在航空與船舶領(lǐng)域,鈦棒、鈦鍛件及鈦板三類型材憑借差異化工藝與性能特征,形成互補(bǔ)性技術(shù)布局。?鈦棒?多采用TC4(Ti-6Al-4V)或TA17(Ti-4Al-2V)材質(zhì),通過熔煉、鍛造或擠壓成型,抗拉強(qiáng)度≥895 MPa,屈服強(qiáng)度≥825 MPa,滿足ISO 5832-3外科植入物級(jí)標(biāo)準(zhǔn)及ASTM B348棒材規(guī)范,其低溫韌性(-196℃沖擊功≥25 J)與高比強(qiáng)度(鋼的2倍)使其成為飛機(jī)起落架軸桿、船舶推進(jìn)器主軸的優(yōu)選材料?。?鈦鍛件?通過自由鍛或模鍛工藝實(shí)現(xiàn)晶粒細(xì)化,以TC4、Ti-75(Ti-6Al-2Nb-1Ta-0.8Mo)為代表,晶粒尺寸控制在5-20 μm,抗疲勞強(qiáng)度較鑄造件提升30%以上,且殘余應(yīng)力降低至≤50 MPa,符合ASTM B381鍛件標(biāo)準(zhǔn),適用于航空發(fā)動(dòng)機(jī)高壓壓氣機(jī)盤、艦船深海耐壓殼體等關(guān)鍵承力部件?。?鈦板?以TA1/TA2工業(yè)純鈦及TC4合金為主流,采用熱軋+冷軋復(fù)合工藝,厚度精度達(dá)±0.05 mm,表面粗糙度Ra≤1.6 μm,執(zhí)行ASTM B265板材標(biāo)準(zhǔn),兼具耐海水腐蝕(腐蝕速率≤0.0015 mm/a)與電磁屏蔽特性,廣泛用于飛機(jī)蒙皮、船舶艙壁及聲吶導(dǎo)流罩?。
從材質(zhì)演進(jìn)看,航空領(lǐng)域正向高強(qiáng)β鈦合金(如TB8/TB9系列)傾斜,其抗拉強(qiáng)度突破1200 MPa,同時(shí)通過Al-Mo-Si系合金優(yōu)化實(shí)現(xiàn)600℃長(zhǎng)期耐熱性;船舶領(lǐng)域則聚焦TA17、Ti-31(Ti-3Al-2.5V)等焊接友好型合金,焊縫強(qiáng)度系數(shù)≥0.9,適應(yīng)大型艦體分段建造需求?。執(zhí)行標(biāo)準(zhǔn)體系呈現(xiàn)軍民融合趨勢(shì),航空領(lǐng)域在GB/T 3620.1基礎(chǔ)上引入AMS 4928(航空用鈦板)、AMS 6945(高強(qiáng)鈦棒)等軍標(biāo),船舶領(lǐng)域則強(qiáng)化GB/T 3621與DNVGL-OS-C401船級(jí)社規(guī)范的協(xié)同認(rèn)證?。