo)致應(yīng)力腐蝕開(kāi)裂風(fēng)險(xiǎn)的增加。此外,電化學(xué)腐蝕也是深海裝備用鈦合金需要面對(duì)的一個(gè)問(wèn)題,因?yàn)樗赡軐?dǎo)致材料性能下降,甚至危及結(jié)構(gòu)的完整性。Zhou研究發(fā)現(xiàn)[36],無(wú)論是采用單向還是交叉掃描路徑的LMD技術(shù)制造的TC4合金,其耐腐蝕性能都不及傳統(tǒng)鍛造件。LMD過(guò)程中的快速冷卻和不均勻的熱梯度可能導(dǎo)致合金中形成非平衡相,如α'馬氏體,這種相的存在可能會(huì)降低合金的耐腐蝕性。
盡管鈦合金在增材制造過(guò)程中應(yīng)用于水下裝備時(shí)面臨挑戰(zhàn),但這項(xiàng)技術(shù)在提升其耐腐蝕性能方面具有巨大潛力,特別是在海洋領(lǐng)域。隨著對(duì)深海環(huán)境影響的深入研究,有望能夠更好地開(kāi)發(fā)鈦合金材料,推動(dòng)深海裝備技術(shù)的發(fā)展。
3、增材制造技術(shù)在鈦合金水下裝備上應(yīng)用面臨的挑戰(zhàn)
3.1制件應(yīng)力腐蝕開(kāi)裂的風(fēng)險(xiǎn)
對(duì)于水下裝備而言,產(chǎn)品的可靠性是核心要求。前述的適應(yīng)性分析表明增材制造技術(shù)具有相當(dāng)大的優(yōu)越性和力學(xué)可靠性。然而,增材制造技術(shù)也有其固有的孔隙問(wèn)題,盡管有報(bào)道稱增材制造技術(shù)可以產(chǎn)生完全致密的結(jié)構(gòu),但不受控制的孔隙率實(shí)際上在增材制造零件中很常見(jiàn)。
Leuders[37]使用X射線斷層掃描檢測(cè)到SLM制樣的孔隙率為0.23%。Kasperovich和Hausmann[38]報(bào)道,在優(yōu)化的SLM參數(shù)下,孔隙度仍然保持在0.08%左右,并且小尺寸孔隙占據(jù)了相當(dāng)大的體積百分比。即便采用真空電子束熔絲增材(EBM),孔隙也同樣在所難免。Ackelid和Svensson[39]發(fā)現(xiàn)成品EBM零件的孔隙率為0.17%。為了消除孔隙,增材制造零件通常要進(jìn)行后處理。然而,熱處理不能很好使孔隙閉合[37]。熱等靜壓(HIP)對(duì)降低孔隙率有積極作用[40-41],例如,經(jīng)過(guò)HIP處理后,孔隙體積分?jǐn)?shù)從0.08%下降到0.01%,孔隙大小也顯著減小[37]。這些孔隙呈圓形,它們是由于困在熔池中的氣體沒(méi)有及時(shí)逸出[42]。對(duì)于以激光為熱源的增材制造技術(shù),降低掃描速度和提高激光功率會(huì)在一定程度上緩解孔隙的形成,但很難徹底消除孔隙[1]。
孔隙的存在對(duì)制件的拉伸性能不會(huì)產(chǎn)生顯著的影響,但會(huì)嚴(yán)重削弱制件的耐蝕性,特別是考慮到增材制件內(nèi)部的殘余拉應(yīng)力存在,會(huì)進(jìn)一步導(dǎo)致應(yīng)力腐蝕風(fēng)險(xiǎn)。
由于水下裝備是在高鹽度和高外水壓的工況下服役,對(duì)于部件的耐蝕性有嚴(yán)苛的要求,尤其是直接接觸海水的部件。盡管已有大量工作證明了鈦合金的表面會(huì)生成氧化膜緩解自身腐蝕,然而,深海的低溫、低氧、高壓環(huán)境會(huì)阻礙鈦合金表面鈍化膜的生成,同時(shí)加劇裂紋尖端區(qū)溶液Cl濃聚[43]。特別是,當(dāng)pH值<4時(shí),鈦合金鈍化膜會(huì)開(kāi)始溶解。因此,增材制件在深海環(huán)境中的可靠性仍然存在較大風(fēng)險(xiǎn)。