工藝創(chuàng)新方面,鈦棒精密冷軋技術(shù)可將直徑公差壓縮至±0.02 mm,減少后續(xù)機(jī)加工量;鈦鍛件近凈成形技術(shù)使材料利用率從60%提升至85%,結(jié)合等溫鍛造工藝可將變形溫度波動(dòng)控制在±10℃以內(nèi),保障組織均勻性;鈦板超塑性成形(SPF)技術(shù)利用850℃下延伸率≥300%的特性,實(shí)現(xiàn)復(fù)雜曲面一體成型,減重效果達(dá)20%-30%?。未來發(fā)展趨勢(shì)將聚焦低成本化(如低合金化TA系列替代TC4)、功能集成化(如鈦板-復(fù)合材料層壓結(jié)構(gòu))及智能化制造(鍛造過程數(shù)字孿生模擬),推動(dòng)鈦材在航空發(fā)動(dòng)機(jī)整體葉盤、船舶氫燃料儲(chǔ)罐等尖端場(chǎng)景的深度滲透?。
以下是中揚(yáng)金屬針對(duì)航空與船舶領(lǐng)域用鈦棒、鈦鍛件、鈦板三種型材的對(duì)比分析,從形態(tài)工藝、性能特點(diǎn)、應(yīng)用場(chǎng)景、執(zhí)行標(biāo)準(zhǔn)及發(fā)展趨勢(shì)等維度展開:
一、材質(zhì)對(duì)比
型材類型 | 常用鈦合金牌號(hào) | 材質(zhì)特性 | 典型應(yīng)用場(chǎng)景 |
鈦棒 | TC4(Ti-6Al-4V) | 綜合性能優(yōu)異(抗拉≥895MPa),耐高溫(400℃),中等塑性 | 航空發(fā)動(dòng)機(jī)軸、船舶液壓管路 |
TA2(工業(yè)純鈦) | 高耐蝕性(C5級(jí)環(huán)境)、低強(qiáng)度(抗拉≥345MPa),易加工 | 船舶海水泵閥桿、航空非承力支架 |
鈦鍛件 | TC11(Ti-6.5Al-3.5Mo-1.5Zr) | 高溫性能強(qiáng)(500℃長(zhǎng)期使用),抗蠕變 | 航空發(fā)動(dòng)機(jī)渦輪盤、船舶曲軸鍛件 |
Ti-5Al-2.5Sn | 焊接性好,低溫韌性優(yōu)異(-196℃) | 航天低溫燃料儲(chǔ)罐、極地破冰船部件 |
鈦板 | TA1/TA2(工業(yè)純鈦) | 高成形性(延伸率≥25%),耐點(diǎn)蝕 | 船舶耐壓殼體、航空機(jī)艙防火隔板 |
TC4(Ti-6Al-4V) | 高比強(qiáng)度(抗拉≥950MPa),抗疲勞 | 艦載機(jī)蒙皮、潛艇聲吶導(dǎo)流罩 |
二、應(yīng)用前景對(duì)比