Leon等人[44]對(duì)比了鍛造TC4與SLM制備的TC4在3.5%NaCl溶液中的應(yīng)力腐蝕行為,如圖6所示,顯然,相較于鍛件,增材制件的耐應(yīng)力腐蝕性下降。
3.2大型結(jié)構(gòu)件形性控制難
水下裝備上還存在大量的大型結(jié)構(gòu)件,盡管目前大型金屬件增材技術(shù)取得了一定進(jìn)展,但在大型結(jié)構(gòu)件的增材制造中,形性控制是一個(gè)具有挑戰(zhàn)性的任務(wù)。主要涉及以下兩個(gè)方面的難點(diǎn):
(1)過(guò)熱、變形與熱應(yīng)力誘發(fā)開(kāi)裂。在大型構(gòu)件增材制造過(guò)程中,底層成形金屬會(huì)反復(fù)經(jīng)歷熱循環(huán),容易導(dǎo)致過(guò)熱現(xiàn)象。過(guò)熱會(huì)引起組織異常、非均勻凝固和晶粒長(zhǎng)大,影響構(gòu)件的性能和質(zhì)量。同時(shí)增材過(guò)程中還伴隨較大的瞬時(shí)熱應(yīng)力,構(gòu)件的變形不可避免,嚴(yán)重時(shí)會(huì)導(dǎo)致試件的開(kāi)裂。
(2)金屬流動(dòng)和充實(shí)性。在LMD和WAAM過(guò)程中,熔融金屬通過(guò)噴嘴進(jìn)行噴射,沿著預(yù)定路徑逐層堆疊,并形成固體結(jié)構(gòu)。然而,在大型結(jié)構(gòu)件中,金屬流動(dòng)的距離較長(zhǎng),需要更好地控制充實(shí)性。如果金屬充實(shí)不均勻,可能導(dǎo)致構(gòu)件的內(nèi)部孔洞、空洞和裂紋等質(zhì)量問(wèn)題。
3.3增材制件的評(píng)價(jià)體系缺失
目前,關(guān)于增材制件的評(píng)價(jià)標(biāo)準(zhǔn)和規(guī)范仍不完善,主要表現(xiàn)在:
(1)關(guān)于增材制件的評(píng)價(jià)僅有現(xiàn)行的GB/T39254—2020,其中給出了增材制件的通用評(píng)價(jià)項(xiàng)目,包括拉伸、硬度、彎曲、沖擊、扭轉(zhuǎn)蠕變、疲勞、斷裂韌性、疲勞裂紋擴(kuò)展、彈性模量和泊松比,缺少耐蝕性方面的評(píng)價(jià)指導(dǎo)。
(2)缺乏定量指標(biāo)。在增材制件的評(píng)價(jià)中,許多性能指標(biāo)尚未形成一致的定量標(biāo)準(zhǔn)。例如,缺乏與增材制造過(guò)程中的缺陷密度等相關(guān)的定量評(píng)估方法。這使得很難比較和評(píng)估不同制造商、不同設(shè)備和不同工藝參數(shù)下的增材制件質(zhì)量和性能。
(3)環(huán)境適應(yīng)性評(píng)估缺乏。增材制件在特殊工況下的環(huán)境適應(yīng)性評(píng)估也相對(duì)缺乏。對(duì)于在水下裝備的高鹽度、低溫度、高外水壓服役工況,缺乏相應(yīng)的評(píng)估指標(biāo)和測(cè)試方法來(lái)確定制件可靠性。
這些問(wèn)題不僅是水下裝備面臨的困境,其他領(lǐng)域都有類似的難題,這就要求專業(yè)領(lǐng)域的科研、技術(shù)人員和產(chǎn)品質(zhì)量監(jiān)督者的緊密合作,盡早出臺(tái)相關(guān)的評(píng)價(jià)依據(jù)。
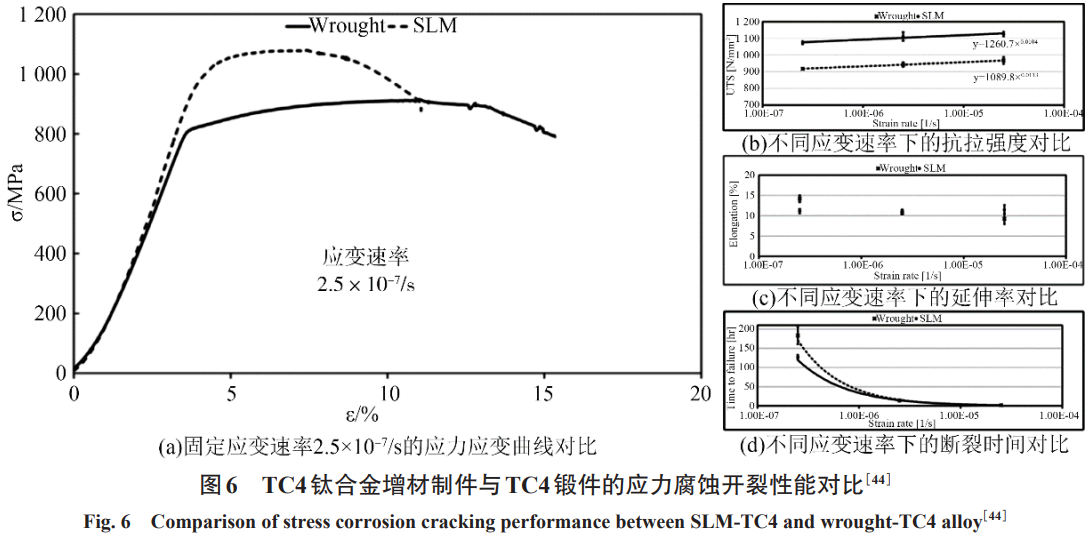
3.4材料與成本問(wèn)題
目前,增材制造所用粉體或絲材仍以目標(biāo)材料為基準(zhǔn)制備而成,并沒(méi)有針對(duì)性地適配不同增材制造工藝所用熱源的特點(diǎn)進(jìn)行開(kāi)發(fā)。此外,相對(duì)于板材而言,增材制造的材料體系仍有較大補(bǔ)充空間。如,水下裝備用TC4ELI鈦合金,目前沒(méi)有相關(guān)的增材制造研究報(bào)道。
在航空航天領(lǐng)域中,部件力學(xué)性能要求高、形狀復(fù)雜且不易用傳統(tǒng)加工方式加工的部件多、部件成形材料價(jià)格高,這些要求與增材制造的特點(diǎn)契合度極高。因此,金屬增材制造技術(shù)得以在航空航天領(lǐng)域取得廣泛應(yīng)用。相比而言,水下裝備的結(jié)構(gòu)復(fù)雜性低,材料價(jià)格也相對(duì)較低,因此,對(duì)于水下裝備而言,增材制造的加工成本仍然偏高,這也是影響增材制造技術(shù)在水下裝備中應(yīng)用的另一因素。
4、結(jié)論與展望
水下裝備的耐壓結(jié)構(gòu)材料正逐漸向鈦合金化轉(zhuǎn)變,這為增材制造技術(shù)的應(yīng)用開(kāi)拓了廣闊的空間。該技術(shù)不僅有望突破傳統(tǒng)熱加工工藝在鈦合金加工上的局限性,而且為水下裝備的設(shè)計(jì)帶來(lái)了前所未有的自由度。隨著國(guó)內(nèi)外對(duì)高端裝備需求的日益增長(zhǎng),特別是在軍事和民用領(lǐng)域?qū)λ卵b備性能要求的不斷提升,鈦合金材料的市場(chǎng)需求預(yù)期將持續(xù)增長(zhǎng)。
增材制造技術(shù)在水下裝備建造中的應(yīng)用展現(xiàn)出顯著的適應(yīng)性,尤其在制造螺旋槳和空心殼體等復(fù)雜結(jié)構(gòu)方面。面對(duì)水下裝備輕量化的發(fā)展趨勢(shì),未來(lái)可能會(huì)看到更多如蒙皮點(diǎn)陣耐壓殼體等創(chuàng)新結(jié)構(gòu)的增材制造應(yīng)用。
盡管如此,增材制造技術(shù)在水下裝備的廣泛應(yīng)用還面臨一系列挑戰(zhàn)。這些挑戰(zhàn)包括但不限于制件的應(yīng)力腐蝕敏感性、大型結(jié)構(gòu)件的形狀與性能控制、制件的質(zhì)量評(píng)價(jià)體系,以及材料成本等方面的問(wèn)題。
盡管存在這些挑戰(zhàn),水下裝備中仍有眾多非觸水部件,如各種支撐結(jié)構(gòu),這些部件完全可以利用增材制造技術(shù)來(lái)制造,以此驗(yàn)證和推進(jìn)增材制造技術(shù)在水下裝備制造中的實(shí)用性。
針對(duì)水下裝備的特殊服役環(huán)境,固相增材制造技術(shù)(例如攪拌摩擦增材技術(shù))由于其在制造過(guò)程中不產(chǎn)生孔隙,能夠?qū)崿F(xiàn)高密度、類似鍛件的組織結(jié)構(gòu),預(yù)計(jì)將在未來(lái)為水下裝備的高質(zhì)量制造提供有力支持。
綜上所述,增材制造技術(shù)在水下鈦合金裝備的建造中具有巨大的潛力和廣闊的發(fā)展前景。隨著技術(shù)的不斷成熟和市場(chǎng)的進(jìn)一步開(kāi)拓,預(yù)期將為水下裝備的設(shè)計(jì)與制造帶來(lái)革命性的變革。
參考文獻(xiàn):
[1] Emmelmann C,Sander P,Kranz J,et al. Laser Additive Manufacturing and Bionics:Redefining Lightweight Design[J]. Physics Procedia,2011,12(1):364-368.
[2] 周洋,孔諒,王敏,等. 鈦及鈦合金焊接接頭腐蝕性能 研究現(xiàn)狀[J]. 電焊機(jī),2018,48(7):46-50+75.