型材類型 | 航空領(lǐng)域前景 | 船舶領(lǐng)域前景 |
鈦棒 | 新增長(zhǎng)點(diǎn): | 新增長(zhǎng)點(diǎn): |
- 超音速客機(jī)發(fā)動(dòng)機(jī)高壓轉(zhuǎn)子(耐溫>600℃) | - 深海采礦船機(jī)械臂驅(qū)動(dòng)軸(抗高壓腐蝕) |
- 電動(dòng)飛機(jī)輕量化導(dǎo)電鈦棒(替代銅合金) | - 氫燃料船低溫液氫輸送管(防氫脆) |
鈦鍛件 | 技術(shù)趨勢(shì): | 技術(shù)趨勢(shì): |
- 等溫鍛造工藝普及(β相區(qū)控形,提升組織均勻性) | - 大型LNG船雙燃料發(fā)動(dòng)機(jī)曲軸一體化鍛造(單件重量>20噸) |
- 3D打印預(yù)成型毛坯(減少材料損耗) | - 耐蝕-耐磨復(fù)合鍛件(表面滲氮處理) |
鈦板 | 創(chuàng)新方向: | 創(chuàng)新方向: |
- 超薄鈦板(0.1mm)用于柔性機(jī)翼蒙皮(可變形飛行器) | - 超寬幅鈦板(寬度>4m)用于全鈦船體外殼(減少焊接縫) |
- 高導(dǎo)熱鈦板(摻雜石墨烯)用于熱防護(hù)系統(tǒng) | - 鈦-鋼復(fù)合板(爆炸焊接)降低成本
|
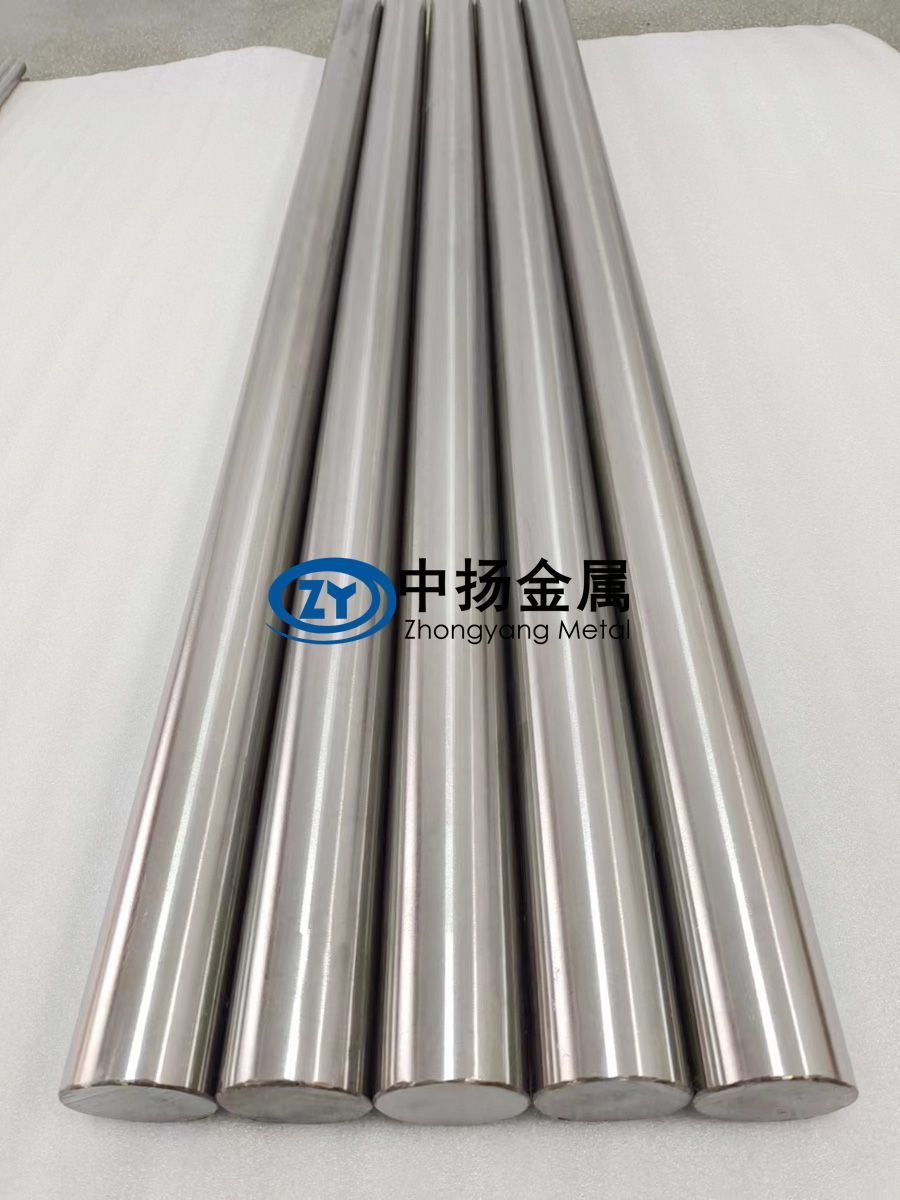
三、綜合對(duì)比表(含材質(zhì)與前景)
維度 | 鈦棒 | 鈦鍛件 | 鈦板 |
核心材質(zhì) | TC4(60%)、TA2(30%)、TA18(Ti-3Al-2.5V,10%) | TC11(50%)、TC4(30%)、Ti-1023(β鈦合金,20%) | TA1/TA2(70%)、TC4(25%)、TA9(Ti-0.2Pd,5%) |
未來技術(shù) | 納米晶鈦棒(ECAP工藝提升強(qiáng)度30%) | 增材制造+鍛造復(fù)合工藝(縮短交付周期50%) | 激光沖擊強(qiáng)化鈦板(疲勞壽命提升2倍) |
市場(chǎng)預(yù)測(cè) | 2025年航空需求增長(zhǎng)25%(C919量產(chǎn)驅(qū)動(dòng)) | 船舶鍛件市場(chǎng)規(guī)模達(dá)$8億(2027年,LNG船擴(kuò)產(chǎn)) | 艦艇鈦板滲透率超40%(替代傳統(tǒng)HY-80鋼) |
環(huán)保挑戰(zhàn) | 熔煉能耗高(需推廣氫能電弧爐) | 鍛模壽命短(研發(fā)陶瓷涂層模具) | 酸洗廢液處理(推廣干式噴砂替代工藝) |