ZHOU Y,KONG L,WANG M,et al.Reserach status of corrosion of Ti and Ti alloy welding joints [J]. Electric Welding Machine,2018,48(07):46-50+75.
[3] 黃瑞生,方乃文,武鵬博,等. 厚壁鈦合金熔化焊接技 術(shù)研究現(xiàn)狀[J]. 電焊機(jī),2022,52(6):10-24.
HUANG R S,F(xiàn)ANG N W,WU P B,et al. Research Status of Thick Plate Titanium Alloy Fusion Welding Technology[J]. Electric Welding Machine,2022,52(6):10-24.
[4] PRASAD A V S R,RAMJI K,DATTA G L. An Experi‐ mental Study of Wire EDM on Ti-6Al-4V Alloy[J]. Procedia Materials Science,2014,5:2567-2576.
[5] GUPTA R K,KUMAR V A,MATHEW C,et al. Strain hardening of Titanium alloy Ti6Al4V sheets with prior heat treatment and cold working[J]. Materials Science &; Engineering A,2016,662:537-550.
[6] 魏玉順,馬青軍,武鵬博,等. TC4鈦合金激光焊接技 術(shù)研究進(jìn)展[J]. 電焊機(jī),2023,53(8):55-66.
WEI Y S,MA Q J,WU P B,et al. Research Progress in Laser Welding Technology of TC4 Titanium Alloy[J]. Electric Welding Machine,2023,53(8):55-66.
[7] HUANG R,RIDDLE M,GRAZIANO D,et al. Energy and emissions saving potential of additive manufactur‐ ing: the case of lightweight aircraft components[J]. Journal of Cleaner Production,2016,135:1559-1570.
[8] HOURMAND M,SARHAN A A D,SAYUTI M,et al. A Comprehensive Review on Machining of Titanium Alloys[J]. Arabian Journal for Science and Engineer‐ ing,2021,46(8):7087-7123.
[9] JOSHI K,PROMOPPATUM P,QUEK S S,et al. Effect of porosity distribution on the strength and strain-tofailure of Laser-Powder Bed Fusion printed Ti-6Al-4V[J]. Additive Manufacturing,2023,74:103738.[10] WAINWRIGHT J,WILLIAMS S,DING J. Refinement of Ti-6Al-4V prior- β grain structure in the asdeposited condition via process control during wiredirect energy deposition[J]. Additive Manufacturing,2023,74:103712.