四、形態(tài)與制造工藝對(duì)比
型材類型 | 形態(tài)特征 | 核心制造工藝 | 典型加工流程 |
鈦棒 | 圓柱/方棒狀,直徑10mm~500mm | 熔煉鑄造→熱軋/冷拉→矯直 | 真空電弧熔煉→鍛造開坯→多道次軋制→表面車光 |
鈦鍛件 | 異形結(jié)構(gòu)(如法蘭、軸類) | 自由鍛/模鍛→熱處理→機(jī)加工 | 鈦錠加熱→鍛壓成型(變形量>50%)→去氧化皮→精銑 |
鈦板 | 薄板/中厚板,厚度0.5mm~100mm | 熱軋→冷軋→退火→表面處理 | 鑄錠熱軋至坯板→多道次冷軋(厚度公差±0.05mm)→酸洗 |
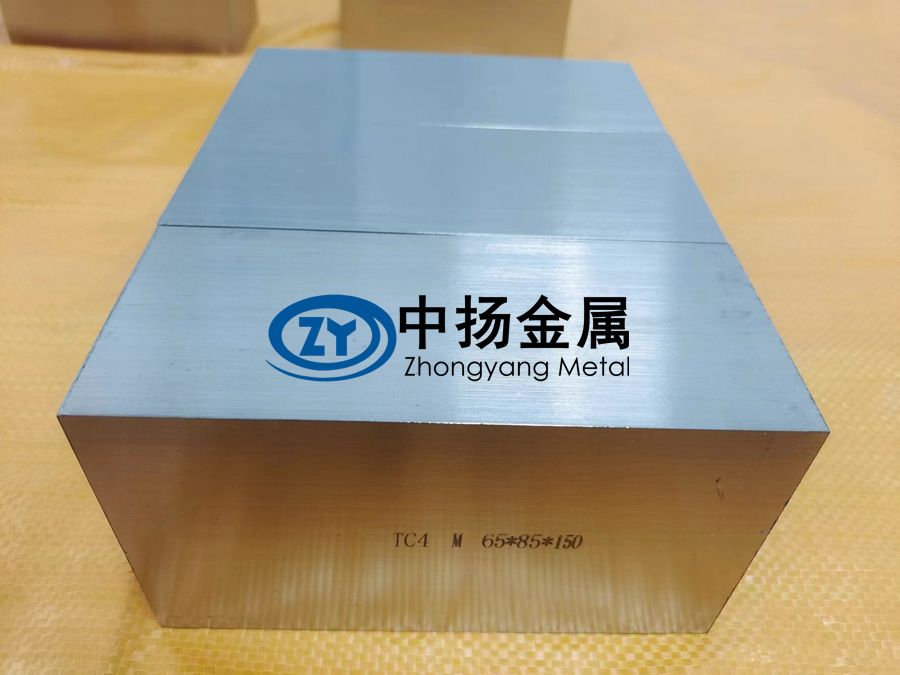
五、性能與材料特性對(duì)比
性能指標(biāo) | 鈦棒 | 鈦鍛件 | 鈦板 |
強(qiáng)度 | 中等(如TC4抗拉≥895MPa) | 最高(鍛造細(xì)化晶粒,TC4鍛件抗拉≥1100MPa) | 適中(冷軋態(tài)抗拉≥950MPa) |
各向異性 | 低(軋制方向均勻) | 可控(通過鍛造流線設(shè)計(jì)優(yōu)化方向性) | 較高(軋制方向強(qiáng)度↑15%) |
耐腐蝕性 | 均勻耐蝕(鹽霧測(cè)試>5000h) | 局部易因殘余應(yīng)力引發(fā)微區(qū)腐蝕(需噴丸強(qiáng)化) | 表面氧化膜致密(耐海水腐蝕等級(jí)C5-M) |
疲勞壽命 | 中高(S-N曲線斜率-0.1) | 最高(鍛造消除缺陷,疲勞極限≥500MPa) | 中(表面劃痕敏感,需拋光處理) |
六、應(yīng)用場(chǎng)景與典型案例
應(yīng)用領(lǐng)域 | 鈦棒典型應(yīng)用 | 鈦鍛件典型應(yīng)用 | 鈦板典型應(yīng)用 |
航空領(lǐng)域 | 發(fā)動(dòng)機(jī)壓氣機(jī)葉片軸(波音787) | 起落架主承力框(空客A350) | 機(jī)身蒙皮(F-22戰(zhàn)斗機(jī)) |
船舶領(lǐng)域 | 潛艇聲吶陣列支架(俄羅斯“北風(fēng)之神”級(jí)) | 螺旋槳葉根鍛件(中國(guó)“蛟龍”號(hào)深潛器) | 船體外殼耐壓板(日本“蒼龍”級(jí)潛艇) |
共性場(chǎng)景 | 液壓管路系統(tǒng)(耐高壓腐蝕) | 閥門閥體(高溫高壓工況) | 防火隔層(艦艇機(jī)艙A60防火分隔) |
七、執(zhí)行標(biāo)準(zhǔn)與檢測(cè)要求
標(biāo)準(zhǔn)維度 | 鈦棒 | 鈦鍛件 | 鈦板 |
國(guó)際標(biāo)準(zhǔn) | AMS 4928(航空級(jí)鈦棒) | AMS 6945(β鈦合金鍛件) | ASTM B265(商用鈦板) |
成分控制 | O≤0.20%、Fe≤0.30%(航空級(jí)) | 雜質(zhì)總量≤0.4%(需真空自耗重熔) | H≤0.015%(防氫脆) |
無損檢測(cè) | 超聲波探傷(Φ≥20mm棒材) | 滲透檢測(cè)(表面裂紋)+X射線(內(nèi)部缺陷) | 渦流檢測(cè)(厚度≤6mm板) |
機(jī)械測(cè)試 | 室溫拉伸+高溫蠕變(發(fā)動(dòng)機(jī)用棒材) | 低周疲勞測(cè)試(循環(huán)次數(shù)>10?) | 杯突試驗(yàn)(冷成型性評(píng)估) |

八、成本與市場(chǎng)趨勢(shì)分析
分析維度 | 鈦棒 | 鈦鍛件 | 鈦板 |
原材料成本 | ¥200~400/kg(TC4) | ¥500~800/kg(模鍛模具費(fèi)占比30%) | ¥150~300/kg(冷軋薄板溢價(jià)高) |
加工損耗率 | 15%~25%(車削余量) | 40%~60%(鍛坯→成品) | 5%~10%(剪切/沖壓成型) |
技術(shù)趨勢(shì) | 精密冷拉技術(shù)(直徑公差±0.02mm) | 等溫鍛造(β相區(qū)變形,提升組織均勻性) | 超寬幅軋制(寬度>3m,減少焊接接頭) |
需求增長(zhǎng)點(diǎn) | 航空發(fā)動(dòng)機(jī)高壓壓氣機(jī)轉(zhuǎn)子(C919增量需求) | 船舶大型曲軸鍛件(LNG船用雙燃料發(fā)動(dòng)機(jī)) | 艦載機(jī)電磁彈射軌道用高導(dǎo)磁鈦板 |
結(jié)論
性能導(dǎo)向:鈦鍛件在高承載關(guān)鍵部件不可替代,鈦板側(cè)重輕量化與耐蝕覆蓋,鈦棒適合軸類/管系;
成本結(jié)構(gòu):鍛件因模具和材料損耗成本最高,板材規(guī)模化生產(chǎn)更具經(jīng)濟(jì)性;
技術(shù)迭代:航空領(lǐng)域推動(dòng)鈦棒精密化(納米晶強(qiáng)化),船舶領(lǐng)域需求超厚鈦板(>80mm);
選型策略:
航空優(yōu)先:鍛件(結(jié)構(gòu)件)>鈦板(蒙皮)>鈦棒(次承力件);
船舶優(yōu)先:鈦板(耐壓殼)>鈦棒(管路)>鍛件(推進(jìn)系統(tǒng))。
相關(guān)鏈接