[11] 王安普,張峰,孫兵兵,等. TC4鈦合金激光金屬沉積 力學(xué)性能各向異性機(jī)理研究[J]. 電焊機(jī),2022,52(4):14-20.
WANG A P,ZHANG F,SUN B B,et al.Study on the Mechanisms of Mechanical Property Anisotropy of TC4 Titanium Alloy by Laser Metal Deposition [J]. Electric Welding Machine,2022,52(4):14-20.
[12] HASIB M T,OSTERGAARD H E,LIU Q,et al. Ten‐ sile and fatigue crack growth behavior of commercially pure titanium produced by laser powder bed fusion ad‐ ditive manufacturing[J].Additive Manufacturing,2021,45:102027.
[13] ZHAO X,LI S,ZHANG M,et al. Comparison of the microstructures and mechanical properties of Ti-6Al4V fabricated by selective laser melting and electron beam melting[J]. Materials &;Design,2016,95(4):21-31.
[14] CHOI Y R,SUN S D,LIU Q,et al. Influence of deposi‐ tion strategy on the microstructure and fatigue proper‐ ties of laser metal deposited Ti-6Al-4V powder on Ti6Al-4V substrate[J]. International Journal of Fatigue,2020,130:105236.
[15] BAMBACH M,SIZOVA I,SYDOW B,et al. Hybrid manufacturing of components from Ti-6Al-4V by metal forming and wire-arc additive manufacturing[J]. Journal of Materials Processing Technology,2020,282:116689.
[16] VEEMAN D,AJITH J,F(xiàn)AHMIDHA A F Y,et al. Wire Arc Additive Manufacturing (WAAM) process of nickel based superalloys–A review[J]. Materials Today:Pro‐ ceedings,2020,21:920-925.
[17] LIU Z,ZHAO D,WANG P,et al. Additive manufactur‐ ing of metals: Microstructure evolution and multistage control[J]. Journal of Materials Science & Technology,2022,100:224-236.
[18] ZHUO Y,YANG C,F(xiàn)AN C,et al. Grain morphology evolution mechanism of titanium alloy by the combina‐ tion of pulsed arc and solution element during wire arc additive manufacturing[J]. Journal of Alloys and Com‐ pounds,2021,888:161641.
[19] WANG X,ZHOU C,LUO M,et al. Fused plus wire arc additive manufacturing materials and energy saving in variable-width thin-walled[J]. Journal of Cleaner Pro‐ duction,2022,373:133765.
[20] LI Y,LI Y,ZHU Y,et al. Hybrid manufacturing by 3D printing: A facile route to fabricate high-performance complex parts of low-fluidity high-entropy alloys[J]. Journal of Physics:Conference Series,2022,2383:012035.
[21] HAMANAKA H,DOI H,YONEYAMA T,et al. Den‐ tal Casting of Titanium and Ni-Ti Alloys by a New Casting Machine[J]. Journal of Dental Research,1989,68(11):1529.
[22] 全球首個(gè)3D打印船舶螺旋槳WAAMpeller正式下線 [J]. 海運(yùn)情報(bào),2018(2):34.
[23] Breddermann K,Drescher P,Polzin C,et al. Printed pressure housings for underwater applications [J]. Ocean Engineering,2016,113:57-63.
[24] BLAKEY-MILNER B,GRADL P,SNEDDEN G,et al. Metal additive manufacturing in aerospace:A review [J]. Materials &;Design,2021,209:110008.
[25] DAI N,ZHANG L C,ZHANG J,et al. Corrosion be‐ havior of selective laser melted Ti-6Al-4 V alloy in NaCl solution[J]. Corrosion Science, 2016, 102:484-489.
[26] SUN Q D,SUN J,GUO K,et al. Influences of process‐ ing parameters and heat treatment on microstructure and mechanical behavior of Ti-6Al-4V fabricated us‐ ing selective laser melting[J]. Advances in Manufactur‐ ing,2022,10(4):520-540.
[27] HRABE N,QUINN T. Effects of processing on micro‐ structure and mechanical properties of a titanium alloy (Ti-6Al-4V) fabricated using electron beam melting (EBM),part 1:Distance from build plate and part size [J]. Materials Science &;Engineering A,2013,573(6):271-277.
[28] Xie Y,Gao M,Wang F D,et al. Anisotropy of fatigue crack growth in wire arc additive manufactured Ti6Al-4V[J]. Materials Science and Engineering:A,2018,709:265-269.
[29] RUBBERT R. Customized dental prosthesis for peri‐ odontal or osseointegration and related systems and methods:US8602780[P].
[30] CHOWDHURY S,ARUNACHALAM N. Surface func‐ tionalization of additively manufactured titanium alloy for orthopaedic implant applications[J]. Journal of Manufacturing Processes,2023,102:387-405.
[31] HAO Y L,LI S J,YANG R. Biomedical titanium alloys and their additive manufacturing[J].Rare Metals,2016,35(09):661-671.
[32] PASANG T,BUDIMAN A S,WANG J C,et al. Addi‐ tive manufacturing of titanium alloys-Enabling remanufacturing of aerospace and biomedical components[J]. Microelectronic Engineering,2023,270:111935.
[33] WARYOBA D R,KEIST J S,RANGER C,et al. Im‐ pact of hot isostatic pressing on the mechanical and mi‐ crostructural properties of additively manufactured Ti6Al-4V fabricated using directed energy deposition[J]. Materials Science and Engineering A,2018,734:310323.
[34] DEBROY T,WEI H L,ZUBACK J S,et al. Additive manufacturing of metallic components-Process,struc‐ ture and properties[J]. Progress in Materials Science,2018,92:112-224.
[35] PAZHANIVEL B,SATHIYA P,MUTHURAMAN K,et al. Influence of NaCl environment on stress corrosion cracking of additive manufactured Ti-6Al-4V alloy[J]. Engineering Failure Analysis,2021,127:105515.
[36] ZHOU X,XU D,GENG S,et al. Mechanical proper‐ ties, corrosion behavior and cytotoxicity of Ti-6Al-4V alloy fabricated by laser metal deposition[J]. Materials Characterization,2021,179:111302.
[37] LEUDERS S,THOENE M,RIEMER A,et al. On the mechanical behaviour of titanium alloy TiAl6V4 manu‐ factured by selective laser melting:Fatigue resistance and crack growth performance[J]. International Jour‐ nal of Fatigue,2013,48(3):300-307.
[38] KASPEROVICH G,HAUSMANN J. Improvement of fatigue resistance and ductility of TiAl6V4 processed by selective laser melting[J]. Journal of Materials Pro‐ cessing Tech,2015,220:202-214.
[39] K?rner C. Additive manufacturing of metallic components by selective electron beam melting—a review[J]. International Materials Reviews,2016,61(5),361-377.
[40] HRABE N,GNAEUPEL-HEROLD T,QUINN T. Fa‐ tigue properties of a titanium alloy (Ti-6Al-4V) fabri‐ cated via electron beam melting (EBM):Effects of in‐ ternal defects and residual stress[J]. International Jour‐ nal of Fatigue,2017,94(2):202-210.
[41] QIU C L,ADKINS N J,ATTALLAH M M. Microstruc‐ ture and tensile properties of selectively laser-melted and of HIPed laser-melted Ti-6Al-4V[J]. Materials Science and Engineering:A,2013,578:230-239.
[42] GALARRAGA H,LADOS D A,DEHOFF R R,et al. Effects of the microstructure and porosity on properties of Ti-6Al-4V ELI alloy fabricated by electron beam melting (EBM)[J]. Additive Manufacturing,2016,10:47-57.
[43] LIU R,CUI Y,LIU L,et al. A primary study of the ef‐ fect of hydrostatic pressure on stress corrosion cracking of Ti-6Al-4V alloy in 3.5% NaCl solution[J]. Corro‐ sion Science,2020,165:108402.
[44] LEON A,KATARIVAS LEVY G,RON T,et al. The ef‐ fect of strain rate on stress corrosion performance of Ti6Al4V alloy produced by additive manufacturing pro‐ cess[J]. Journal of Materials Research and Technol‐ ogy,2020,9(3):4097-4105.
相關(guān)鏈接